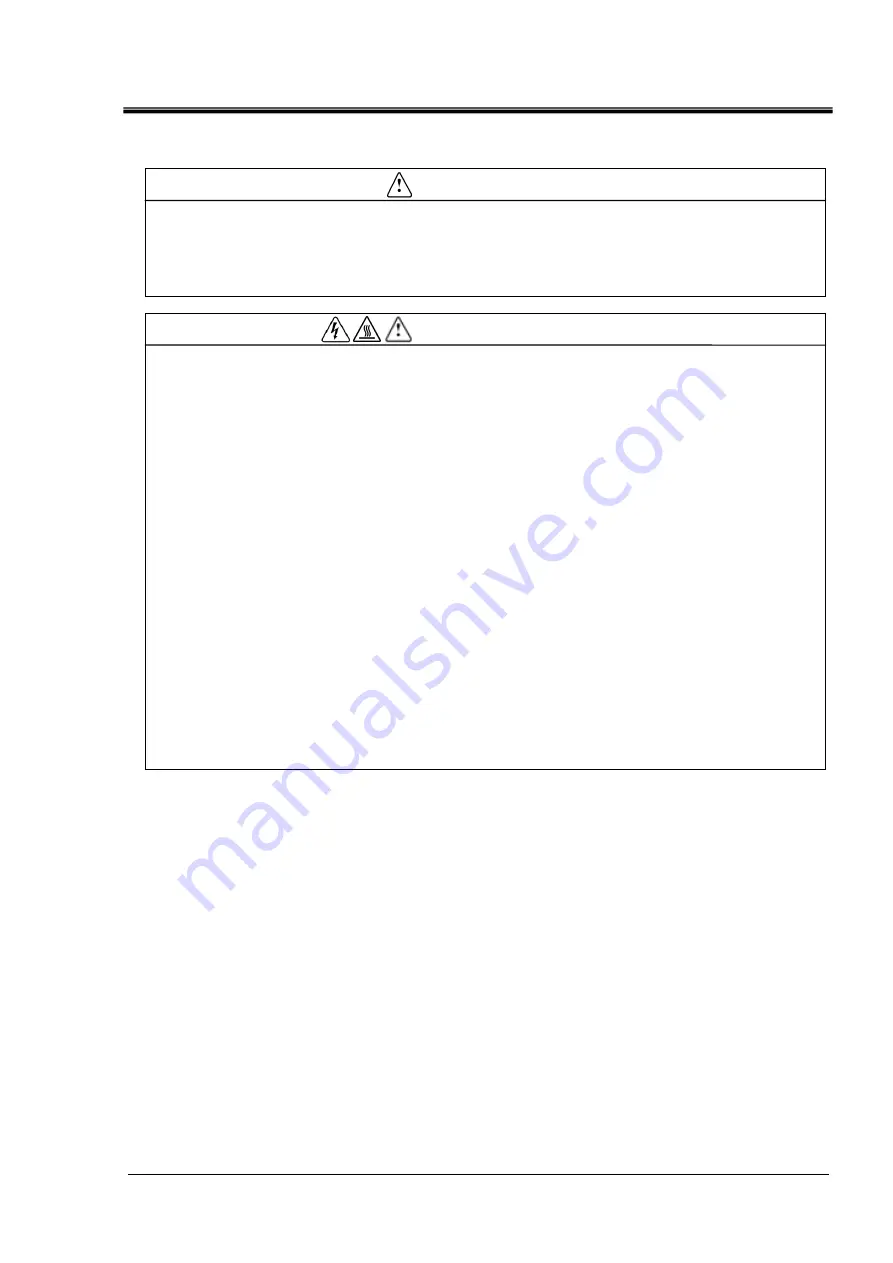
IDX-OM-V020
Chapter
5
Checks and Maintenance
IDFA60/70/80/90 Series
5.1
Daily inspection
5-1
Chapter 5 Checks and Maintenance
5.1 Daily inspection
Before daily operation, check the following points. When any abnormality is found, stop operation
immediately and refer to the Chapter 6 Troubleshooting.
- There should be no leakage of compressed air.
- The lamp is on during operation.
- Confirm that condensate comes out of the drain tube.
- The evaporation thermometer is in the green area.
- There should be no abnormality with noise or vibration from the product.
- There should be no smell or smoke from the product.
DANGER
- Cut off the power supply upstream when removing the panel.
- Before replacing or cleaning parts, be sure to bleed compressed air remaining inside of the
product until the gauge indicates “0”.
Do not remove the auto drain case assembly with any air pressure remaining internally. If
there is residual pressure in the product, there would be great danger of an unexpected
accident, such as shooting out of parts when they are being unscrewed.
- Power supply parts become hot and will be applied with high voltage during operation. Heat
may cause burns, or electric shock can result due to high voltage. Even if the switch with
lamp is turned off and the operation is stopped, electricity will be applied to the primary
line. During the work for primary line, turn off the electrical leakage breaker of the user's
equipment.
- Even if the device operation stops, there is a danger of burns due to residual heat. Do not
start working on the parts inside the product until the temperature has decreased to 50°C or
less. Guideline: 10 to 15 minutes
- There is the possibility of contacting the condensate during the auto drain maintenance
work. Follow the procedure that you define to keep the worker safe.
(eg. Put on protective glasses, apron, and gloves).
- Use an aqueous solution of neutral detergent for cleaning of the auto drain and do not use
solvents.
- When removing the panels and auto drain case assembly, wear protective gloves to prevent
injuries from sharp edges.
- Only people who have sufficient knowledge and experience about the product and its
incidental devices are allowed to perform maintenance.
- Before maintenance, read and understand the important cautionary notifications in this
operation manual.
WARNING
Summary of Contents for IDFA60-23-A
Page 36: ...IDX OM V020 Chapter 7 Documents 7 5 Air Refrigerant Circuit IDFA60 70 80 90 Series 7 6...
Page 52: ......
Page 53: ......