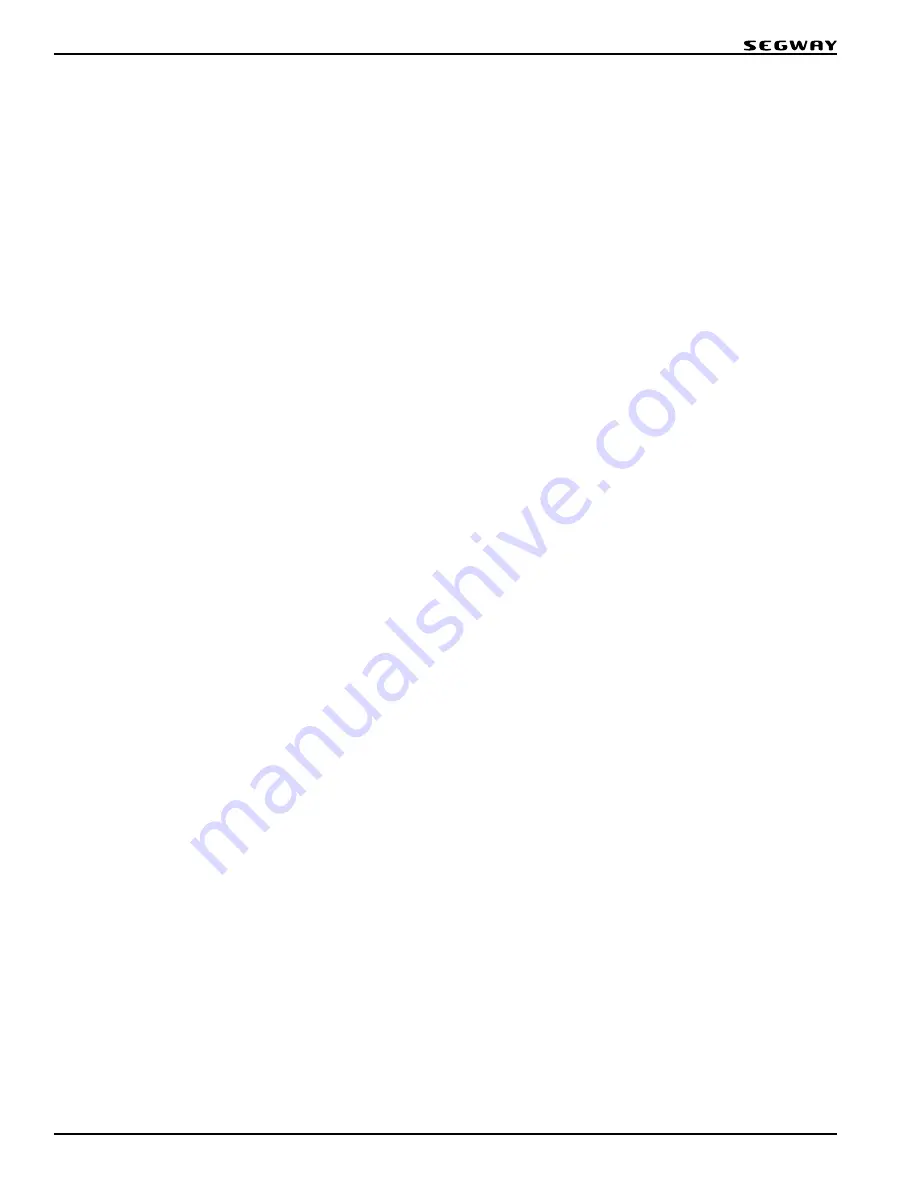
24
Operational Model
RMP 210
Initialization
Initialization is composed of three sub-states: Init Hardware, Init Propulsion, and Check Startup Issues. First, the control hardware is
initialized; this includes the CCU and ABB. Then, the propulsion system is initialized (the MCUs and BSA). If there are no issues with
the system, the RMP transitions to Standby Mode. Otherwise it shuts down.
If the BOOT1 or BOOT2 signal is pulled low the RMP will enter Diagnostic Mode or Bootloader Mode, respectively.
Init Hardware
During Init Hardware, the following steps are performed:
1. UIP and SP initialize hardware, interrupts, and software.
2. UIP and SP synchronize their timing.
3. UIP-SP communication is established.
4. SP reads configuration parameters from NVM, initializes dependent data, and passes the parameters to the UIP for UIP
dependent data initialization.
5. UIP and SP verify configuration validity.
6. SP extracts the faultlog from NVM and relays the faultlog array to the UIP for user access.
Init Propulsion
During Init Propulsion the SP initializes each MCU using a state machine. Each state verifies a certain MCU operational status. If any
MCU is not operating as expected, the RMP will transition to Disable Mode and power off. Information regarding the failure is stored
in the faultlog.
Check Startup Issues
In this sub-state the SP checks for various parameters that will gate entry to Standby Mode. When the RMP detects an issue, Standby
Mode entry is gated and the RMP will emit a tone and blink the LEDs for five seconds before failing initialization. If the issue is
corrected in this time, the transition to Standby Mode will be allowed.
The following issues will gate transition to Standby Mode:
• An MCU declares a fault.
• The RMP is charging (this can be overridden: refer to the
RMP V3 Interface Guide).
• An MCU battery open circuit voltage is below the operational threshold.
• An MCU battery state of charge is below the operational threshold.
• 7.2 VDC battery (if present) has low or high voltage.
• Any detected machine motion (RMP moving un-commanded).
• Tractor mode request is present from the user.
• BSA communication has not been established.
Faults
Faults occur in response to events that impact the RMP. This could include anything from receiving a user-commanded DTZ signal
to detecting a failed battery. Sometimes faults are the result of a problem that needs to be resolved. Other times they are merely
informative.
In response to a fault the RMP may simply log the fault or it may take an action. There are four types of fault responses:
• No fault response — fault is logged. No change in RMP behavior.
• DTZ response — fault initiates a Decel To Zero. RMP comes to a stop, logs the fault, and holds position. Disable response —
fault causes RMP to power off. RMP logs the fault and powers off immediately.
• Disable MCU response — fault causes a single MCU to go down. RMP will continue to hold position as in a DTZ response.
Summary of Contents for RMP 210 V3
Page 1: ...User Manual Segway Robotics Mobility Platform RMP 210 V3 Robotics...
Page 2: ......
Page 20: ...20 RMP 210 RMP 210...
Page 30: ...30 Powering On Off RMP 210...
Page 34: ...34 Connecting RMP 210...
Page 40: ...40 Maintenance RMP 210...
Page 49: ...49 User Manual Troubleshooting...
Page 50: ...Robotics 24927 00001 aa...