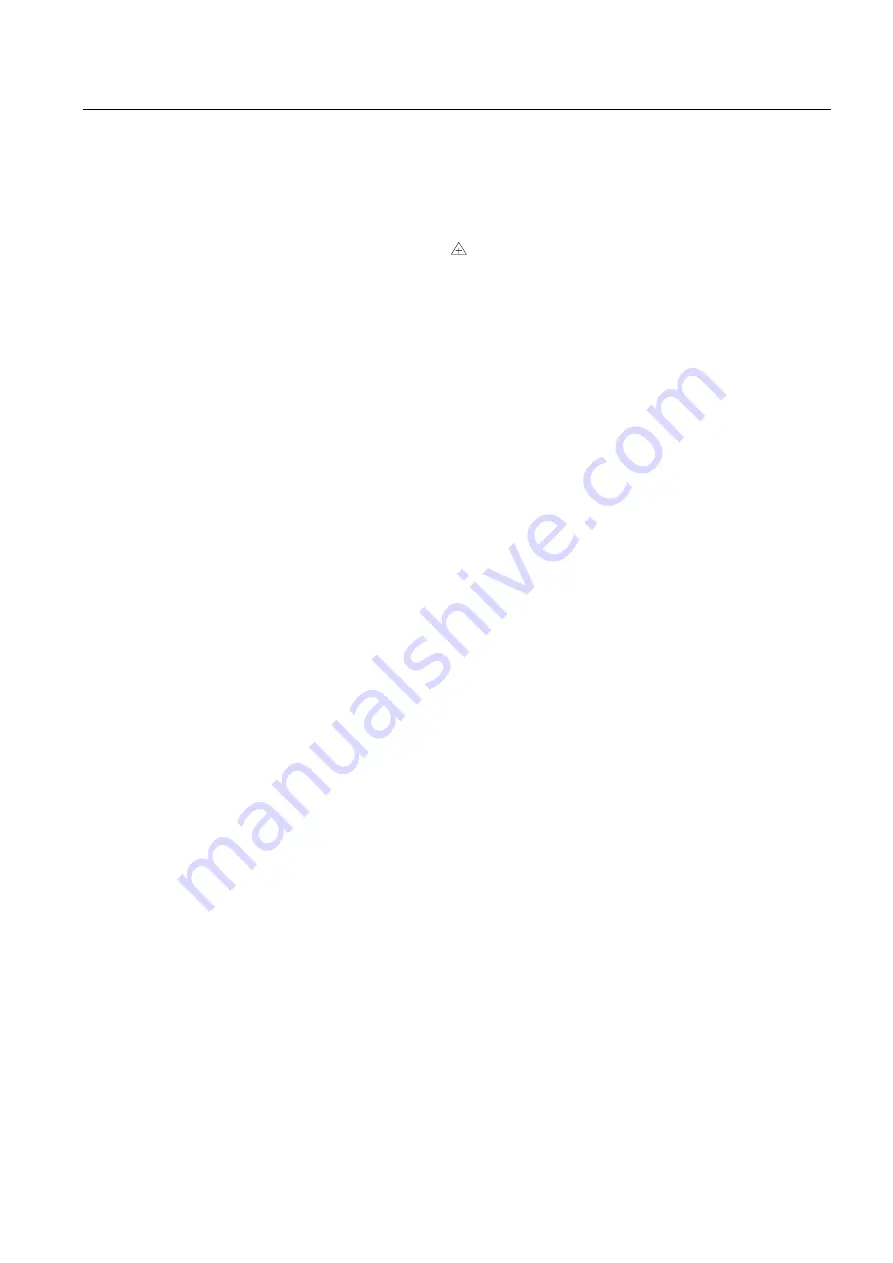
Parameter assignment/Addressing
10.2 Description of parameters
SIPART PS2 with PROFIBUS communication
Operating Instructions, 09/2007, A5E00127926-07
161
Example: An average actuating time of 1.2 seconds is shown in the digital display as "C 1.2",
where "C" stands for "calculated". The average actuating time can be used as a reference
step time. However, it merely represents a rough standard value.
Set the sub-parameters "A1" to "A5" as per your requirements. Then start measuring the
reference step time by pressing the increment button for at least five seconds. The digital
display shows "rEAL" during these five seconds.
The device then moves to the set start position automatically and executes the desired jump.
The current position in percent is continuously shown on the digital display. "inPST" for
"initialize partial stroke test" appears in the lower line of the digital display. When the test is
completed, the measured reference step time in seconds is shown on the digital display.
"Fdini" is displayed if the start position cannot be approached or the step target cannot be
achieved. "Fdini" stands for "failed PST initialization".
The factory setting is "NOINI".
A7.FACT1 - factor 1
Use this sub-parameter to set the factor for the formation of limit threshold 1. Set the factor in
a range from "0.1" to "100.0". The limit threshold is the product of the reference step time
and "A7.FACT1". The process to determine the reference step time is described under
"A6.PSTIN".
The threshold 1 fault message is displayed when the limit threshold 1 exceeds. The process
to activate and display this fault message is described in the "XDIAG" parameter.
The factory setting is "1.5".
A8.FACT2 - factor 2
Use this sub-parameter to set the factor for the formation of limit threshold 2. Set the factor in
a range from "0.1" to "100.0". The limit threshold is the product of the reference step time
and "A8.FACT2". The process to determine the reference step time is described under
"A6.PSTIN".
The threshold 2 fault message is displayed when the limit threshold 2 exceeds. The process
to activate and display this fault message is described in the "XDIAG" parameter.
The factory setting is "3.0".
A9.FACT3 - factor 3
Use this sub-parameter to set the factor for the formation of limit threshold 3. Set the factor in
a range from "0.1" to "100.0". The limit threshold is the product of the reference step time
and "A9.FACT32". The process to determine the reference step time is described under
"A6.PSTIN".
The threshold 3 fault message is displayed when the limit threshold 3 exceeds. The process
to activate and display this fault message is described in the "XDIAG" parameter.
If the time threshold exceeds, the control signal of the actuator is simultaneously cancelled to
prevent a sticky or rusty valve, if any, from breaking off and overshooting.
The partial stroke test is then interrupted temporarily, a threshold 3 fault message is
reported, and the actuator is moved back to its start position.
The factory setting is "5.0".