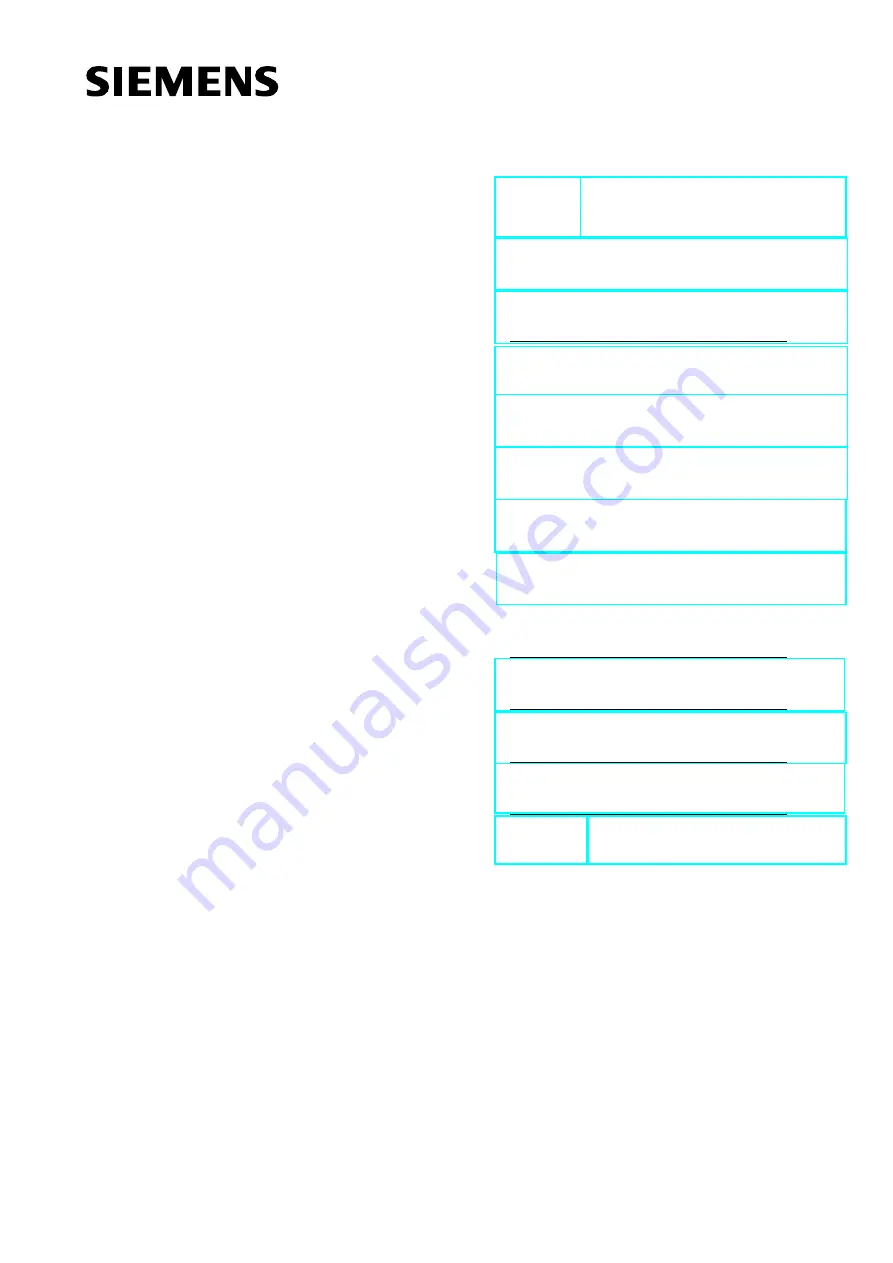
General Technical Specifications
Appendices
Dimensioned Drawings and
Pinouts
Edition 02/2003
EWA 4NEB 780601602-06
ET 200X Distributed I/O Device
Manual
SIMATIC
This manual is part of the documentation
package with the order number
6ES7198-8FA10-8BA0
Summary of Contents for SIMATIC ET 200X
Page 8: ...Preface viii ET 200X Distributed I O Device EWA 4NEB 780601602 06 ...
Page 20: ...Contents xx ET 200X Distributed I O Device EWA 4NEB 780601602 06 ...
Page 40: ...Product Overview 1 20 ET 200X Distributed I O Device EWA 4NEB 780601602 06 ...
Page 58: ...Configuration Options 2 18 ET 200X Distributed I O Device EWA 4NEB 780601602 06 ...
Page 80: ...Installation 3 22 ET 200X Distributed I O Device EWA 4NEB 780601602 06 ...
Page 124: ...Configuration Options 2 18 ET 200X Distributed I O Device EWA 4NEB 780601602 06 ...
Page 328: ...Order Numbers A 10 ET 200X Distributed I O Device EWA 4NEB 780601602 06 ...
Page 348: ...Dimesioned Drawings and Pinouts C 18 ET 200X Distributed I O Device EWA 4NEB 780601602 06 ...
Page 362: ...Index Index 8 ET 200X Distributed I O Device EWA 4NEB 780601602 06 ...