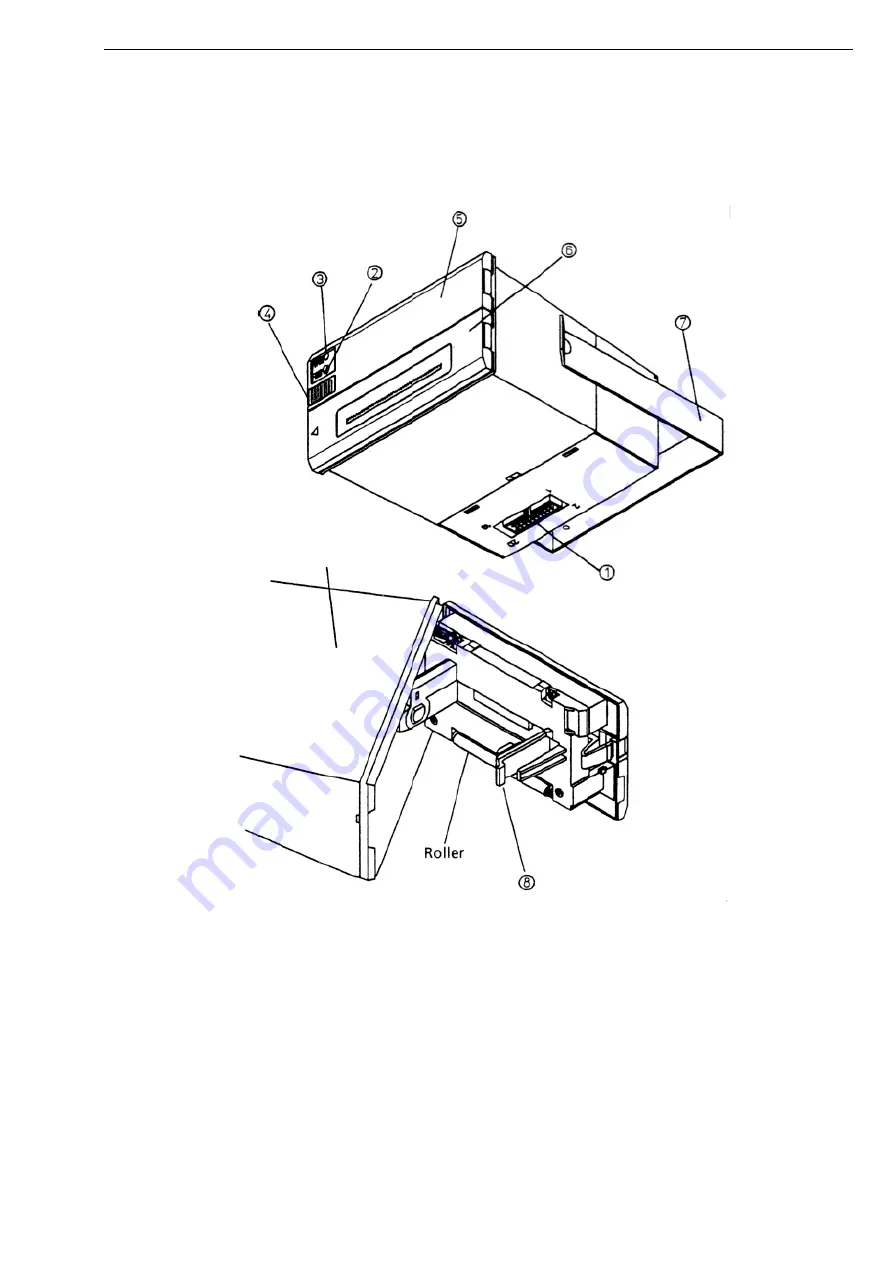
"Steam sterilizer Laboklav 55 - 195"
User manual
49
10.6. Changing paper and ribbon cassette of the printer
The CBM-920 CITIZEN printer is a dot-matrix printer. It is available as an optionally integrated device
which is connected to the device via a serial interface RS 232.
For more information, please read the detailed operating instructions of the printer from the
manufacturer.
Figure 4: Printer CBM 920 RS 232
1- Interface Connector
2- Feed Switch
3- Paper Lamp
4- Knob
5- Front Cover
6- Ribbon Cover
7- Mounting bracket
8- Paper Holder
Case