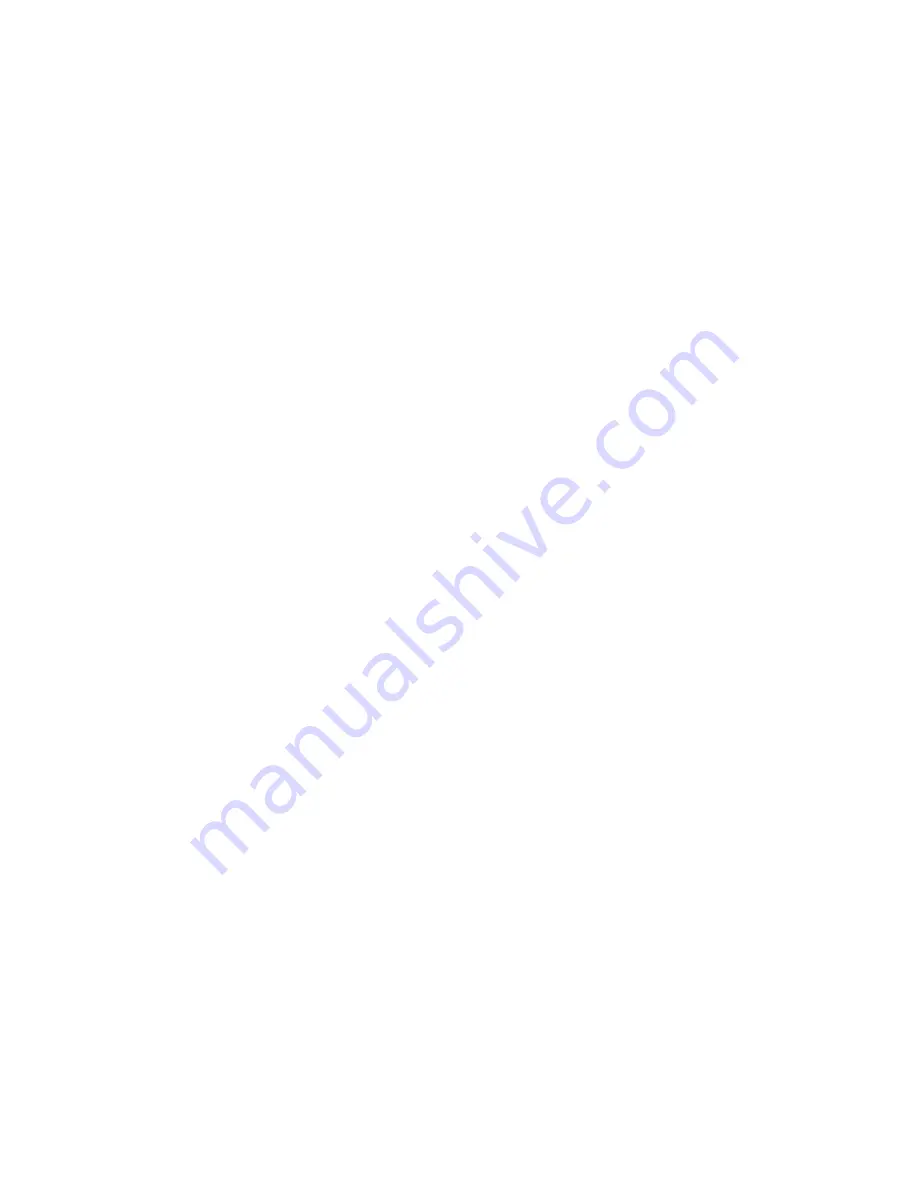
Section 2 Installation
F103/4/5A Manual
www.rottlermfg.com
2-13
Installation Procedure
Rottler F103/4/5 Series Foundation and Hold Down Requirements
Rottler machines require a good concrete foundation and hold down system. It is not recommended to
install a machine on a cracked floor or over an expansion joint. The layout/position of the hold down holes
can be found on the foundation drawings below.
There are two methods commonly used by customers:
1. Drill the concrete floor as per drawing layout before arrival of machine.
2. Place machine, mark floor through holes in machine base, move machine away then drill the floor.
The machine is provided with jacking bolts and steel pads to place between the jacking bolts and floor.
