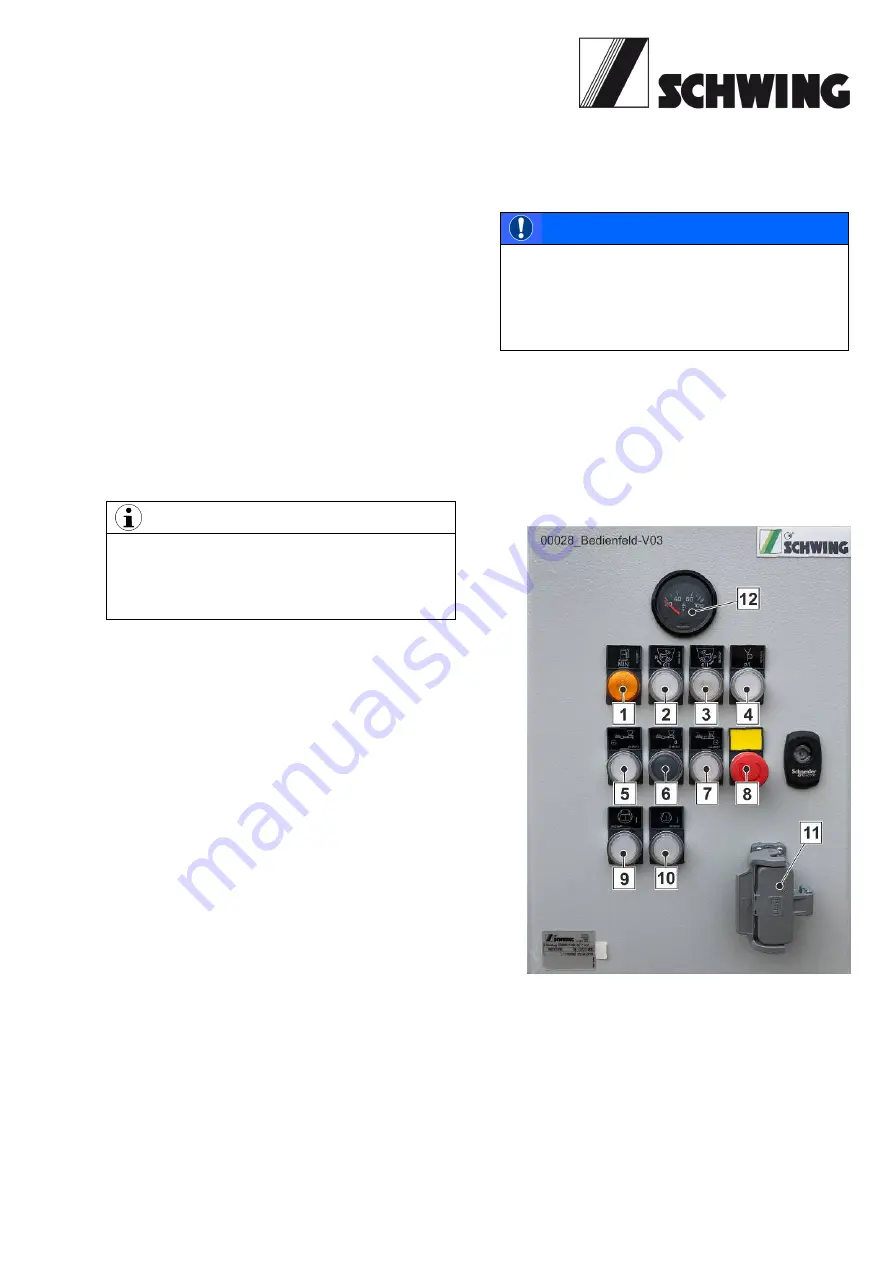
3.39-1
005.149.04-EN
3.39 Troubleshooting/emergency operation
3.39.1 Control failure
If a functional failure occurs, first check whether
- An EMERGENCY STOP button has been
actuated.
- The grid assembly in the filling hopper is
raised.
- A fuse has been triggered.
- * The magnets of the competent control
valves are supplied with voltage.
