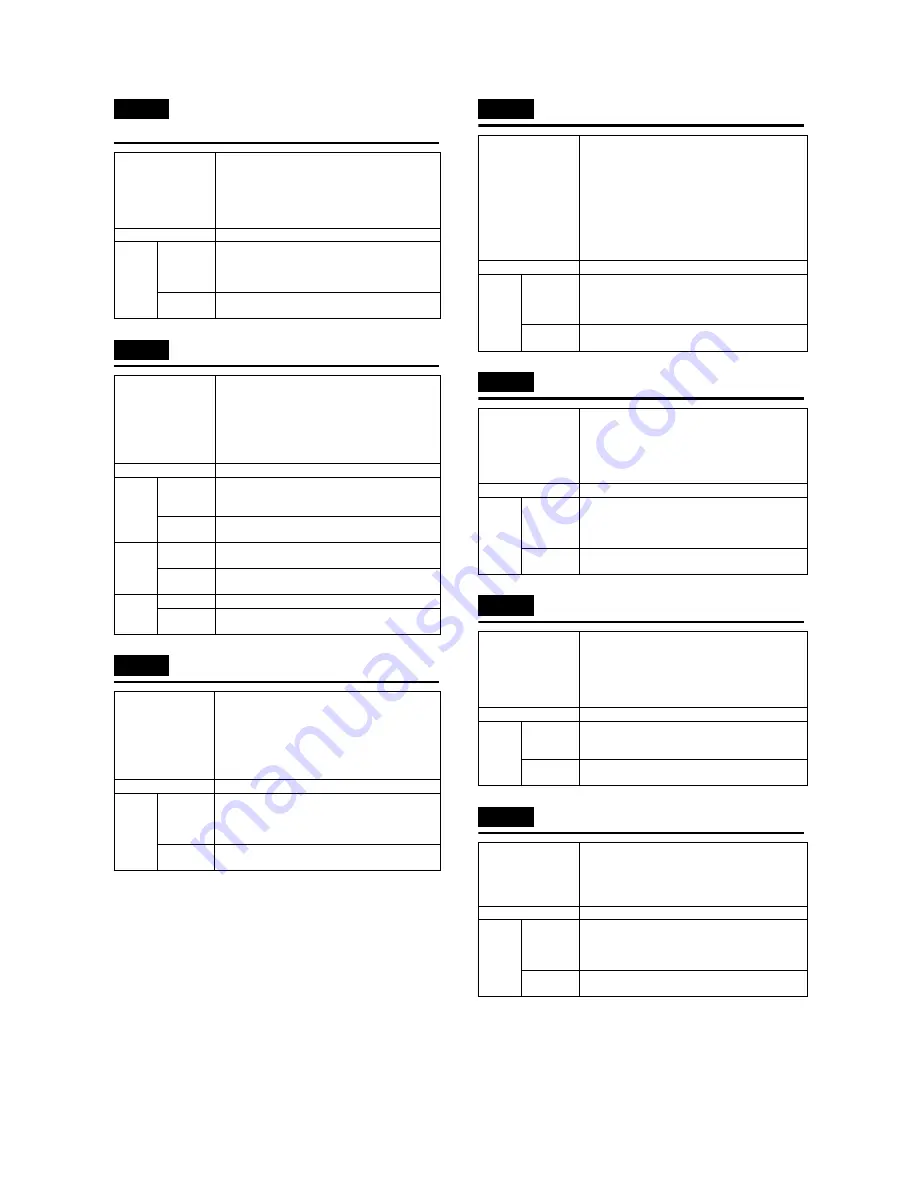
MX-M700N SELF DIAG AND TROUBLE CODE 8 – 10
EE-EU
Auto developer adjustment trouble
(Undertoner error)
F1-00
Finisher communication trouble
F1-02
Finisher transport motor abnormality
F1-03
Finisher oscillation motor trouble
F1-08
Finisher staple shift motor trouble
F1-09
Finisher load capacity sensor trouble
F1-10
Finisher/staple motor trouble
Details
Described on the toner density control design
specifications and the change request.
When the average of 10 output values of the toner
sensor (sampling data) after completion (3 min) of
the auto development adjustment is smaller than
3.5V.
Section
Engine
Case 1
Cause
Toner density sensor trouble
Charging voltage and developing voltage trouble
Toner density trouble
Developing unit trouble PCU PWB trouble
Check and
remedy
Use SIM 25-2 to perform the automatic developing
adjustment.
Details
An error in the communication line test after
turning on the power or canceling the simulation.
Communication error with the finisher.
Follows the communication protocol specifications.
Communication error, timing abnormality of the
communication data and the communication signal
line
Section
Engine
Case 1
Cause
Improper connection or disconnection of the
connector or harness between the machine and
the finisher.
Check and
remedy
Check the connector and the harness in the
communication line.
Case 2
Cause
Finisher control PWB trouble.
Control PWB (PCU) trouble.
Check and
remedy
Replace the finisher control PWB or the PCU
PWB.
Case 3
Cause
Malfunction caused by noises
Check and
remedy
Canceled by turning ON/ OFF the power.
Details
When opening the shutter unit, the opening
process is not completed in 1sec.
When closing the shutter unit, the closing process
is not completed in 1sec.
When the tray lift unit is operating in the dangerous
area, "Not closed state" of the shutter close sensor
is detected.
Section
Finisher
Case 1
Cause
Motor lock
Motor RPM abnormality
Overcurrent to the motor
Finisher control PWB trouble
Check and
remedy
Use SIM 3-3 to check the transport motor
operation.
Details
When opening the oscillation unit, the opening
process is not completed in 1sec.
When closing the oscillation unit, the closing
operation is not completed in 3sec.
When the tray lift unit is operating in the dangerous
area, "Not closed state" of the oscillation unit close
sensor is detected.
When controlling the oscillation unit speed, the
encoder input cannot be detected within a specified
time.
Section
Finisher
Case 1
Cause
Motor lock
Motor RPM abnormality
Overcurrent to the motor
Finisher control PWB trouble
Check and
remedy
Use SIM 3-3 to check the motor operation.
Details
When the stapler shift motor does not move from
the hope position in 4sec when operating the
stapler shift motor.
When the stapler shift motor does not return to the
home position in 4sec when operating the stapler
shift motor.
Section
Finisher
Case 1
Cause
Motor lock
Motor RPM abnormality
Overcurrent to the motor
Finisher control PWB trouble operation.
Check and
remedy
Use SIM 3-3 to check the staple shift motor
Details
When the received data on performing the sensor
test at turning on the power are outside the
specified range.
When the detected data on calculation of the
correction value are outside the specified
range.
Section
Finisher
Case 1
Cause
Sensor breakage
Harness disconnection
Console finisher control PWB trouble
Check and
remedy
Use SIM 3-2 to check the sensor operation.
Details
When the staple unit does not shift from HP within
0.5sec in staple process.
When a stapler jam is detected and the staple
motor is reversed, the staple motor does not return
to HP in 0.5sec.
Section
Finisher
Case 1
Cause
Motor lock
Motor RPM abnormality
Overcurrent to the motor
Finisher control PWB trouble
Check and
remedy
Use SIM 3-3 to check the staple shift motor
operation.