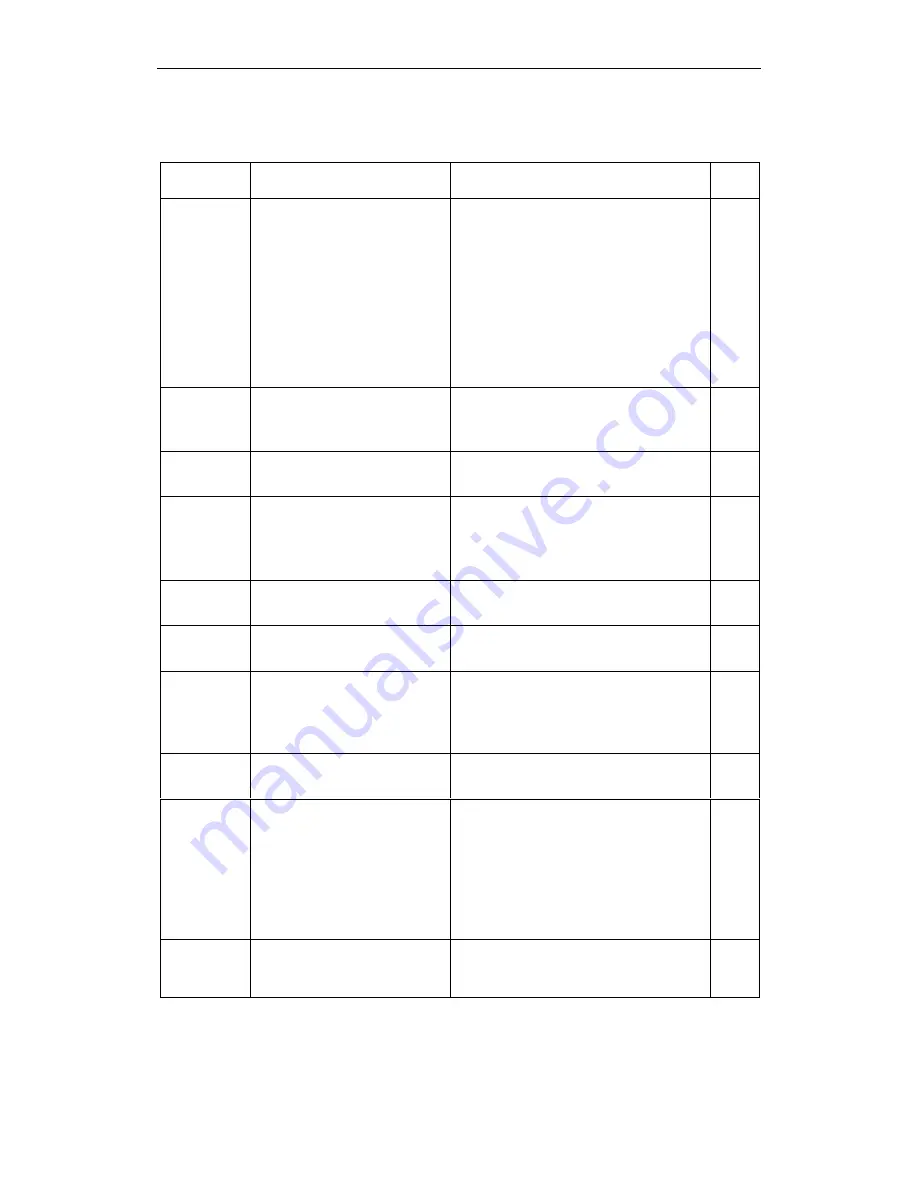
6 Troubleshooting
Issue 04/02
MICROMASTER 410 Operating Instructions
60
6SE6400-5EA00-0BP0
6.4 Alarms
Alarm
Possible Causes
Diagnose & Remedy
Reac-
tion
A0501
Current Limit
Ø
Motor power does not
correspond to the inverter power
Ø
Motor leads are too long
Ø
Earth
faults
Check the following:
1.
Motor power (P0307) must correspond to
inverter power (r0206).
2. Cable length limits must not be exceeded.
3. Motor cable and motor must have no short-
circuits or earth faults
4.
Motor parameters must match the motor in
use
5. Motor must not be obstructed or overloaded
Ø
Increase
the
ramp-up-time.
Ø
Reduce the boost.
--
A0502
Overvoltage
limit
Ø
Overvoltage limit is reached.
Ø
This warning can occur during
ramp down, if the dc-link con-
troller is disabled (P1240 = 0).
If this warning is displayed permanently, check
drive input voltage .
--
A0503
UnderVoltage
Limit
Main supply failed
Check main supply voltage (P0210).
--
A0504
Inverter Over
Temperature
Warning level of inverter heat-sink
temperature (P0614) is exceeded,
resulting in pulse frequency reduction
and/or output frequency reduction
(depending on parametrization in
(P0610)
Check the following:
1. Ambient temperature must lie within
specified limits
2. Load conditions and duty cycle must be
appropriate
--
A0505
Inverter I
2
t
Warning level exceeded, current will
be reduced if parameterized
(P0610 = 1)
Check that duty cycle lies within specified limits
--
A0506
Inverter duty
cycle
Difference between heatsink and
IGBT junction temperature exceeds
warning limits
Check that duty cycle and shock loads lie within
specified limits
--
A0511
Motor Over
Temperature
I
2
t
Ø
Motor
overloaded.
Ø
Load duty cycle too high.
Check the following:
1. P0611
(motor
I
2
t time constant) should be
set to appropriate value
2. P0614
(Motor
I
2
t overload warning level)
should be set to suitable level
--
A0600
RTOS Overrun
Warning
Software problem
Contact Service Department
--
A0910
Vdc-max
controller de-
activated
Ø
Vdc max controller has been de-
activated
Ø
Occurs if main supply voltage is
permanently too high.
Ø
Occurs if motor is driven by an
active load, causing motor to go
into regenerative mode.
Ø
Occurs at very high load inertias,
when ramping down.
Check the following:
1. Input voltage must lie within range.
2.
Load must be matched.
3. In certain cases apply braking resistor.
--
A0911
Vdc-max
controller
active
Vdc max controller is active; so ramp-
down times will be increased
automatically to keep DC-link voltage
(r0026) within limits
Check the inverter input voltage (P0210)
--
Summary of Contents for micromaster 410
Page 1: ......
Page 5: ......
Page 10: ...Safety Instructions Issue 04 02 MICROMASTER 410 Operating Instructions 10 6SE6400 5EA00 0BP0 ...
Page 14: ...Table of Contents Issue 04 02 MICROMASTER 410 Operating Instructions 14 6SE6400 5EA00 0BP0 ...
Page 44: ...3 Commissioning Issue 04 02 MICROMASTER 410 Operating Instructions 44 6SE6400 5EA00 0BP0 ...
Page 56: ...5 System Parameters Issue 04 02 MICROMASTER 410 Operating Instructions 56 6SE6400 5EA00 0BP0 ...
Page 62: ...6 Troubleshooting Issue 04 02 MICROMASTER 410 Operating Instructions 62 6SE6400 5EA00 0BP0 ...
Page 68: ...8 Options Issue 04 02 MICROMASTER 410 Operating Instructions 68 6SE6400 5EA00 0BP0 ...
Page 74: ......
Page 80: ...Index Issue 04 02 MICROMASTER 410 Operating Instructions 80 6SE6400 5EA00 0BP0 ...
Page 82: ...MICROMASTER 410 Operating Instructions 82 6SE6400 5EA00 0BP0 ...
Page 84: ......