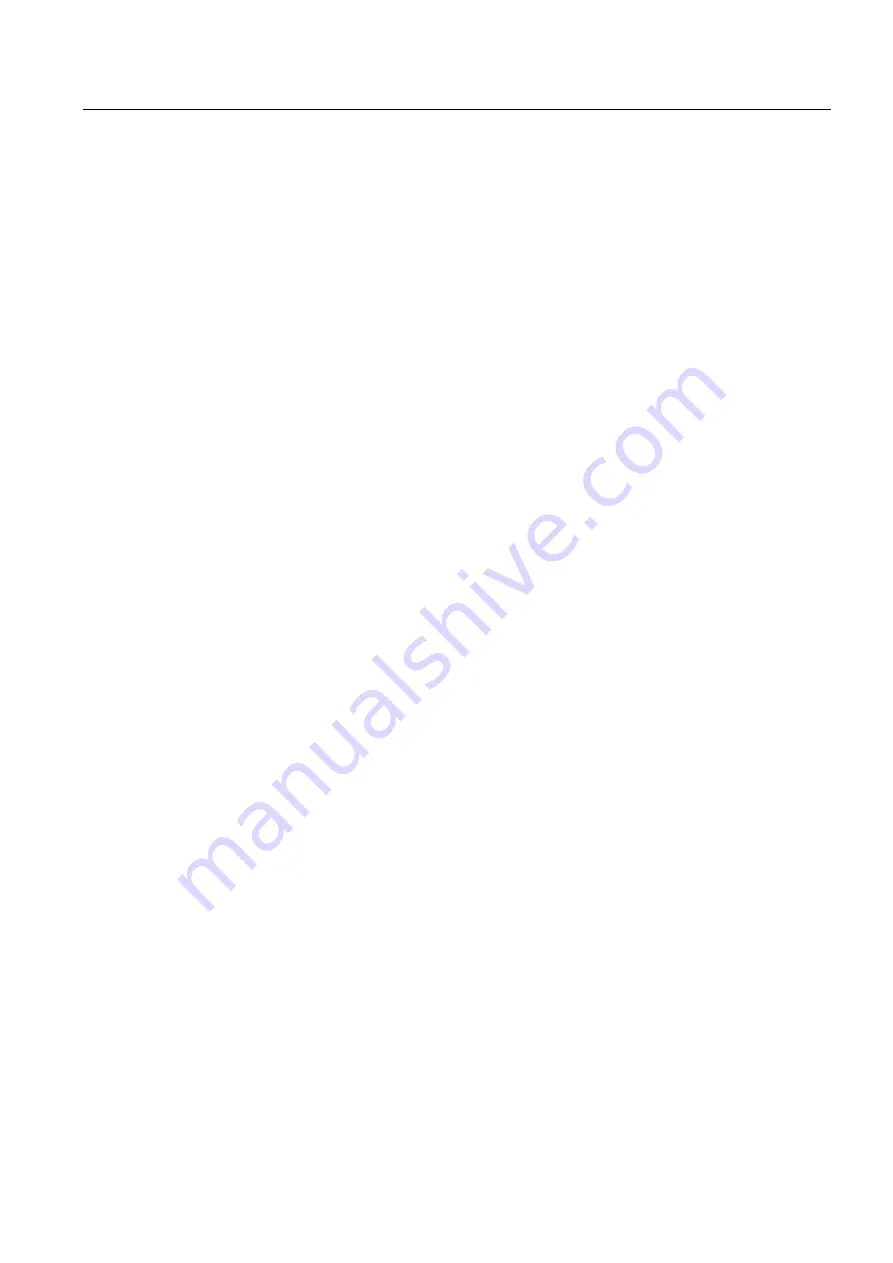
Functions
5.11 Operation in fieldbus systems
Frequency inverter
Operating Instructions, 08.10. 2008, t.b.d.
149
5.11
Operation in fieldbus systems
The frequency inverters are available in different variants for communication with higher-
level controls with the subsequently listed fieldbus interfaces:
●
CU240E and CU240S for USS via RS485
–
Control via PZD (process data channel)
–
Parameterizing using PKW (parameter channel)
●
CU240S DP and CU240S DP-F for PROFIBUS DP
–
Control in cyclic operation using telegrams 1, 20, 350, 352 and 999
–
Control and parameterizing in cyclic operation using telegrams 353 and 354
–
Parameterizing using acyclic communication
●
CU240S DP and CU240S DP-F for PROFINET
–
Control in cyclic operation using telegrams 1, 20, 350, 352 and 999
–
Control and parameterizing in cyclic operation using telegrams 353 and 354
–
Parameterizing via acyclic communication
5.11.1
Communication via USS
Universal serial interface (USS)
The USS protocol allows you to establish a serial point-to-point connection (RS 232
interface) and serial data connection between a higher-level master system and several
slave systems (RS 485 interface). Master systems include programmable logic controllers
(e.g. SIMATIC S7-200) or PCs. The converters are always slaves on the bus system.
The USS protocol allows you to implement automation tasks with cyclic message frame
transfer (fixed message frame length required) and visualization tasks. In this case, variable
message frame lengths are better since texts and parameter descriptions can be transferred
in a single message frame without the data being split up.
USS bus topology via RS 485
Communication networks with up to 31 frequency inverters (slaves) connected to a control
can be established via the RS 485 interface. The topology must be configured as a path in
which the first and last devices are terminated with terminating resistors.