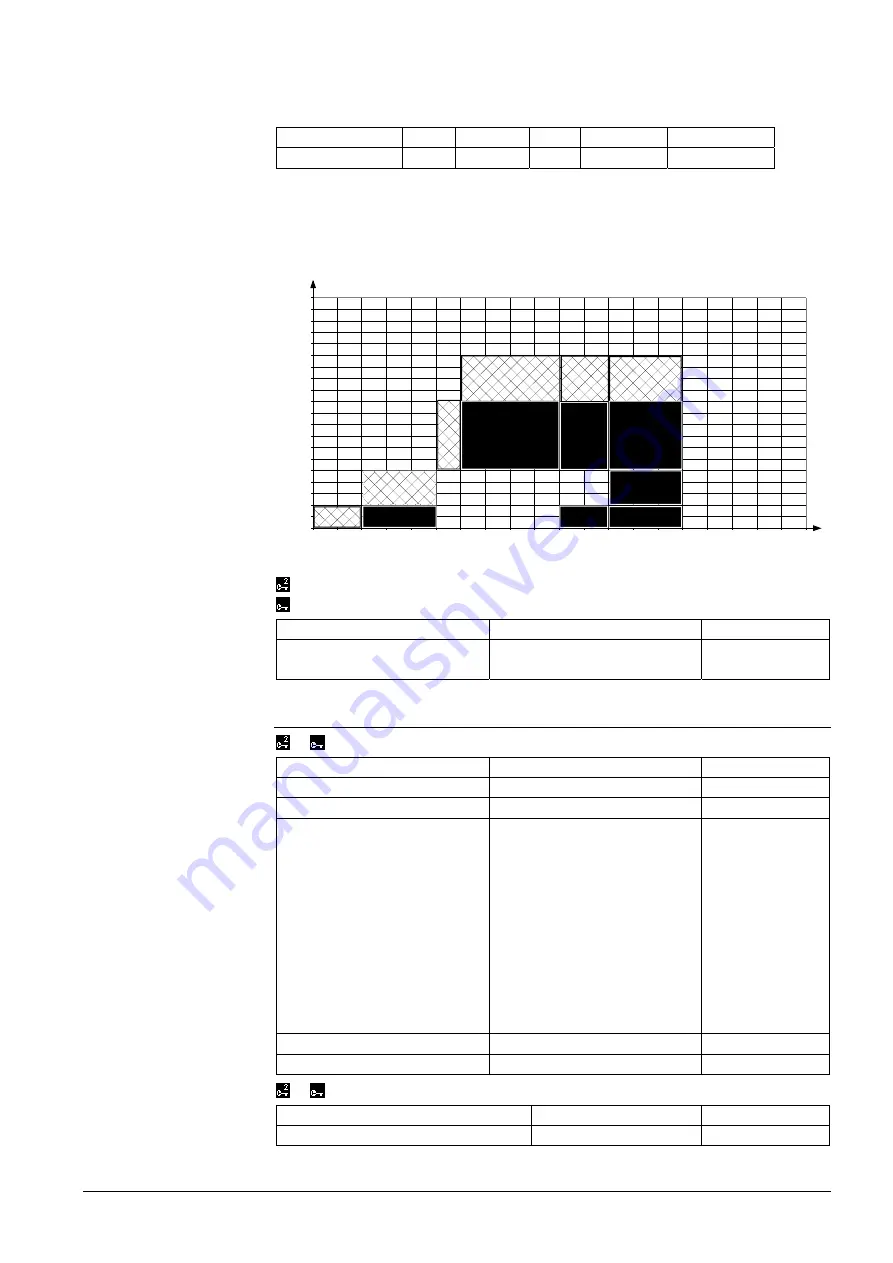
83/232
Building Technologies
Boiler sequence controller RMK770
CE1P3132en
HVAC Products
6 Boiler sequence management
23.04.2009
This approach can be chosen only if the output of the basic stage of boiler 2 exceeds
the rated capacity of boiler 1. If this strategy is chosen, a fixed boiler sequence makes
sense, thereby ensuring that the same boiler is always boiler no. 2.
Output stage
1 2
3 4
5
Boiler release
1.1 1.1+1.2 2.1 2.1+2.2 1.1+2.1+2.2
This switch-on order is called binary switching on. With the RMK770, binary switching
on is restricted to the first 2 boilers. The next boilers are switched sequentially. With
binary switching on, boiler 2 is always the controlling boiler.
Binary switching of boiler sequence with 2 boilers:
Output of boiler 1 = 100%, output of boiler 2 = 200%
0
20
40
60
80
100
120
140
160
180
200
220
240
260
280
300
320
340
360
380
400
0
20
40
60
80
100
120
140
160
180
200
220
240
260
280
300
320
340
360
380
400
3132D
03
Heat demand or load
Bo
il
e
r 1
Boil
e
r 2
Main menu > Commissioning > Settings > …
or
Main menu > Settings > Boiler sequence manager > Control parameters
Operating line
Range
Factory setting
Boiler sequence strategy
Sequentially / Binary-
sequentially
Sequentially
6.3.4
Boiler sequence operating mode
or
Main menu > Boiler sequence manager > Boiler sequence optg mode
Operating line
Range
Factory setting
Preselection
Off / Summer operation / Auto
Auto
State
On / Off
Cause Commissioning
Operating mode selector
Frost protection for consumer /
Flow/return frost protection /
Sustained mode
Overtemp protection / Overrun /
Protective boiler startup seq
Flue gas measuring mode
Manual control
No boiler sensor available /
No request / Request
Summer operation
Inactive / Active
Boil sequence selection manual Auto / 1…6
Auto
or
Main menu > Boiler sequence manager > Boiler sequence optg mode
Operating line
Range
Factory setting
Setp preselection manual
---- / 8…140 °C
---- °C
Example