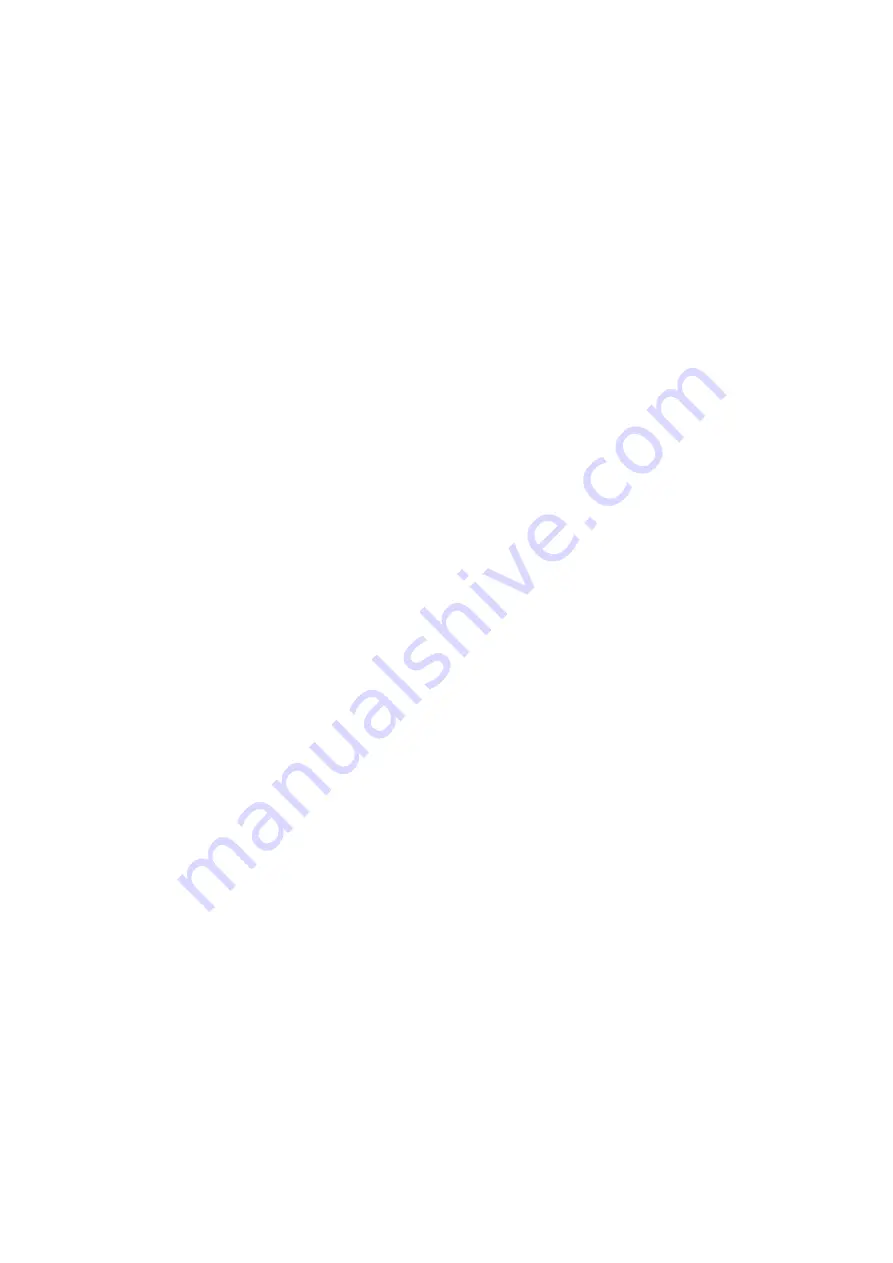
– 126 –
STORAGE WHEN NOT IN USE
To guarantee the operating reliability of the combine, proper service and storage are of great importance. The ser-
vice before winter storage can be divided into three parts, in order of performance: cleaning, checking and protec-
tion. A dry store or shed is ideal storage for the combine.
Cleaning:
Open the stone trap and all doors. Remove and wash all detachable guards, sieves, the bottom cassettes of the
grain pan and straw walkers as well as the grain tank bottom augers. Dirt is ef
¿
ciently removed from a dry com-
bine by compressed air. A high-pressure washer may be used with caution. To reduce drying time use warm water
and idle the threshing machinery.
Do not direct water jets at the bearings as the packing does not hold against a strong spray of water.
In normal seasons, it is not necessary to wash the inner parts of the combine in water; the inside of the combine
can be raked clean with a suitable tool. Apply suitable solvent on heavily greasy spots before washing.
Start cleaning from the top. Clean the radiator cells by blowing air from the direction of the engine.
Checking:
Take a pen and paper and write down all the shortcomings and required service measures in the following order:
Condition of knives.
Draw-in
¿
ngers and bearings.
Slip damages and breaks in belts and the remaining tensioning margin.
Condition of and basic settings for the cylinder and concave.
Condition of the grain pan and shaker shoe packing.
Bearing clearances and fastenings.
Wear, corrosion and dents.
Rotor knives and counter-knives of the chopper as well as rotor bearings.
It is important to have the recorded defects repaired before storage to ensure the ef
¿
cient functioning of the com-
bine at the beginning of the following harvesting season.
Protection:
Use pure engine oil or special protective oil in a sprayer.
Places to be protected:
Knife (protective oil)
Draw-in
¿
ngers (protective oil)
Worn paint (paint)
Electrical connections (special protective spray)
Chains (oil); rotate the mechanism by hand to ensure even lubrication.
Transmission chains (unloading and the reel) shall be disengaged, cleaned with a solvent and lubricated with
molybdenic oil.
Lubrication of the rotor knife joints of the chopper.
After protection all the cleaning doors, the grain pan and straw walker bottoms and sieves are left open to produce
a draught inside the combine. This will prevent rodents from nesting in the inner parts of the combine.
Pre-storage Service of the Air Conditioner:
Use compressed air to clean the cooler condenser and evaporator cells. In case the combine engine is run during
storage, the cooler should also be switched on for a few minutes. To operate the cooling system in cold weather,
have the heater on at full capacity and the ventilator fan stopped for approx. 15 min. during which time the air con-
ditioning sensor will warm up and enable the switching on of the compressor. After this the ventilator fan is run at
its lowest speed and the cooling at full capacity.
Summary of Contents for Comia c4
Page 2: ......
Page 16: ... 14 ...
Page 126: ... 124 C8 C8 C8 LUBRICATION DIAGRAM ...
Page 134: ... 132 M3 ...
Page 136: ... 134 M6 ...
Page 137: ... 135 M7 ...