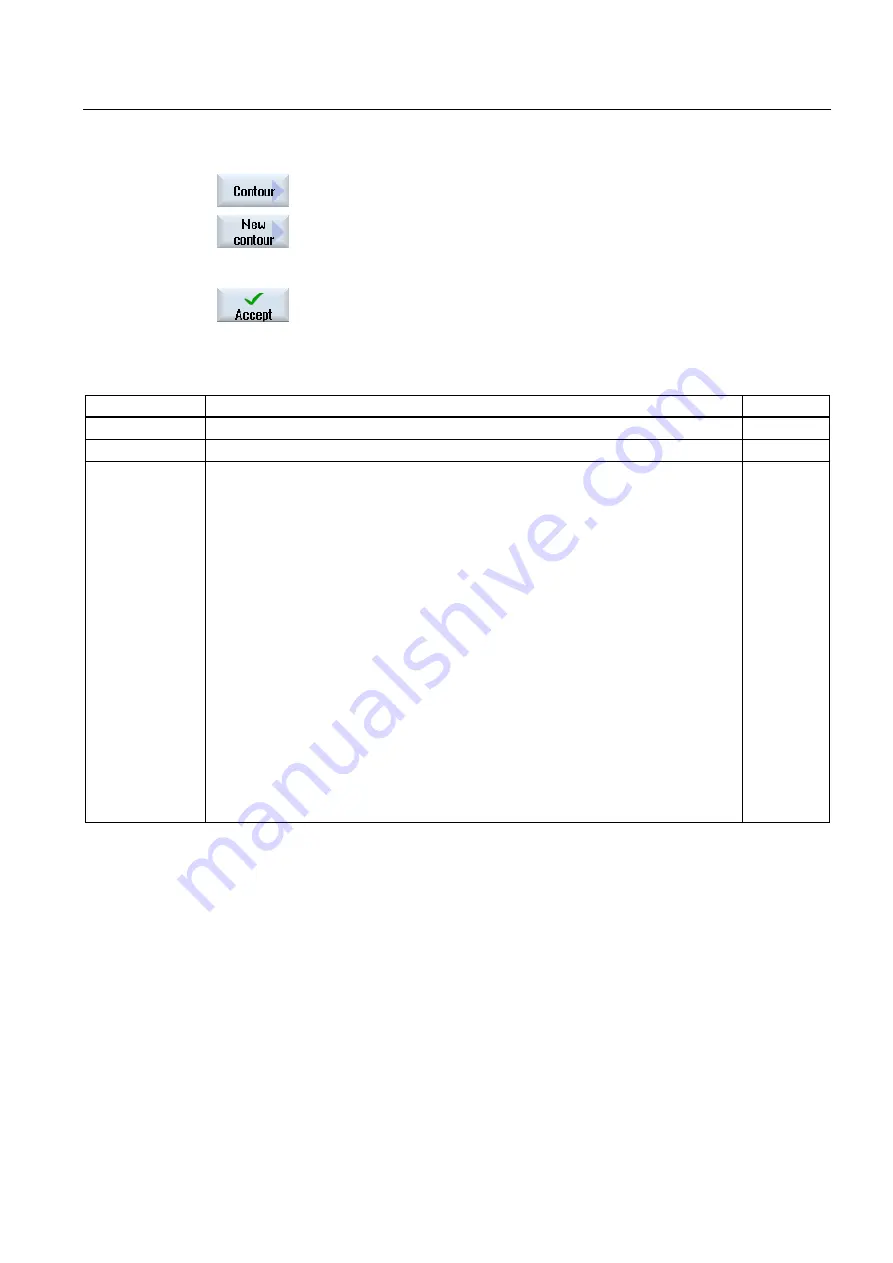
Programming technological functions (cycles)
8.5 Contour turning - only for G code programs
Milling
Operating Manual, 03/2010, 6FC5398-7CP20-1BA0
381
3.
Press the "Contour" and "New contour" softkeys.
The "New Contour" input window opens.
4.
Enter a name for the new contour. The contour name must be unique.
5.
Press the "Accept" softkey.
The input window for the starting point of the contour appears.
Enter the individual contour elements (see Section "Creating contour
elements").
Parameter
Description
Unit
Z
Starting point Z (abs)
mm
X
Starting point X ∅ (abs)
mm
Additional
commands
You can enter additional commands in the form of G code for each contour element.
You can enter the additional commands (max. 40 characters) in the extended
parameter screens ("All parameters" softkey). The softkey is always available at the
starting point, it only has to be pressed when entering additional contour elements.
You can program feedrates and M commands, for example, using additional G code
commands. However, carefully ensure that the additional commands do not collide with
the generated G code of the contour and are compatible with the machining type
required. Therefore, do not use any G code commands of group 1 (G0, G1, G2, G3), no
coordinates in the plane and no G code commands that have to be programmed in a
separate block.
The contour is finished in continuous-path mode (G64). As a result, contour transitions
such as corners, chamfers or radii may not be machined precisely.
If you wish to avoid this, then it is possible to use additional commands when
programming.
Example: For a contour, first program the straight X parallel and then enter "G9" (non-
modal exact stop) for the additional command parameter. Then program the Z-parallel
straight line. The corner will be machined exactly, as the feedrate at the end of the X-
parallel straight line is briefly zero.
Note:
The additional commands are only effective for finishing!
Summary of Contents for SINUMERIK 840D
Page 6: ...Preface Milling 6 Operating Manual 03 2010 6FC5398 7CP20 1BA0 ...
Page 50: ...Introduction 1 4 User interface Milling 50 Operating Manual 03 2010 6FC5398 7CP20 1BA0 ...
Page 600: ...Appendix A 2 Overview Milling 600 Operating Manual 03 2010 6FC5398 7CP20 1BA0 ...
Page 610: ...Index Milling 610 Operating Manual 03 2010 6FC5398 7CP20 1BA0 ...