For shipping, the steel pads are packed in a separate box and marked with yellow/black tape so the box
is clearly visible. This allows the machine to be unpacked and removed from the shipping crate, placed
on the floor on these steel pads without opening the accessory crates. When placing the machine on the
jacking bolts, ALWAYS rough level to be sure that the weight of the machine is evenly distributed over all
the jacking bolts.
Rottler recommend Hilti products as per attached list. 3/4” (20mm) diameter X 12” (300mm) long studs
are recommended. Drill floor approx 7” (180mm) deep with 1” (25mm) drill. As it is difficult to drill concrete
exactly on center, it is recommended to drill a pilot hole. After drilling and before injecting epoxy, it is
also recommended to move the machine into place and make sure all studs fit through the holes in the
base and travel all the way down into the holes so that approx 5” (130mm) protrude out of the floor. The
machine may have to be moved a small amount to allow all studs to fit. Once this is checked, the studs
can be removed then the epoxy injected into the bottom of the holes. Make sure all dust is vacuumed out
of the holes before the epoxy is injected. Ensure that the epoxy is injected starting at the bottom of the
holes to be sure the stud has maximum contact with the epoxy. The size of the holes will determine how
much epoxy to inject into the holes before fitting the studs. On average, 1/2 to 2/3 of the hole should be
filled with epoxy before the stud is installed. Be sure when the stud is installed, that the epoxy fills the hole
to the top. Fit the washer and nut and tighten lightly to align the stud then allow the epoxy 24 hours to
harden ready for leveling and final anchoring.
The column is tied down with chains for transport, if it is required to move the column to help with
installation of the hold down system, the column tie downs can be removed and manually turn the
horizontal ball screw nut by hand to move the column sideways. Be sure that the rails are clean and lubed
under the column before moving.
The following is a
MINIMUM
recommendation for safe reliable operation.
4000 PSI concrete
Slab thickness of 12” (30cm)
Any slab that is thinner than this may require monitoring of levelness of the machine.
Summary of Contents for F103 Series
Page 2: ......
Page 4: ......
Page 10: ...Section 1 Introduction F103 4 5A Manual www rottlermfg com 1 5...
Page 21: ...Section 2 Installation F103 4 5A Manual www rottlermfg com 2 10...
Page 26: ...Section 2 Installation F103 4 5A Manual www rottlermfg com 2 15...
Page 43: ...Section 2 Installation F103 4 5A Manual www rottlermfg com 2 32...
Page 99: ...Section 5 Operating Instructions F103 4 5A Manual www rottlermfg com 5 12...
Page 102: ...Section 5 Operating Instructions F103 4 5A Manual www rottlermfg com 5 15...
Page 105: ...Section 5 Operating Instructions F103 4 5A Manual www rottlermfg com 5 18...
Page 106: ...Section 5 Operating Instructions F103 4 5A Manual www rottlermfg com 5 19...
Page 115: ...Section 5 Operating Instructions F103 4 5A Manual www rottlermfg com 5 28...
Page 189: ...Section 6 Maintenance F103 4 5A Manual www rottlermfg com 6 2 Grease Cross Reference Chart...
Page 190: ...Section 6 Maintenance F103 4 5A Manual www rottlermfg com 6 3...
Page 191: ...Section 6 Maintenance F103 4 5A Manual www rottlermfg com 6 4...
Page 192: ...Section 6 Maintenance F103 4 5A Manual www rottlermfg com 6 5...
Page 196: ...Section 6 Maintenance F103 4 5A Manual www rottlermfg com 6 9 Lubrication Locations...
Page 197: ...Section 6 Maintenance F103 4 5A Manual www rottlermfg com 6 10 Lubrication Locations cont...
Page 199: ...Section 6 Maintenance F103 4 5A Manual www rottlermfg com 6 12 Air Line Diagram...
Page 216: ...Section 6 Maintenance F103 4 5A Manual www rottlermfg com 6 29...
Page 217: ...Section 6 Maintenance F103 4 5A Manual www rottlermfg com 6 30...
Page 246: ...Section 6 Maintenance F103 4 5A Manual www rottlermfg com 6 59...
Page 267: ...Section 8 Machine Parts F103 4 5A Manual www rottlermfg com 8 2 Rear Left Sheet Metal...
