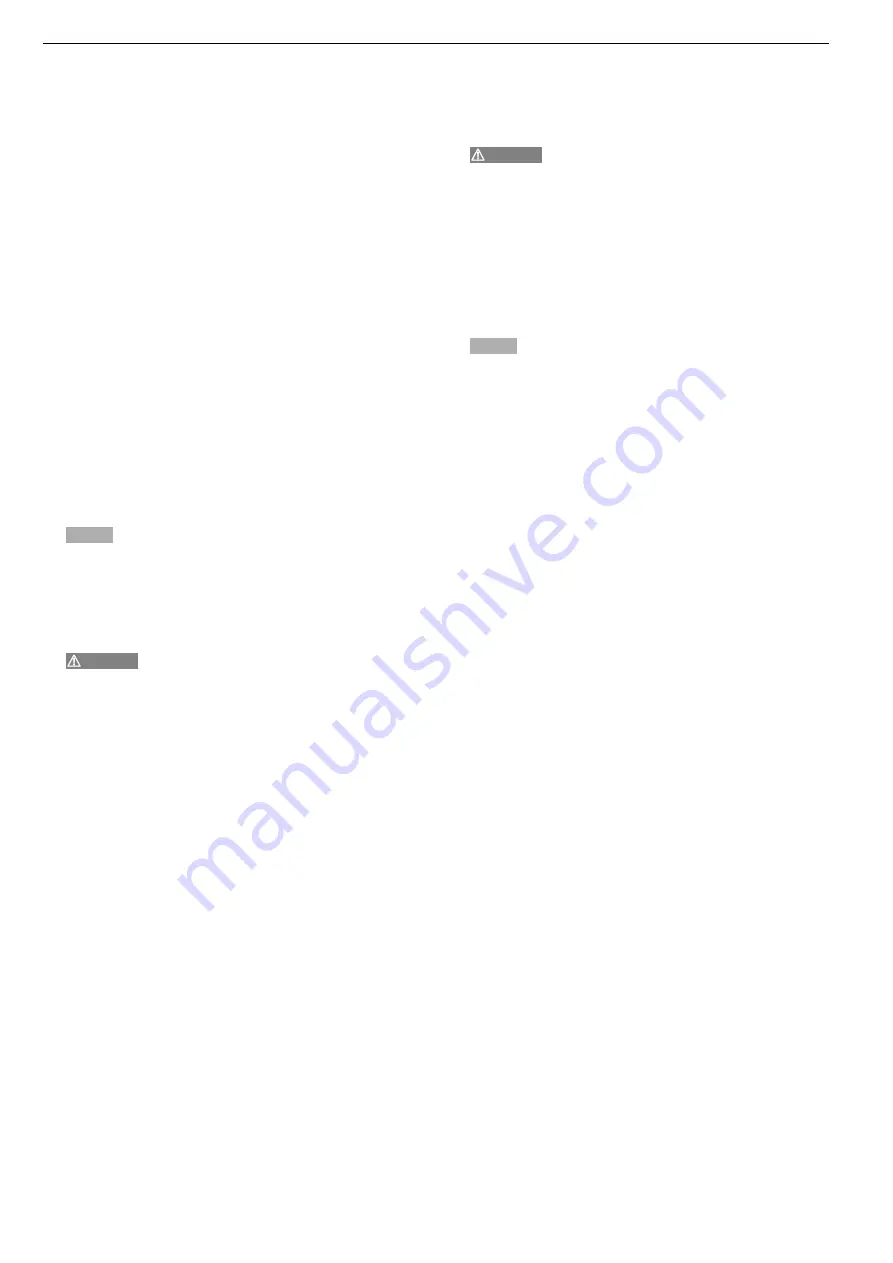
eng
eng
drive unit switches automatically to return and the expanding head is closed
again. Keep holding the inching switch (8) down and push the expanding head/
drive unit further. Keep repeating the expansion process until the expanding
jaws (17) are slid all the way into the pipe. Consult and comply with the instruc-
tions for installation and fitting of the system’s manufacturer.
