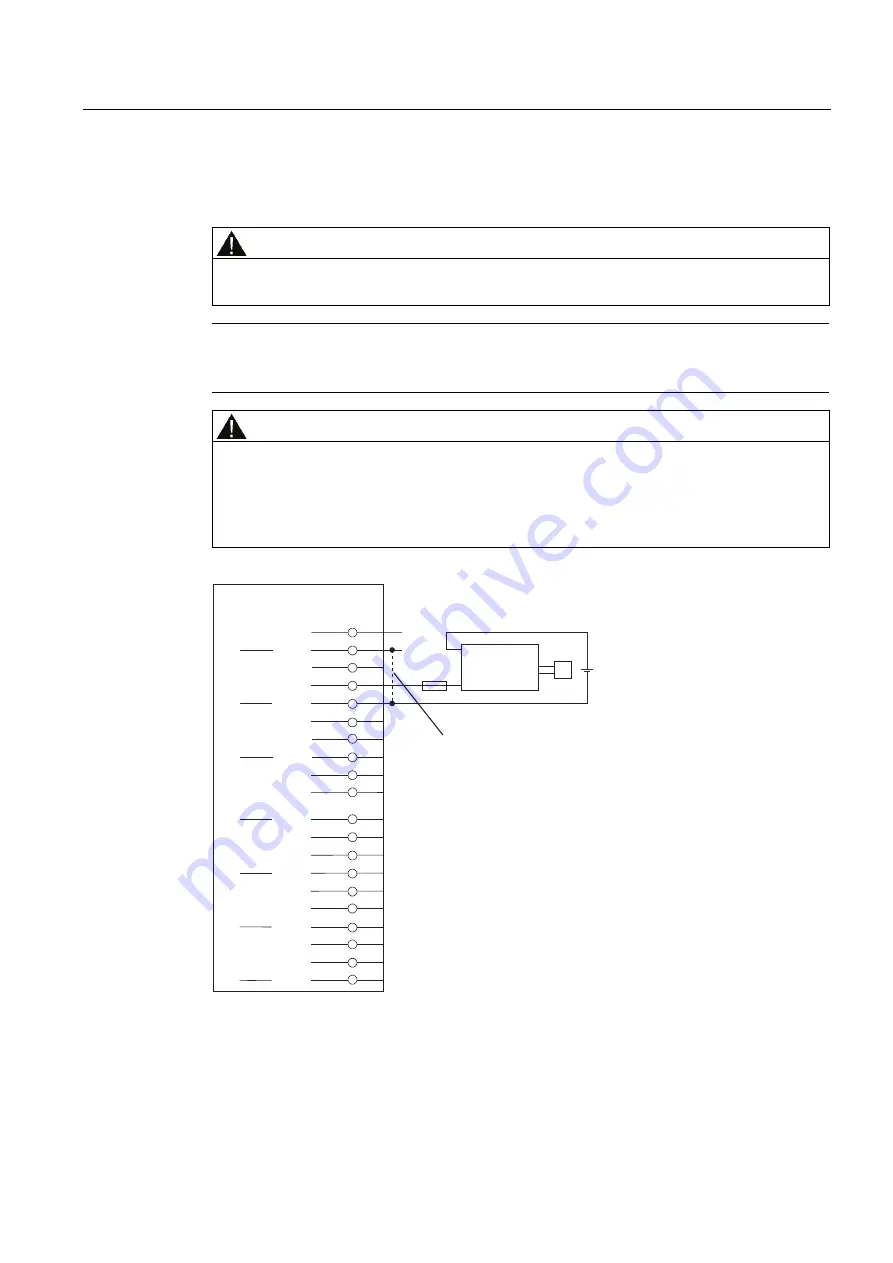
Analog modules
9.3 SM 336; F-AI 6 x 0/4 ... 20 mA HART
Fail-safe signal modules
232
Installation and Operating Manual, 01/2010, A5E00085586-10
Wiring scheme B: 2-wire transducer, external sensor supply
Particularity:
WARNING
An undervoltage at the transducer cannot be detected, i.e., a transducer with undervoltage
detection may be required.
Note
1L+ and 2L+ can be fed from one power supply. The maximum permissible common mode
voltage U
CM
must be observed.
WARNING
Depending on the internal structure of the sensor, a short circuit from 2L+ to Mn+ (sensor
with measuring circuit referring to 2M) or from Mn- to 2M (sensor with measuring circuit
referring to 2L+) can destroy the input resistors (see documentation for the utilized sensor).
For this reason, a suitable measure must be taken to protect the input resistors (e.g. fuse
on the module).
60
$,[P$+$57
/
0
/
0
/
0
9V
0
0
9V
0
0
9V
0
0
9V
0
0
9V
0
0
9V
0
0
3
&+
&+
&+
&+
&+
&+
ZLUH
WUDQVGXFHU
UHFRPPHQGHG
Figure 9-23 2-wire transducer, external sensor supply