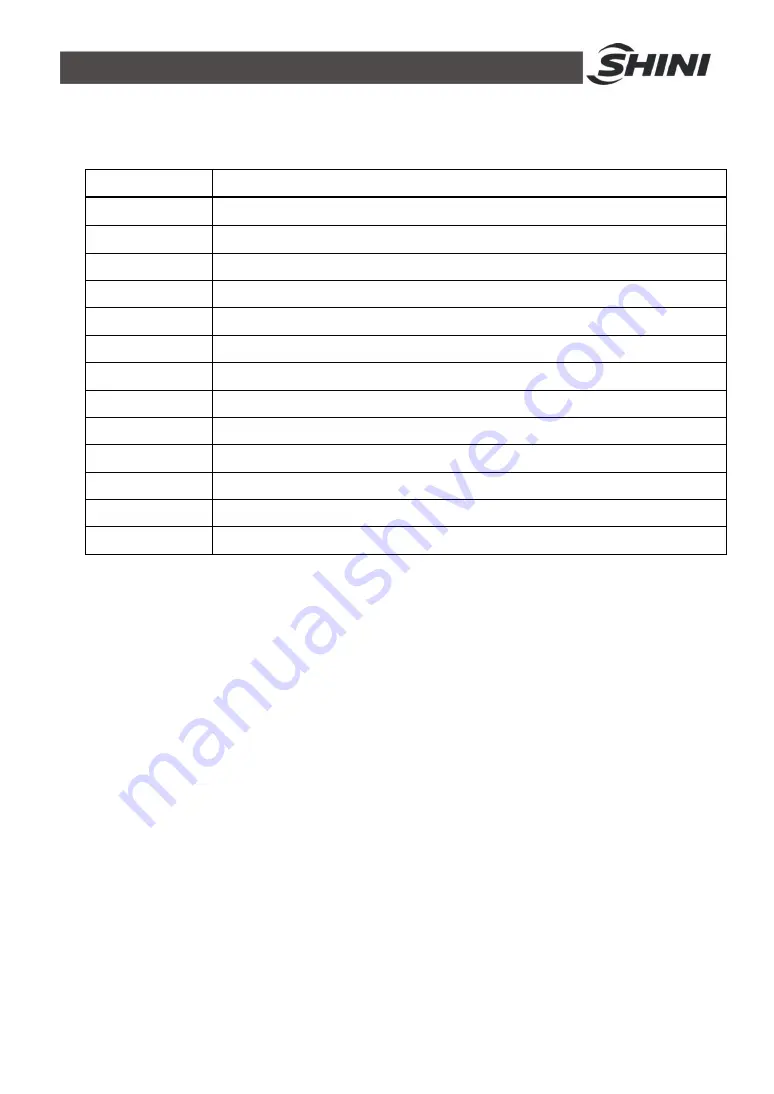
33(62)
4.13 Alarm Description (Dehumidifying System)
Table 4-1: Error Code
Error Code
Description
E-01
Heater thermocouple
E-02
Anti- phase, default phase
E-03
Blower overload
E-04
Drying temp. is higher than EGO protection set value
E-05
Drying temp. is higher than system set max. temp.
E-07
Over-temp protection (PV
≥
SV+ set value, system sounds alarm)
E-08
Memory error
E-09
Honeycomb rotor fault
E-10
Regenerative temp. is higher than EGO protection set value.
E-11
Thermocouple of
“
+,-
”
connect wrongly.
E-12
PID auto-turning fault
E-13
Low temp. alarm
E-12
Heater Alarm
Summary of Contents for SCD-160Ux2/200H
Page 1: ...SCD One to Two Compact Dryer Date Aug 2018 Version Ver A English ...
Page 2: ......
Page 8: ...8 62 ...
Page 41: ...41 62 ...