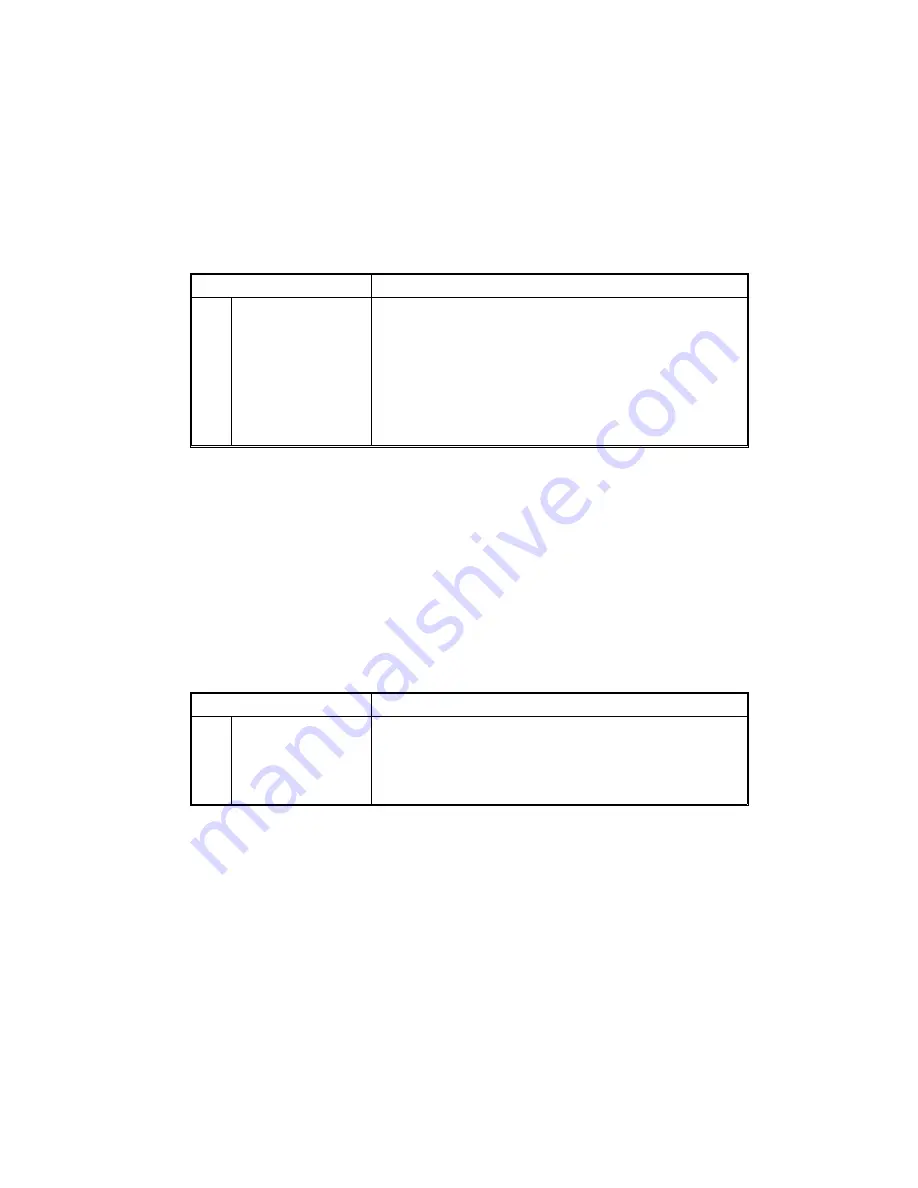
4) Plug in the machine and turn on the main switch, then lower the platen
cover.
5) Enter the SP mode as follows:
a) Enter "71" using the numeral keys.
b) Press and hold the Clear/Stop key until a dot (
•
) appears in the top
left corner of the copy counter.
c) Release the Clear/Stop key and again press the Clear/Stop key.
d) Press the Lighter key.
6) Perform SP 12 as follows:
SP Mode Number
Procedure
12
Conversion from
220
∼
230V to
240V.
Enter "12" using the numeral keys. Then, press
the Auto Image Density key.
Change the data from "0" to "1" using numeral
key.
Then, press the Auto Image Density key.
"12" will start blinking.
Go to the step 15. 3).
15. Perform the developer initial setting.
1) Plug in the machine and turn on the main switch, then lower the platen
cover.
2) Enter the SP mode as follows:
a) Enter "71" using the numeral keys.
b) Press and hold the Clear/Stop key until a dot (
•
) appears in the top
left corner of the copy counter.
c) Release the Clear/Stop key and again press the Clear/Stop key.
d) Press the Lighter key.
3) Perform SP 65 as follows:
SP Mode Number
Procedure
65
Developer Initial
Setting
Enter "65" using the numeral keys and press the
Auto Image Density key. "50" will be displayed
in the copy counter. Press the Start key for
initial setting.
A151/A152
3-8
FSM
Summary of Contents for A151
Page 1: ...SERVICE MANUAL PN RCFM3213 A151 A152 A202 A203 RICOH GROUP COMPANIES ...
Page 2: ...SERVICE MANUAL A151 A152 A202 A203 RICOH GROUP COMPANIES ...
Page 3: ...A151 A152 A202 A203 FIELD SERVICE MANUAL PN RCFM3213 ...
Page 4: ......
Page 6: ......
Page 8: ......
Page 10: ......
Page 22: ......
Page 26: ......
Page 27: ...OVERALL MACHINE INFORMATION ...
Page 28: ......
Page 32: ......
Page 33: ...GUIDE TO COMPONENTS ...
Page 34: ......
Page 42: ......
Page 43: ...INSTALLATION ...
Page 44: ......
Page 55: ...SERVICE TABLES ...
Page 56: ......
Page 95: ...REPLACEMENT AND ADJUSTMENT ...
Page 96: ......
Page 193: ...TROUBLESHOOTING ...
Page 194: ......
Page 250: ......
Page 251: ...DOCUMENT FEEDER A296 ...
Page 252: ......
Page 268: ......
Page 274: ......
Page 277: ...A202 A203 SERVICE MANUAL ...
Page 278: ......
Page 337: ...DOCUMENT FEEDER A662 ...
Page 338: ......
Page 359: ...TECHNICAL SERVICE BULLETINS ...
Page 360: ......
Page 372: ...Tech Service Bulletin No 3013 3213 008 Page 2 of 3 Continued ...
Page 373: ...Tech Service Bulletin No 3013 3213 008 Page 3 of 3 ...