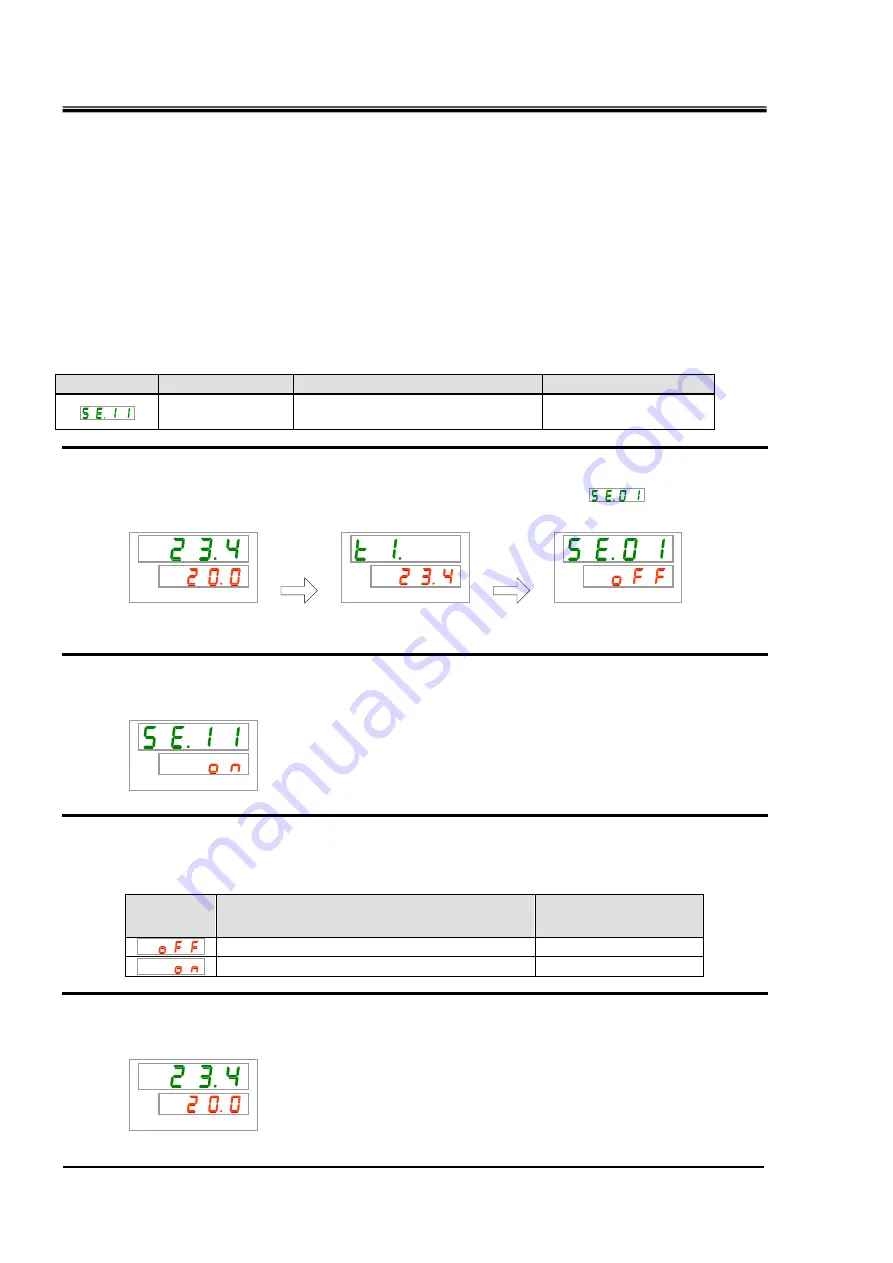
HRX-OM- T002
Chapter 5 Display and setting of various functions
5.12
Key Operation Sound Setting
HRS090 Series
5-32
5.12 Key Operation Sound Setting
5.12.1 Key operation sound setting
Operation sound (click sound) of the buttons on the operation panel can be set
ON/OFF.
Default setting is button operation
sound “ON”.
5.12.2 Setting/checking of the button operation sound
The table below shows the set item for button operation sound and the default setting.
Table 5.12-1 Set item for button operation sound
Display
Item
Contents
Default
Button operation
sound
Sets
button
operation
sound
ON/OFF.
ON
1.
Press and hold the [MENU] button for approximately 2 seconds.
Repeat pressing the button until the button-lock setting screen [
] appears on the
digital display.
PV
SV
PV
SV
PV
SV
Setting/Checking: Button operation sound
2.
Press the [SEL] button 10 times.
Setting screen of button operation sound appears on the digital display.
PV
SV
3.
Set the button operation sound On/OFF with [
▲] button or [▼] button, and press the
“SEL” button to enter.
Table 5.12-2 Setting for button operation sound
Set value
Explanation
Default
Button operation sound OFF
Button operation sound ON
✓
4.
Press the [MENU] button once.
Returns to the main display (which shows the circulating fluid temperature).
PV
SV
Press and
hold [MENU]
key.
Press and
hold [MENU]
key.