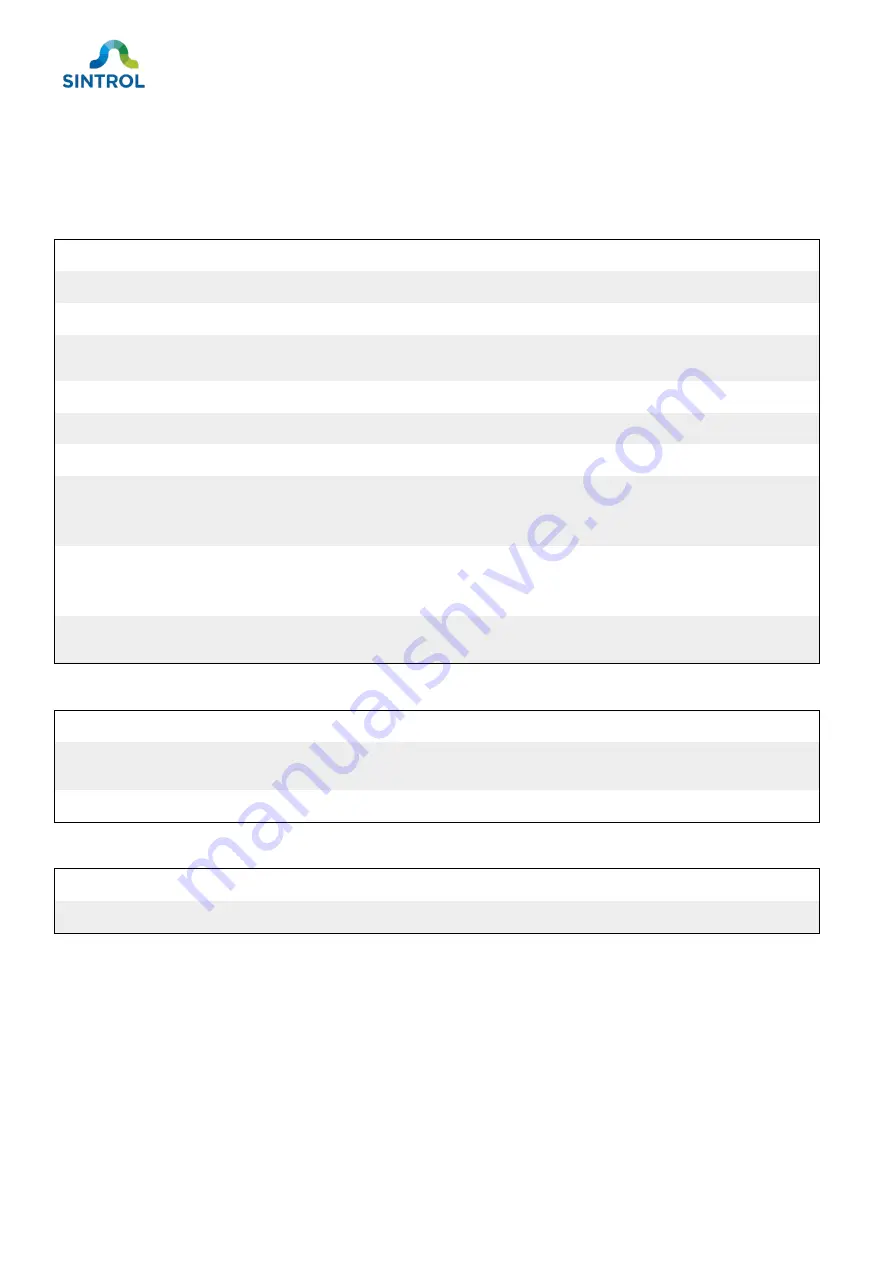
©2021 Sintrol.
All rights reserved.
98 (104)
Revision 4
12
Specifications
For dimensional drawings, see section
General information
Product name:
DumoPro
Measured objects:
Total suspended particles (TSP)
Measurement principle:
Inductive electrification
Measurement range:
Detection limit 0.01 mg/m
3
Max. range up to several g/m
3
depending on operating conditions
Ingress protection:
IP66
Power supply requirements:
24 V DC ±10%
Power consumption:
Up to 10 W
Output signals:
•
2 × Independent solid-state relays, max. 30 V DC / 1 A
•
Isolated active 4 ... 20 mA output loop,
max. loop resistance 250 Ω
Communication interface:
•
Serial communication RS-485
•
USB
•
Radio frequency*
Communication protocol:
•
Modbus RTU (with RS-485)
•
Sintrol network (with USB, RF and RS-485)
Physical characteristics
Enclosure:
Aluminum and stainless steel (316L)
Wetted parts:
•
Probe: Stainless steel (316L)
•
Insulation: Teflon
Weight:
4.20 kg (9.26 lb)
Ambient conditions
Temperature:
−40 ... 60 °C (−40 ... 140 °F)
Humidity:
Max. 95 % relative humidity (non-condensing)
* Requires optional RF antenna