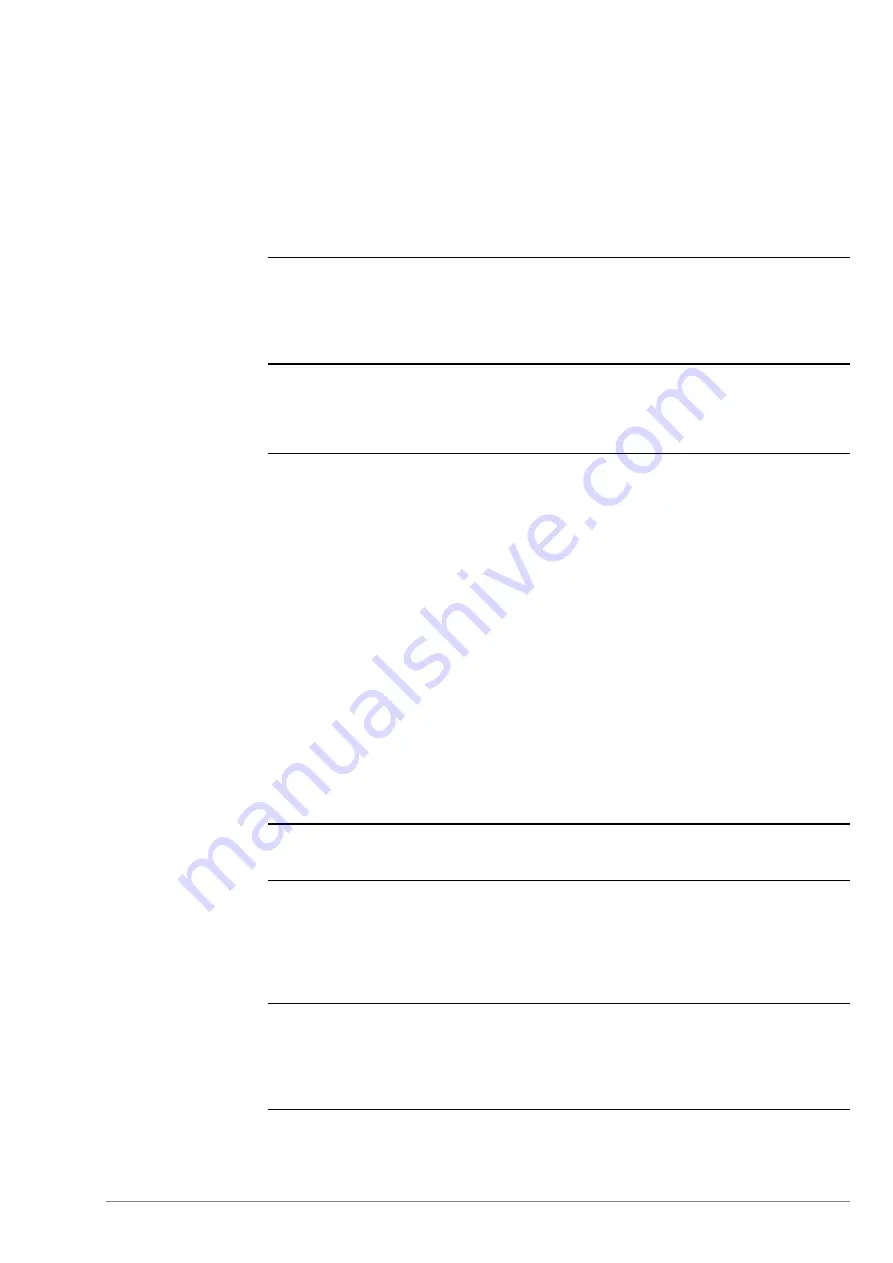
Schindler 3100/3300/6300
J 43402603 / 01
9/269
Copyright © 2017 INVENTIO AG
Returning to Normal
Operation
If the elevator has been commissioned, but used as a building elevator, or if it has been
taken out of service for an extended period of time, the following work must be carried
out by a competent person before the installation is put back into normal operation:
–
Clean and lubricate the installation.
–
Replace damaged components.
–
Check the safety elements.
Maintenance
Obligations
The installation described here conforms to Schindler quality standards. It was built in
accordance with the state of the art and the recognized safety regulations. In order to
ensure safe operation after handover, the installation must be regularly maintained by
competent persons.
Safety Components
Ensuring that all safety components are kept in safe operating condition. In order to
ensure safe operation, the safety components must be regularly maintained by
competent persons.
New Lifts Directive
The new lifts directive (Directive 2014/33/EU) will be transposed into the national law of
the member states of the European Union, Iceland, Lichtenstein and Norway (based on
their participation in the European Economic Area), Switzerland (based on a mutual
recognition agreement with the EU) and Turkey (based on a customs union with the EU)
as of 20 April 2016, and will replace the national legislation based on the current lifts
directive (Directive 95/16/EC) as of this date.
This means that all lifts that are placed on the market as of 20 April 2016 must comply
with the requirements of the new lifts directive. Lifts that have been placed on the market
before 20 April 2016 and that are in conformity with the current lifts directive (Directive
95/16/EC) may however still be put into service after this date.
One of the main changes introduced with the new lifts directive is the requirement to
ensure the traceability of safety components for lifts throughout the entire supply chain.
To meet the legal requirements, all safety components for lifts manufactured and/or
supplied by Schindler will be labelled with a standard type label that among other
information includes one or several of the following items: Ident, serial and batch
number, name and address of the manufacturer and importer of the safety component
for lifts, as well as a traceability tag (QR-Tag) for Schindler internal purposes.
Standard Schindler
Type Label
For standard Schindler type label, refer to section "Safety Components".
Handling of
Emergencies
When the handling of alarms is the responsibility of the owner of the installation, the
following has to be considered:
In the case of an emergency where there is no response from the car, it must be
assumed that the person in the car pressing the alarm button has impaired speech or
hearing. This requires immediate intervention by a competent person.
Restricted Access
Only competent persons are permitted to enter the machine room and hoistway. Building
maintenance and/or cleaning work in the machine room or in the hoistway must be
carried out only by competent persons or in the presence of a competent person. Prior to
such work, all safety measures and precautions must be in place.
Safety Precautions
Doors giving access to the machine room and hoistway for maintenance must be kept
locked at all times. It must, however, be possible to open the doors from the inside
without a key.
Access routes to the machine room and hoistway must be easy and safe to pass