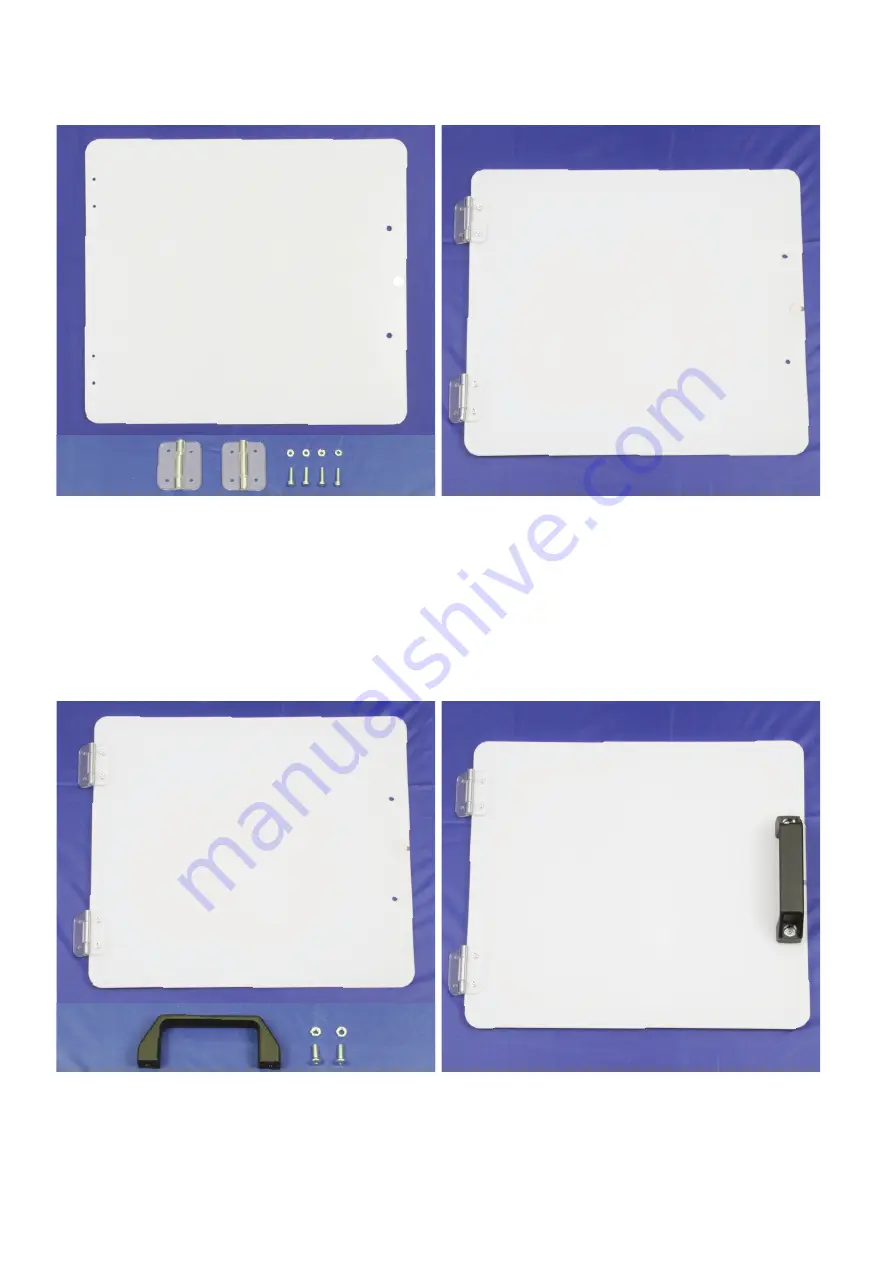
59
b) Assembly of the door
Attaching the hinges
1x door
2x hinges
4x cylinder head screws M3x12
4x screw nuts M3
Remove the protective film around the 4 boreholes for the hinges.
Screw them tight to the outside of the door using the M3 cylinder head
screws and nuts.
You can recognise the outside by the magnet. It is inserted into the
door from the outside, i.e. the side where you can touch the magnet
directly is on the outside.
The order is:
Cylinder head screw - hinge - door - screw nut
Attaching the handle
1x door with attached hinges
1x handle
2x countersunk screws M5x16
2x screw nut M5
Remove the protective film around the two boreholes for the handle
and attach it also to the outside of the door using the M5 countersunk
screws and nuts.
The order is:
Countersunk screw - handle - door - screw nut