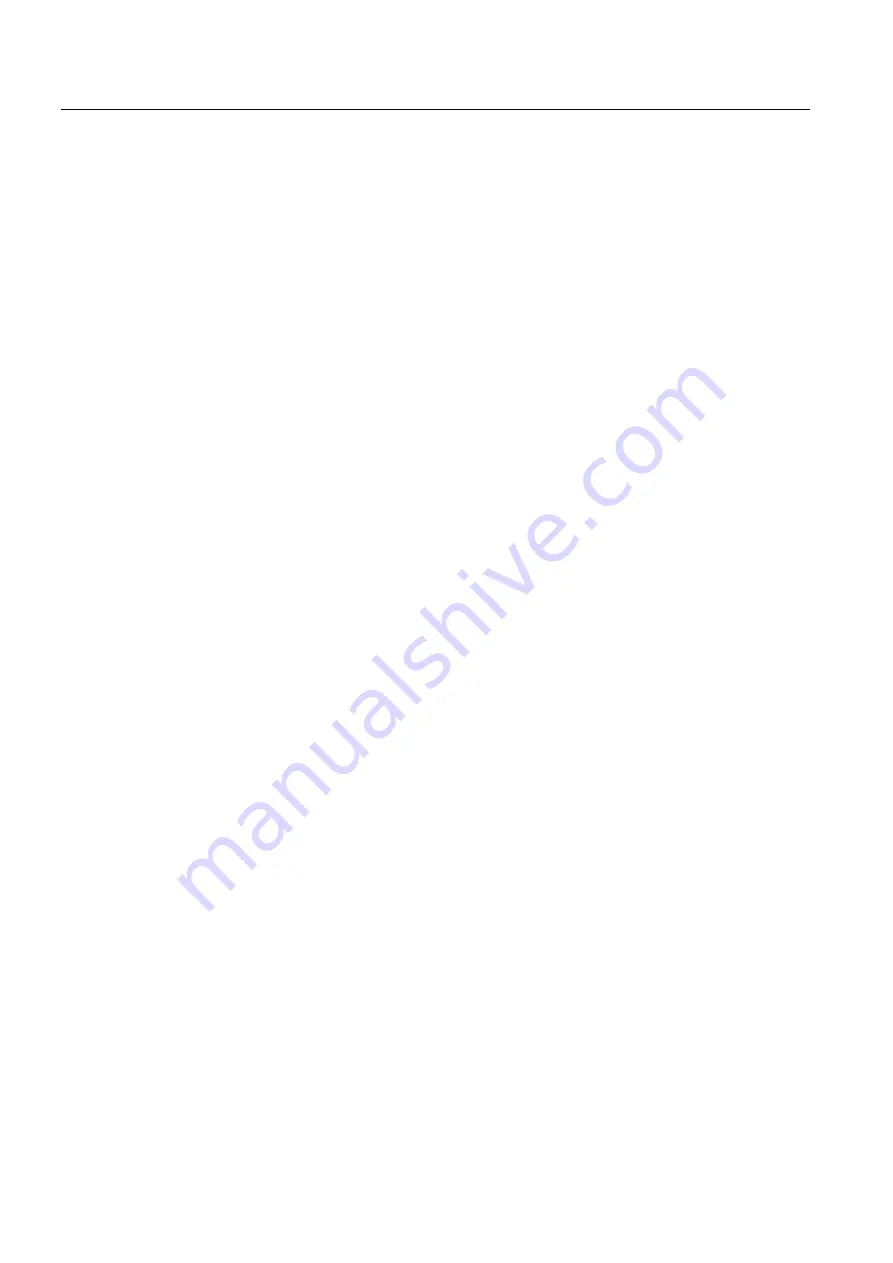
Programming technological functions (cycles)
8.5 Contour turning - only for G code programs
Milling
382
Operating Manual, 03/2010, 6FC5398-7CP20-1BA0
8.5.4
Creating contour elements
Creating contour elements
After you have created a new contour and specified the starting point, you can define the
individual elements that make up the contour.
The following contour elements are available for the definition of a contour:
●
Straight vertical line
●
Straight horizontal line
●
Diagonal line
●
Circle/arc
For each contour element, you must parameterize a separate parameter screen. Parameter
entry is supported by various help screens that explain the parameters.
If you leave certain fields blank, the cycle assumes that the values are unknown and
attempts to calculate them from other parameters.
Conflicts may result if you enter more parameters than are absolutely necessary for a
contour. In such a case, try entering less parameters and allowing the cycle to calculate as
many parameters as possible.
Contour transition elements
As transition element between two contour elements, you can select a radius or a chamfer
or, in the case of linear contour elements, an undercut. The transition element is always
attached at the end of a contour element. The contour transition element is selected in the
parameter screen of the respective contour element.
You can use a contour transition element whenever there is an intersection between two
successive elements which can be calculated from the input values. Otherwise you must use
the straight/circle contour elements.
Additional commands
You can enter additional commands in the form of G code for each contour element. You
can enter the additional commands (max. 40 characters) in the extended parameter screens
("All parameters" softkey).
You can program feedrates and M commands, for example, using additional G code
commands. However, make sure that the additional commands do not collide with the
generated G code of the contour. Therefore, do not use any G code commands of group 1
(G0, G1, G2, G3), no coordinates in the plane and no G code commands that have to be
programmed in a separate block.
Summary of Contents for SINUMERIK 840D
Page 6: ...Preface Milling 6 Operating Manual 03 2010 6FC5398 7CP20 1BA0 ...
Page 50: ...Introduction 1 4 User interface Milling 50 Operating Manual 03 2010 6FC5398 7CP20 1BA0 ...
Page 600: ...Appendix A 2 Overview Milling 600 Operating Manual 03 2010 6FC5398 7CP20 1BA0 ...
Page 610: ...Index Milling 610 Operating Manual 03 2010 6FC5398 7CP20 1BA0 ...