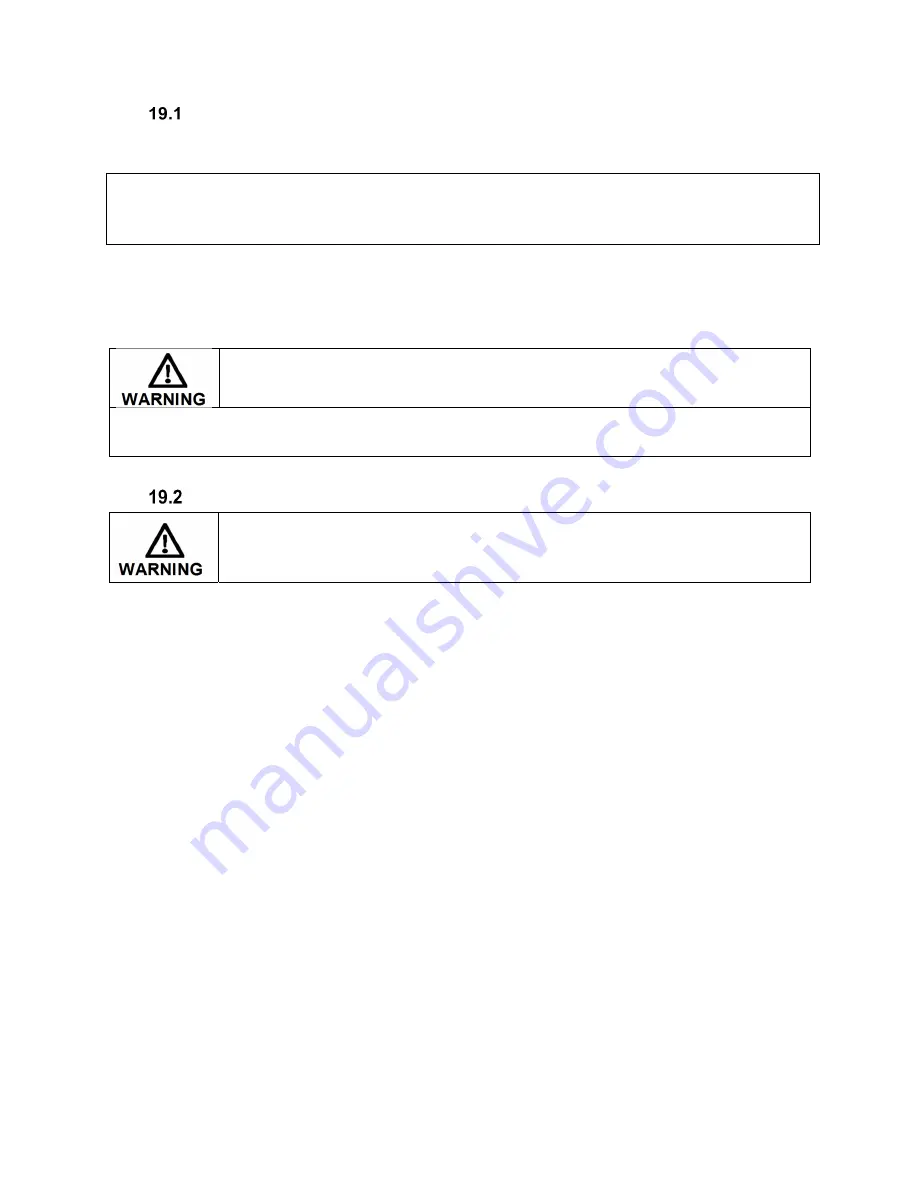
E93.1601EN032.C VGH installation manual
108
19 INSPECTION,
MAINTENANCE
AND
SERVICE.
General
For a good, safe and long-time operation of the boiler and to maintain warranty it is mandatory to carry out
inspection, maintenance and service on the boiler at least once a year.
Inspection, maintenance and service of the boiler must also be carried out on the following occasions:
When a number of similar error codes and/or lock-outs appear.