Expanding with ROLLER’S Akku-Exparo P, ROLLER’S Akku-Exparo Cu
(Fig. 11, 12)
Push the compression sleeve over the pipe in the ROLLER’S Akku-Exparo P,
insert the expanding head into the pipe up to the stop and press the expanding
head/drive machine against the pipe. Switch on the drive machine (8). Make
sure that the compression sleeve is far enough away from the expanding head
in the expanding process because otherwise the expanding jaws (17) can bend
or break. Keep the inching switch (8) pressed until the pipe is expanded. This
is indicated by an acoustic signal (click). Expand several times if necessary.
Read and follow the installation and assembly instructions of the system
manufacturer.
In the ROLLER’S Akku-Exparo Cu, insert the expanding head into the pipe and
press the expanding head/drive machine against the pipe. Switch on the drive
machine. If the expanding head is open, the drive machine switches auto-
matically to return and the expanding head is closed again. Read and follow
the installation and assembly instructions of the system manufacturer.
3.4. Electronic battery charging status check with complete discharge protec-
tion
All ROLLER Akku presses made as of 2011-01-01 will be fitted with an electronic
battery charging status check with complete discharge protection and battery
charge indicator with 2-colour LED (23) green/red. The LED lights green when
the battery is fully or still sufficiently charged. The LED lights red when the
battery must be charged. The drive unit finishes off the current pressing cycle
and can then only be switched on again when a charged battery is inserted. If
the drive unit is not used, the LED goes out after 2 hours but comes on again
when the tool is switched back on.
4. Maintenance
NOTICE
Notwithstanding the maintenance listed below it is necessary to
send in the ROLLER drive units together with all the tools (e.g. pressing tongs,
pressing tongs Mini, pressing rings with adapter tongs, compression heads,
expanding heads) at least once a year to an authorised ROLLER customer
service station for inspection. This opportunity is also taken to carry out the
prescribed annual inspection of electrical equipment in accordance with EN
62638 (VDE 0702) for power tools.
4.1. Maintenance
WARNING
Before maintenance work, pull the mains plug or remove
the battery!
Keep the pressing tongs, pressing tongs Mini, adapter tongs, pressing rings,
pressing heads and expanding heads, and particularly their receptacles, clean.
Clean heavily soiled metal parts with turpentine oil, for example, and then
rustproof them.
Clean plastic parts (for ex. housing, batteries) only with a mild soap and a damp
cloth. Do not use domestic cleaning agents. These frequently contain chemicals
that can attack plastic parts. On no account use petrol, turpentine oil, thinners
or similar products to clean plastic parts.
Ensure that liquids never get inside the electrical equipment. Never immerse
the electrical equipment in liquid.
4.1.1. Pressing tongs, pressing tongs Mini, adapter tongs and pressing rings
Pressing tongs, pressing tongs Mini, pressing rings and adapter tongs must
be checked regularly for smooth action. Clean pressing tongs, pressing tongs
Mini, pressing rings and adapter tongs if necessary and lubricate the bolts (12)
of the pressing jaws, pressing segments and adapter jaws with machine oil.
Remove deposits from the pressing contour (11). Check the proper functioning
of all pressing tongs, pressing tongs Mini, pressing rings and adapter tongs
regularly with a test pressing with inserted pressing fitting. The pressing jaws
(10) must close fully both at their tips (Fig. 1, at "A") and at the height of the
connecting lug (Fig. 1 at "B") after completing the pressing. The pressing
segments (21) must closed after completing the pressing. Damaged or worn
pressing tongs, pressing tongs Mini, pressing rings and adapter tongs may no
longer be used. In case of doubt, send in the drive machine together with all
pressing tongs, pressing tongs Mini, pressing rings and adapter tongs to an
authorised ROLLER after-sales service facility for inspection.
4.1.2. Radial presses
Keep the press tongs receptacle clean, in particular clean the press rollers (5)
and tongs shank (2) at regular intervals and then lubricate them with machine
oil. Check the functional reliability of the drive unit regularly by making a pressing
with the largest press fitting used. If the pressing tongs, pressing tongs Mini
close completely during this pressing operation (see above), the drive unit is
functionally reliable.
4.1.3. Axial presses
Keep the pressing heads (14) and locating holes inside the pressing device
clean. Keep the expanding heads (16) and expanding mandrel (18) clean.
Lightly grease the expanding mandrel (18) from time to time.
