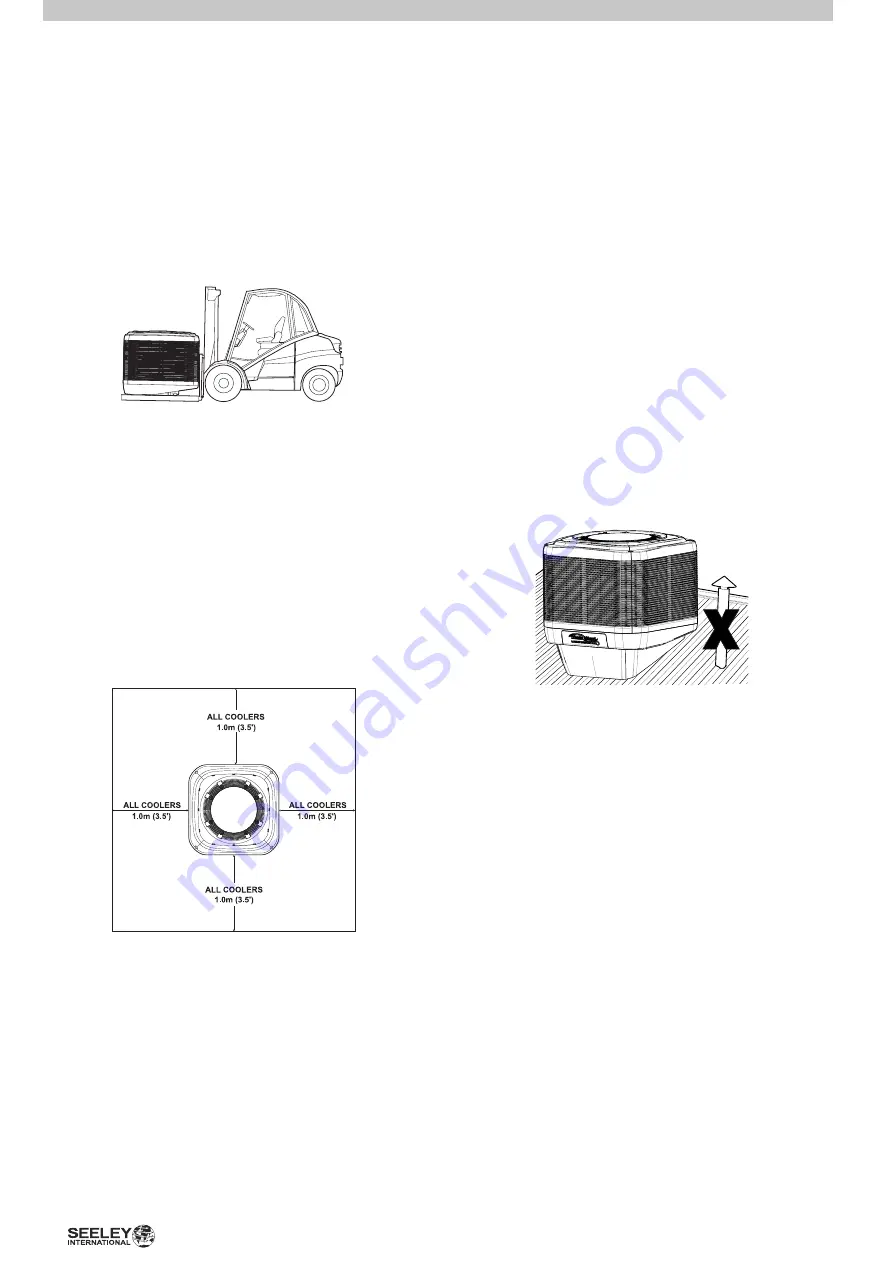
8 |
INSTALLATION
MOVING THE COOLER
The CW-6S cooler can be moved either by fork-truck or pallet-
truck whilst it is resting on its dedicated pallet. Do not drag or lift
the cooler unless it is on its dedicated pallet.
If the cooler has been unpackaged as per the instructions in the
‘On Arrival to Site’ section, then ensure that the foam supporting
blocks are in place and transport carefully.
COOLER LOCATION
Check proposed cooler location to ensure it is structurally
capable of supporting the weight of the cooler. If the roof is
structurally inadequate, provide an alternate load bearing
structure.
The ideal location for the cooler is in a central position on the
roof (away from sleeping areas and where people spend most
of their time) so that the duct runs are of approximately the
same length. Carefully consider neighbouring residences and
noise levels when locating the cooler, if necessary talk to the
customer and the neighbour before carrying out the installation.
Always locate the cooler where it will receive adequate fresh air
and not in a recess where it may be starved for air or where the
air is polluted.
Ensure location is a minimum of:
•
3m (10’) from a solid fuel heater flue,
•
1.5m (5’) from a gas flue,
• 1.0m (3.5’) away from adjacent solar panels or similar roof
mounted fixtures,
• 5m (17’) from a sewer vent, and
• 600mm (2’) from a wall.
ILL2970-A
ILL2962-A
Allow adequate access to and around the cooler for
maintenance. Provision must be made for access to electricity,
water supplies and drains.
Note!
Do you need to discuss the installation of items like
safety anchor points with the customer?
• The cooler must be mounted at least 3m (10’) (preferably
5m (17’)) away from any TV antenna or antenna cables.
Make sure the cooler is not between the antenna and the
transmission tower that is providing the television signal to the
home.
ACCESS FOR SERVICING AND MAINTENANCE
The cooler should be installed in a position that allows adequate
access for installation, and future maintenance and servicing
activities. This should comply with installation guidelines and
any local, State and National regulations.
Consider the following for installation location:-
• Which has clear access to and around the cooler
•
Which is clear of fixtures in line with below clearances
• Which is clear of fall edges (> 3m away)
• Which is structurally capable of supporting the weight of the
cooler and service technicians
Required clearances around the cooler for future maintenance
and servicing are shown adjacent.
Extra service or warranty charges may apply for the cost of
any equipment or additional labour involved in accessing
the cooler if these guidelines are not met.
ILL2987-A