At least every twelve months maintenance must be done to ensure safe and efficient operation.
Damage caused by the lack of maintenance will not be covered under warranty
Service intervals
The normal service frequency for the boiler is once a year. Every year the boiler must be cleaned and checked,
according to the maintenance procedures. If there is doubt whether the boiler is operating with the correct water
and/or combustion air quality, it is advised that a first check is already executed after six months. This check
serves to determine the frequency of the future services. The maximum interval between two services is one year.
INSPECTION, MAINTENANCE AND SERVICE MUST BE EXECUTED FOR A SAFE AND
EFFICIENT OPERATION OF THE BOILER.
“Caution: Label all wires prior to disconnection when servicing controls. Wiring errors can cause improper and
dangerous operation.
“Verify proper operation after operation servicing.”
Safety instructions Crystalline Silica
Refractory Insulation
The refractory insulation of the heat exchanger (located on the rear wall inside the heat exchanger and burner
door) must be inspected. If this insulation disk shows any signs of (water) damage or degradation it must be
exchanged. Also check if there are any indications in the burner room of a high condensate level (caused by a
blocked condensate trap) that might have wetted the rear wall insulation. When this has happened, the rear wall
insulation must also be replaced.
Only use the insulation disk that is supplied by the boiler manufacturer.
The same procedure must be applied on the insulation and gaskets fitted on the burner door.
Refractory Ceramic Fibers (RFC)
Personal Protective Equipment Required -
Read the following warnings and handling instructions carefully
before commencing any service work in the combustion chamber. The insulating material on the inside of the
burner plate and the rear combustion chamber wall contain
Refractory Ceramic Fibers
and must never be handled
without personal protective equipment. When disturbed as a result of servicing, these substances become
airborne and, if inhaled, may be hazardous to your health.
Potential Carcinogen
- Use of
Refractory Ceramic Fibers
in high temperature applications (above 1805 °F) can
result in the formation of Crystalline Silica (cristobalite), a respirable silica dust. Repeated airborne exposure to
crystalline silica dust may result in chronic lung infections, acute respiratory illness, or death. Crystalline silica is
listed as a (potential) occupational carcinogen by the following regulatory organizations:
International Agency for
Research on Cancer (IARC),
Canadian Centre for Occupational Health and Safety (CCOHS), Occupational Safety
and Health Administration (OSHA), and National Institute for Occupational Safety and Health (NIOSH). Failure to
comply with handling instructions in Table 19.1
may result in serious injury or death.
Crystalline Silica
- Certain components in the combustion chamber may contain this potential carcinogen. Read
warnings and handling instructions pertaining to Refractory Ceramic Fibers before commencing service work in
the combustion chamber. Take all necessary precautions and use recommended personal protective equipment
as required see Table 19.1. Installation and service must be performed by a qualified installer, service agency or
the gas supplier who must read and follow the Installation, Operation, and Service Manual before performing any
work on this boiler. Improper installation, adjustment, alteration, service or maintenance can cause property
damage, serious injury (exposure to hazardous materials) or death.
Warning
Crystalline Silica
–
Read instructions below carefully
Summary of Contents for VGH-299-CH
Page 6: ...E93 1601EN032 C VGH installation manual 6 1 SAFETY GUIDELINES ...
Page 59: ...E93 1601EN032 C VGH installation manual 59 Ladder Logic Diagram Figure 11 3 ...
Page 60: ...E93 1601EN032 C VGH installation manual 60 Electrical schematics Figure 11 4 ...
Page 61: ...E93 1601EN032 C VGH installation manual 61 Figure 11 5 ...
Page 123: ...E93 1601EN032 C VGH installation manual 123 22 SPARE PARTS Figure 22 1 ...
Page 124: ...E93 1601EN032 C VGH installation manual 124 Figure 22 2 ...
Page 127: ...E93 1601EN032 C VGH installation manual 127 ...