4.1.4. Pipe expanders
ROLLER’S Akku-Exparo Q & E, ROLLER’S Akku-Exparo-Press P, ROLLER’S
Akku-Exparo Cu, keep the expanding device (15), expanding heads (16) and
expanding mandrel (18) clean. Lightly grease the expanding mandrel (18) from
time to time.
4.2. Inspection/repair
WARNING
Before any repair work, pull the mains plug or remove the
battery!
This work may only be performed by qualified personnel.
An annual inspection is recommended for all press/expanding tools (including
pressing tongs, pressing tongs Mini).
The gearbox of the drive unit in the ROLLER’S Uni-Press E is maintenance -
free. They operate in a permanent grease filling and therefore require no
lubrication. The motor of the ROLLER’S Uni-Press E, ROLLER’S Uni-Press
and ROLLER’S Uni-Press ACC has carbon brushes. These are subject to wear
and must therefore be inspected or replaced from time to time. Only use genuine
ROLLER’S Uni-Press carbon brushes. The ROLLER Akku drive units operate
electrohydraulically. If the pressing power is insufficient or oil is lost, the drive
unit must be inspected and if necessary repaired by ROLLER or by an author-
ised ROLLER after-sales service facility.
NOTICE
Damaged or worn pressing tongs, pressing tongs Mini, pressing
rings, pressing heads or expanding heads cannot be repaired.
5. Trouble
5.1. Trouble:
Drive unit does not operate.
Cause:
● Worn carbon brushes (ROLLER’S Uni-Press E,
ROLLER’S Uni-Press, ROLLER’S Uni-Press ACC).
● Mains lead defective (ROLLER’S Uni-Press E,
ROLLER’S Uni-Press, ROLLER’S Uni-Press ACC).
● Battery empty or defective (ROLLER Akku drive units).
● Drive unit defective.
5.2. Trouble:
Radial press does not finish pressing operation, pressing tongs,
pressing tongs Mini, adapter tong, pressing ring does not close
completely.
Cause:
● Drive unit overheated (ROLLER’S Uni-Press E,
ROLLER’S Uni-Press, ROLLER’S Uni-Press ACC).
● Worn carbon brushes (ROLLER’S Uni-Press E,
ROLLER’S Uni-Press, ROLLER’S Uni-Press ACC).
● Slipping clutch defective (ROLLER’S Uni-Press E).
● Battery empty or defective (ROLLER Akku drive units).
● Drive unit defective.
● Incorrect pressing tong, pressing tong Mini, pressing ring or adapter tong
(pressing contour, size) inserted.
● Pressing tong, pressing tong Mini, pressing ring or adapter tong with
stiff action or defective.
● The pipe is squeezed in between the compression sleeve and the fitting
collar (ROLLER axial presses).
5.3. Trouble:
Expander does not finish the expanding, expanding head does
not open completely.
Cause:
● Battery flat or defective (ROLLER cordless drive machines)
● Defective drive machine
● Wrong expanding head (pressing contour, size) used
● Expanding head too tight or defective
● Expanding device set incorrectly (ROLLER’S Akku-Exparo Cu).
● Compression sleeve and expanding head not far enough apart
5.4. Trouble:
During closing of the pressing tong, pressing tong Mini or pressing
ring, a marked ridge is created on the compression sleeve.
Cause:
● Damaged or worn pressing tong, pressing tong Mini or pressing ring /
pressing contour.
● Incorrect pressing tong, pressing tong Mini, pressing ring or adapter tong
(pressing contour, size) inserted.
● Unsuitable matching of compression sleeve, pipe and support sleeve.
5.5. Trouble:
In axial presses, the pipe is squeezed in between the
compression sleeve and fitting collar.
Cause:
● Wrong expanding head (pressing contour, size) used
● Unsuitable matching of compression sleeve, pipe and support sleeve.
5.6. Trouble:
Pressing jaws close unevenly when the pressing tongs, pressing
tongs Mini are not loaded at “A” and “B” (Fig. 1).
Cause:
● Pressing tong, pressing tong Mini, adapter tong have been dropped,
compression spring is bent.
5.7. Damages
For preventing damages make sure to avoid operating situations like exempla-
rily shown in Fig. 14 through 16, that no distortion between pressing tongs,
pressing tongs Mini, pressing rings, adapter tongs, fitting and drive unit occurs.