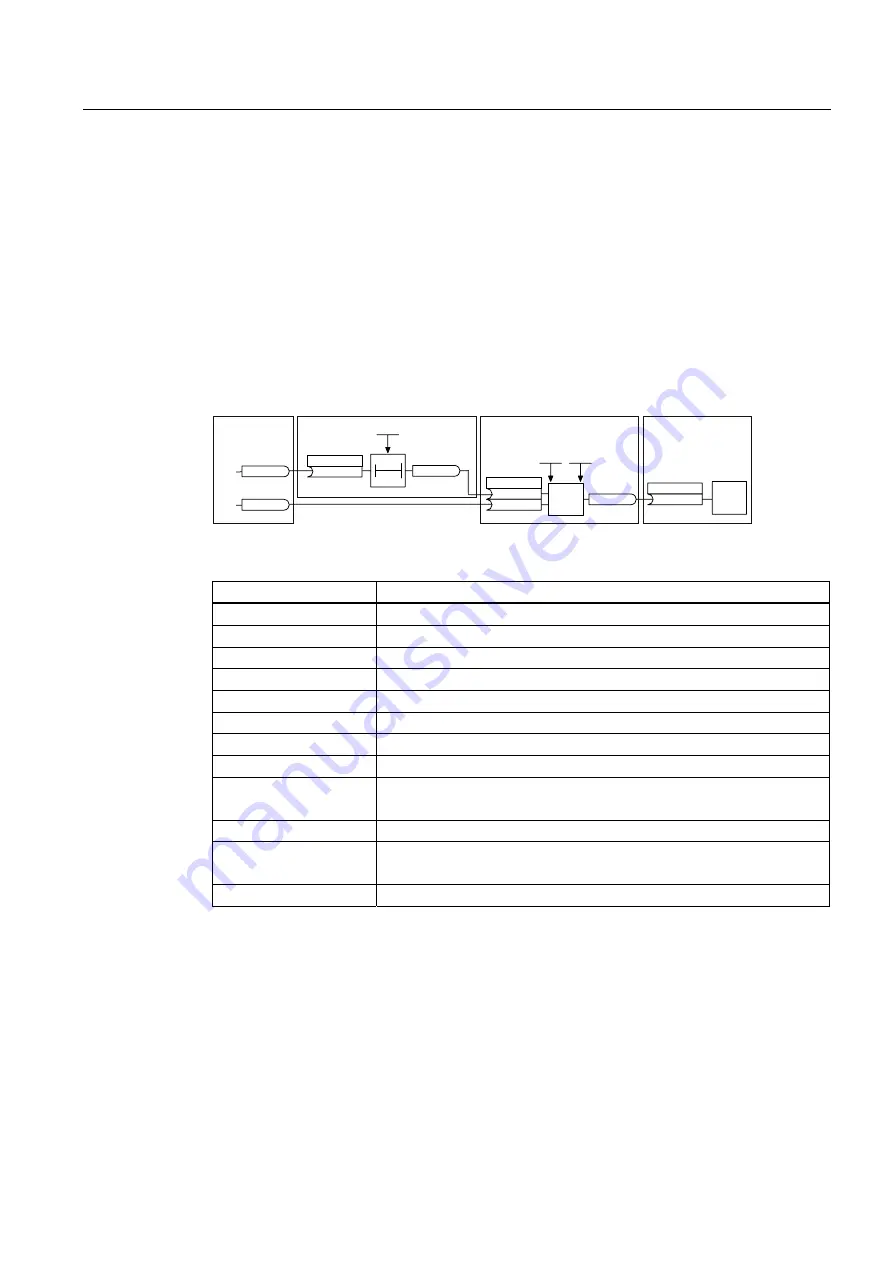
Introduction
1.4 Extended adaptation options using BICO parameters (parameterization for advanced level personnel)
Frequency inverter
Operating Instructions, 08.10. 2008, t.b.d.
19
1.4.2
BICO technology: example
Example: Shifting a basic PLC functionality into the frequency inverter
A conveyor system is to be configured in such a way that it can only start when two signals
are present simultaneously. These could be the following signals, for example:
●
The oil pump is running (the required pressure level is not reached, however, until after
five seconds)
●
The protective door is closed
The task is realized by inserting free blocks between the digital input 0 and the internal ON
command for the motor and interconnecting them.
&
Index [0]
P2810
Index [1]
r0722.0
r0722.1
r2811
Index [0]
P2849
Timer
T
0
P2850 = 5,0 [s]
r2852
Index [0]
P0840
ON/
OFF1
DI 0
DI 1
P2801[0]
P2800
Figure 1-4
Example: Signal interconnection for interlock
Parameter
Description
P0003 = 3
Enable expert access to parameters
P0700 = 2
Select the command source
P0701 (e.g.) = 99
Enable/"open" digital input 0 (DI0) for BICO parameterization
P0702 (e.g.) = 99
Enable/"open" digital input 1 (DI1) for BICO parameterization
P2800 = 1
Group enable all freely-programmable function blocks (FFB)
P2801 [In000] = 1
Individual enable of the AND function block
P2802 [In000] = 1
Individual enable of the TIMER function block
P2850 = 5.0
Set the TIMER delay time: 5 seconds
P2849 = r0722.0
Connect the status of DI0 to the TIMER input
r0722.0 = Parameter that displays the status of digital input 0.
P2810 [In000] = r2852
Connect the TIMER output to the 1st input of the AND
P2810 [In001] = r0722.1 Connect the status of DI1 to the 2nd AND input
r0722.1 = Parameter that displays the status of digital input 1.
P0840 = r2811
Connect the AND output to the control command ON/OFF1