* INFORMATION
The plugs of the control valve magnets are
equipped with light-emitting diodes for
troubleshooting, which must light up when
voltage is present.
3.39.2 Electrical fuse protection for the
machine control system
Depending on the type of machine, the system
can be secured in several places:
-
A main safety fuse located near the starter.
-
Safety fuses in the switch cabinet or
operator station of the concrete pump
(Fig. 1).
Also see electric circuit diagram.
Check fuses:
-
Switch off the motor and remove the
ignition key.
-
Open the top cover of the control station
using the special key.
Commercially available vehicle fuses are used.
Only insert newly equivalent fuses.
ATTENTION
Material damage caused by overrated
fuses!
The electrical system is destroyed due to
overrated and overridden fuses
-
Close the cover of the control station and
begin operating the machine.
If the error occurs again:
-
Stop the machine and
-
have an electrician inspect the system.
Fig. 1
Summary of Contents for SP 1800-D
Page 1: ...Original operating instructions Stationary concrete pump EN SP 1800 D SP 2800 D...
Page 8: ...005 007 00 EN Blank page...
Page 26: ...1 4 6 004 997 02 EN Blank page...
Page 30: ...1 4 1 4 002 410 15 EN Blank page...
Page 46: ...1 7 10 005 142 08 EN Fig 21 turn main switch for starter batteries to the right...
Page 48: ...005 016 00 EN Blank page...
Page 49: ...Safety Manual Concrete delivery and placing machines 01 2018 Rev16 EN...
Page 56: ...8 01 2018 Rev16 EN...
Page 58: ...10 01 2018 Rev16 EN...
Page 78: ...30 01 2018 Rev16 EN...
Page 104: ...56 01 2018 Rev16 EN...
Page 106: ...58 01 2018 Rev16 EN...
Page 120: ...72 01 2018 Rev16 EN...
Page 121: ......
Page 122: ......
Page 124: ...005 017 00 EN Blank page...
Page 126: ...3 2 1 001 855 06 EN Blank page...
Page 129: ...3 3 3 001 462 06 EN Fig 1...
Page 130: ...3 3 4 001 462 06 EN Blank page...
Page 139: ...3 10 5 005 144 04 EN Fig 10 Fig 11 locked release Fig 12 Fig 13...
Page 150: ...3 20 6 004 551 01 EN Blank page...
Page 164: ...3 22 14 003 336 15 EN Blank page...
Page 174: ...3 34 4 004 546 02 EN Blank page...
Page 180: ...3 37 4 004 910 01 EN Blank page...
Page 186: ...3 38 6 005 148 02 EN Blank page...
Page 220: ...3 60 12 002 368 08 EN Blank page...
Page 224: ...3 80 2 001 156 04 EN Blank page...
Page 226: ...005 018 00 EN Blank page...
Page 232: ...4 3 2 002 878 14 EN Blank page...
Page 244: ...4 4 12 000 869 22 EN Blank page...
Page 264: ...4 5 20 000 024 14 EN Blank page...
Page 268: ...4 10 2 004 073 01 EN Blank page...
Page 274: ...4 11 001 915 00 EN Blank page...
Page 276: ...4 11 001 915 00 EN Blank page...
Page 284: ...4 20 8 004 553 03 EN Blank page...
Page 292: ...4 30 4 004 491 01 EN Blank page...
Page 300: ...4 40 8 001 193 16 EN Blank page...
Page 306: ...4 42 6 004 076 01 EN Blank page...
Page 324: ...4 44 18 002 514 16 EN Blank page...
Page 330: ...4 55 6 002 940 02 EN Blank page...
Page 332: ...4 57 2 004 054 00 EN Blank page...
Page 340: ...4 60 8 005 151 04 EN Blank page...
Page 346: ...4 70 2 001 918 05 EN Blank page...
Page 348: ...005 019 00 EN Blank page...
Page 357: ......
Page 358: ......
Page 360: ......
Page 363: ......
Page 366: ...005 020 00 EN Blank page...
Page 372: ...6 8 6 002 720 04 EN Blank page...
Page 374: ...005 021 00 EN Blank page...