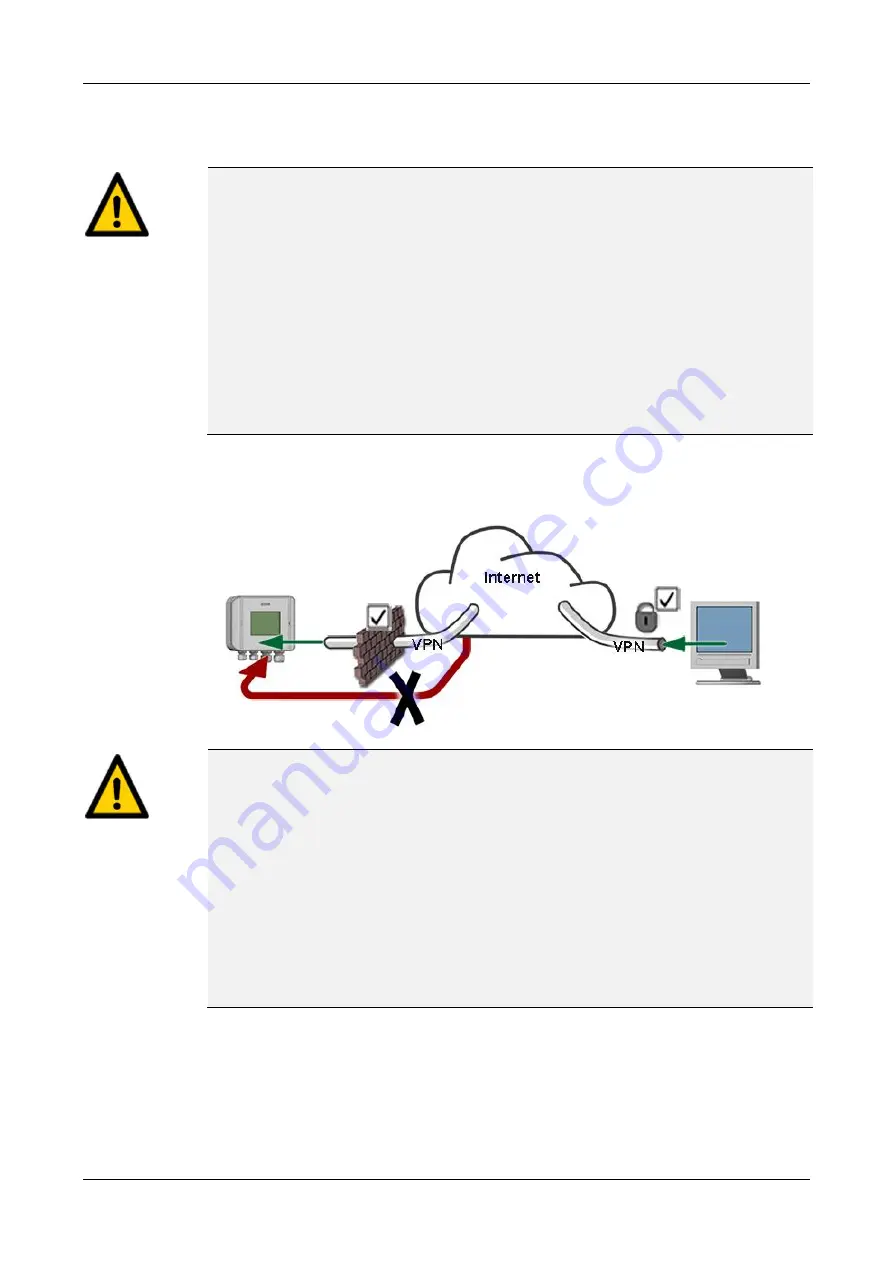
General safety points
Instruction Manual ScrubberGuard
14830E/1
27
3.5
Warning and danger symbols on the instrument
WARNING!
There are no warning or danger symbols on the instrument.
Users must ensure that they observe the safety measures as specified in the Instruction Man-
ual at all times when working with the instrument and its peripheral equipment, even if no
warning or danger symbols are attached to the instrument.
The following sections must be internalized:
Section 1.8
Section 1.11
Section 1.13
Section 3.1
Section 3.4
Observe safety pointers when performing the described procedures.
Observe local safety pointers.
3.6
Preventing undesirable online access attempts
WARNING!
SIGRIST instruments are equipped with an integrated web user interface and Mod-
bus TCP interface, thus offering state-of-the-art administration and control possibil-
ities. However, if these are connected directly to the Internet, then any Internet us-
er can in principle access your instrument and change the configuration.
Please note the following points to prevent this:
Never connect the instrument directly to the Internet.
Operate it behind a firewall and block access to the instrument.
Only connect to branch offices via VPN.
Change the standard password on commissioning.
Always keep up to date with the latest changes regarding Internet security so that you
can react promptly in the event of alterations.
Install the latest updates immediately (also for the router and firewall).
Summary of Contents for AquaScat SG
Page 6: ......