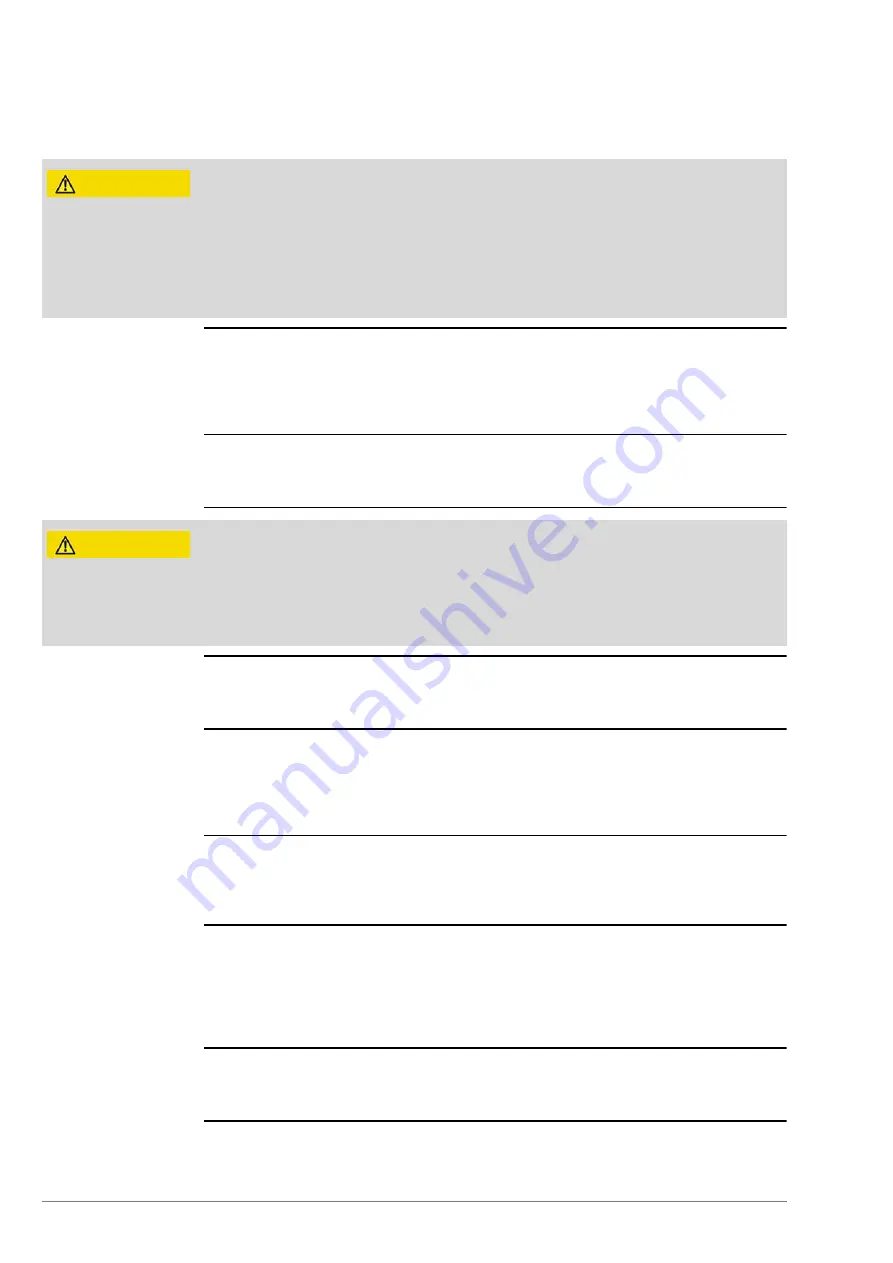
Schindler 3100/3300/6300
J 43402603 / 01
10/269
Copyright © 2017 INVENTIO AG
through at all times. If one or more of the access routes are blocked, the installation must
be taken out of service.
Access to Building
and Installation
For emergencies, and to carry out maintenance operations, safe access to the building
and to the installation must be guaranteed at all times. The access to the control and the
drive must be locked. The machine room key may only be made available to persons
authorized by the owner.
Maintenance
Operations
The owner of the installation must fulfill the requirements as laid down in the chapter
"Maintenance Information and Instructions".
Lighting
Adequate lighting of the machine room, hoistway and access routes must be guaranteed
at all times.
Temperature and
Ventilation
The owner of the installation must ensure that the temperature in the machine room and
in the hoistway is maintained b 5 °C and + 40 °C. The machine room and the
hoistway must be adequately ventilated. The machine room and the hoistway may not
be used for ventilating spaces which are not associated with the installation.
Lubricants and Oils
Only the lubricants and oils (gear oil) listed in the maintenance manual may be used.
The use of other lubricants can effect safety and cause extensive damage requiring
costly repairs.
Disposal
Used lubricants and oils must be taken back by the maintenance company and disposed
of in accordance with the legal requirements. Lubricants and in particular motor and
hydraulic oils belong to the classes of materials causing dangerous water pollution. Lead
accumulators and batteries containing lead have to be transported to the local Schindler
company for an adequate disposal.
Utilization of
Hoistway
The hoistway may not be used for other purpose than the elevator installation. It is not
permitted to have equipment present which does not belong to the installation.
CAUTION
Notification to the Maintenance Company
If irregularities in the installation are observed - (for example, leveling, noises,
vibrations, defective car lighting, start with a jerk, etc.) - the maintenance company
must be notified immediately.
The owner of the installation must also notify the maintenance company of any
changes that are imminent in the area of the installation, and whenever an emergency
has occurred.
CAUTION
Notification by the Owner of the Installation
According to the product liability laws, the installer must also keep track of its
installations even after commissioning and handover.
Therefore, damage to the installation or possible dangerous conditions must also be
reported to the installer by the owner of the installation.