Page 268: ...Section 8 Machine Parts F103 4 5A Manual www rottlermfg com 8 3 Right Rear Sheet Metal...
Page 269: ...Section 8 Machine Parts F103 4 5A Manual www rottlermfg com 8 4 Air Control Door...
Page 270: ...Section 8 Machine Parts F103 4 5A Manual www rottlermfg com 8 5 Air Control Solenoid Pack...
Page 271: ...Section 8 Machine Parts F103 4 5A Manual www rottlermfg com 8 6 Oiler Door...
Page 274: ...Section 8 Machine Parts F103 4 5A Manual www rottlermfg com 8 9 Enclosure Inside Parts...
Page 275: ...Section 8 Machine Parts F103 4 5A Manual www rottlermfg com 8 10 Enclosure Panel...
Page 276: ...Section 8 Machine Parts F103 4 5A Manual www rottlermfg com 8 11 DIN Rail Components...
Page 278: ...Section 8 Machine Parts F103 4 5A Manual www rottlermfg com 8 13 Computer Components...
Page 279: ...Section 8 Machine Parts F103 4 5A Manual www rottlermfg com 8 14 Spindle Base Right Side...
Page 280: ...Section 8 Machine Parts F103 4 5A Manual www rottlermfg com 8 15 Spindle Base Left Side...
Page 282: ...Section 8 Machine Parts F103 4 5A Manual www rottlermfg com 8 17 Motor Housing Parts...
Page 283: ...Section 8 Machine Parts F103 4 5A Manual www rottlermfg com 8 18 Z Axis Motor Parts...
Page 284: ...Section 8 Machine Parts F103 4 5A Manual www rottlermfg com 8 19 Counter Balance Pulley Parts...
Page 288: ...Section 8 Machine Parts F103 4 5A Manual www rottlermfg com 8 23 Upper Spindle Ballscrew Parts...
Page 289: ...Section 8 Machine Parts F103 4 5A Manual www rottlermfg com 8 24...
Page 290: ...Section 8 Machine Parts F103 4 5A Manual www rottlermfg com 8 25 Lower Spindle Ballscrew Parts...
Page 291: ...Section 8 Machine Parts F103 4 5A Manual www rottlermfg com 8 26...
Page 297: ...Section 8 Machine Parts F103 4 5A Manual www rottlermfg com 8 32 Pendant Swing Arm...
Page 299: ...Section 8 Machine Parts F103 4 5A Manual www rottlermfg com 8 34 Pendant Components...
Page 300: ...Section 8 Machine Parts F103 4 5A Manual www rottlermfg com 8 35 Main Base Parts...
Page 303: ...Section 8 Machine Parts F103 4 5A Manual www rottlermfg com 8 38 Chip Shield Assembly...
Page 304: ...Section 8 Machine Parts F103 4 5A Manual www rottlermfg com 8 39 Front Cover and Lights...
Page 305: ...Section 8 Machine Parts F103 4 5A Manual www rottlermfg com 8 40 Oil Line Diagram...
Page 307: ...Section 8 Machine Parts F103 4 5A Manual www rottlermfg com 8 42...
Page 309: ...Section 9 Options F103 4 5A Manual www rottlermfg com 9 2...
Page 311: ...Section 10 Material Data Safety Sheets F103 4 5A Manual www rottlermfg com 10 2...
Page 312: ...Section 10 Material Data Safety Sheets F103 4 5A Manual www rottlermfg com 10 3...
Page 313: ...Section 10 Material Data Safety Sheets F103 4 5A Manual www rottlermfg com 10 4...
Page 314: ...Section 10 Material Data Safety Sheets F103 4 5A Manual www rottlermfg com 10 5...
Page 315: ...Section 10 Material Data Safety Sheets F103 4 5A Manual www rottlermfg com 10 6...
Page 316: ...Section 10 Material Data Safety Sheets F103 4 5A Manual www rottlermfg com 10 7...
Page 317: ...Section 10 Material Data Safety Sheets F103 4 5A Manual www rottlermfg com 10 8...
Page 318: ...Section 10 Material Data Safety Sheets F103 4 5A Manual www rottlermfg com 10 9...