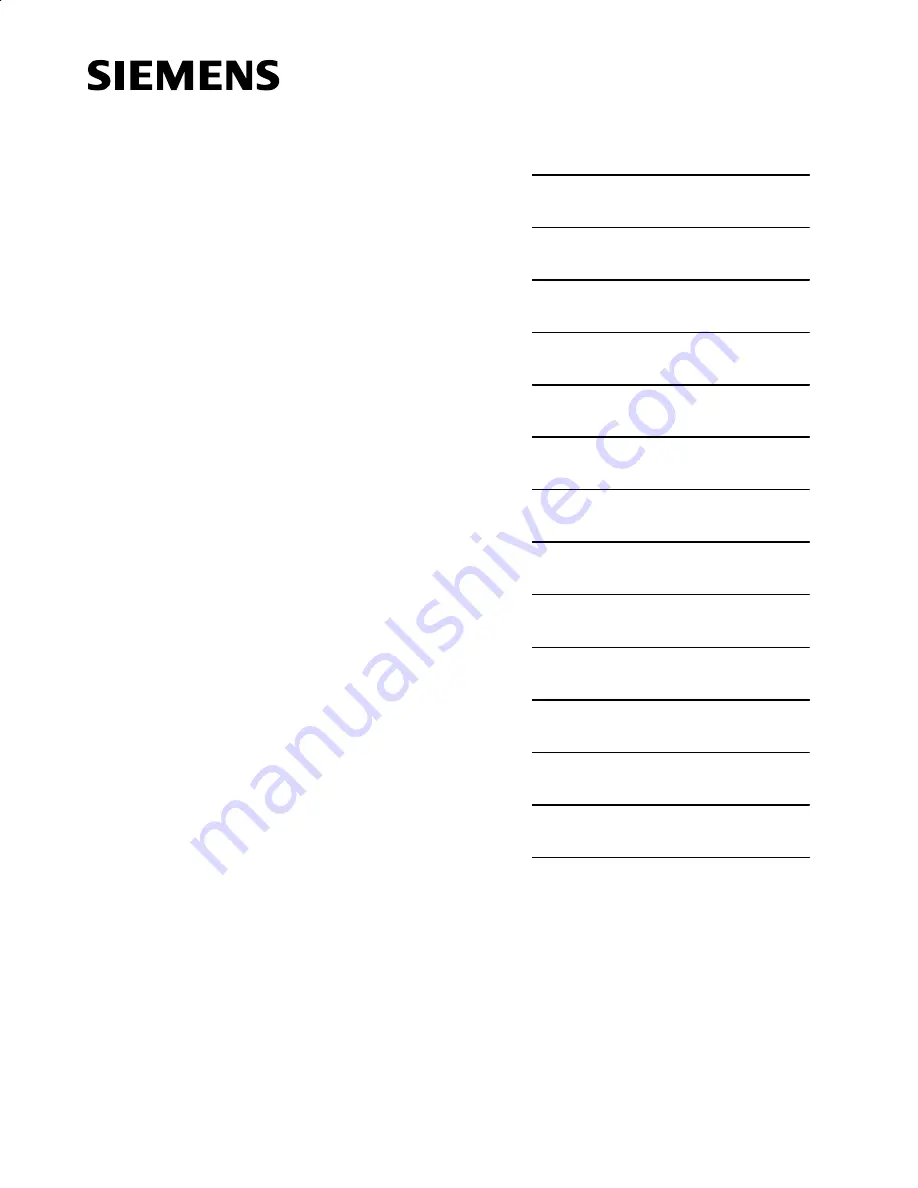
Preface, Contents
Overview
1
ASi Basics
2
Configuration Options
3
Installing and Wiring DP/ASi Link
4
Configuring the DP/ASi Link
5
DP/ASi Link to S7
6
Operating Modes
7
Diagnostics and Error Handling
8
Appendices
Technical Data
A
I/O Code
B
Parameterization Message
C
Configuration Message
D
Glossary, Index
Edition 3
EWA 4NEB 710 6055-02b
Distributed I/O System
DP/ASi Link
Manual
SIMATIC
Summary of Contents for SIMATIC Distributed I/O System DP/ASi Link
Page 6: ...vi Distributed I O System DP ASi Link EWA 4NEB 710 6055 02b Preface ...
Page 18: ...1 6 Distributed I O System DP ASi Link EWA 4NEB 710 6055 02b Overview ...
Page 26: ...2 8 Distributed I O System DP ASi Link EWA 4NEB 710 6055 02b ASi Basics ...
Page 72: ...5 12 Distributed I O System DP ASi Link EWA 4NEB 710 6055 02b Configuring the DP ASi Link ...
Page 116: ...B 2 Distributed I O System DP ASi Link EWA 4NEB 710 6055 02b I O Code ...
Page 128: ...C 12 Distributed I O System DP ASi Link EWA 4NEB 710 6055 02b Parameterization Message ...
Page 148: ...Index 6 Distributed I O System DP ASi Link EWA 4NEB 710 6055 02b Index ...