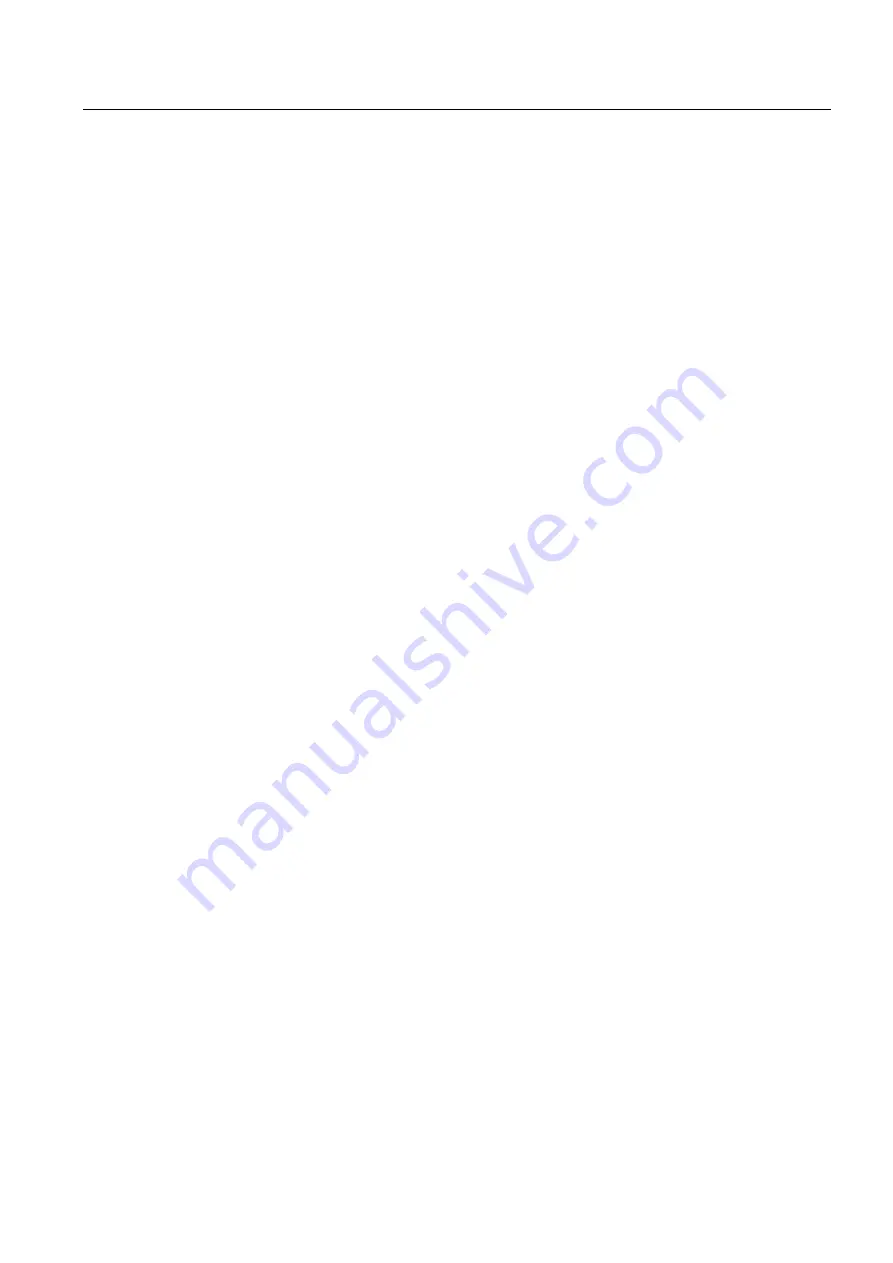
Glossary
Fail-safe signal modules
Installation and Operating Manual, 01/2010, A5E00085586-10
333
Discrepancy analysis
Discrepancy analysis for equivalence or nonequivalence is used for fail-safe inputs in order
to determine faults based on the time characteristic of two signals with the same
functionality. Discrepancy analysis is initiated when different levels are detected for two
associated input signals (for nonequivalence check: same level). On expiration of an
assignable period (→ discrepancy time), a check is made to determine whether the difference
(or, in the case of nonequivalence: the agreement) has been cleared. If not, a discrepancy
error exists.
There are two types of discrepancy analysis for fail-safe input modules:
●
→ 1oo2 evaluation:
The discrepancy analysis is performed between the two input signals of the 1oo2
evaluation in the fail-safe input module.
●
With redundant I/O (only S7 FH systems):
The discrepancy analysis is performed between the two input signals of the redundant
input modules by the fail-safe driver blocks of the
S7 F/FH Systems optional software.
Discrepancy time
Assignable time for the → discrepancy analysis. If the assigned discrepancy time is too long,
the fault detection time and → fault reaction time are prolonged unnecessarily. If the assigned
discrepancy time is too short, availability is reduced unnecessarily, as a discrepancy error
which in actual fact does not exist is reported.
F monitoring time
→ PROFIsafe monitoring time
Fail-safe signal modules
S7-300 signal modules that support safety-oriented operation (in → safety mode) in
S7
Distributed Safety or S7 F/FH Systems. These modules feature integrated → safety
functions.
Fail-safe systems
Fail-safe systems (F-systems) remain in a safe state or immediately change to another safe
state when specific failures are detected.
Fault reaction time
The maximum fault reaction time of an F-system denotes the interval between the
occurrence of any fault and a reliable reaction at all corresponding fail-safe outputs. For the
overall → F-System: The maximum fault reaction time defines the interval between the
occurrence of any fault in any → F-I/O and a reliable reaction at the corresponding fail-safe
output.
At inputs: The maximum fault reaction time defines the interval between the occurrence of
the fault and the reliable reaction at the backplane bus.
For digital outputs: The maximum fault reaction time defines the interval between the
occurrence of the fault and the reliable reaction at the digital output.