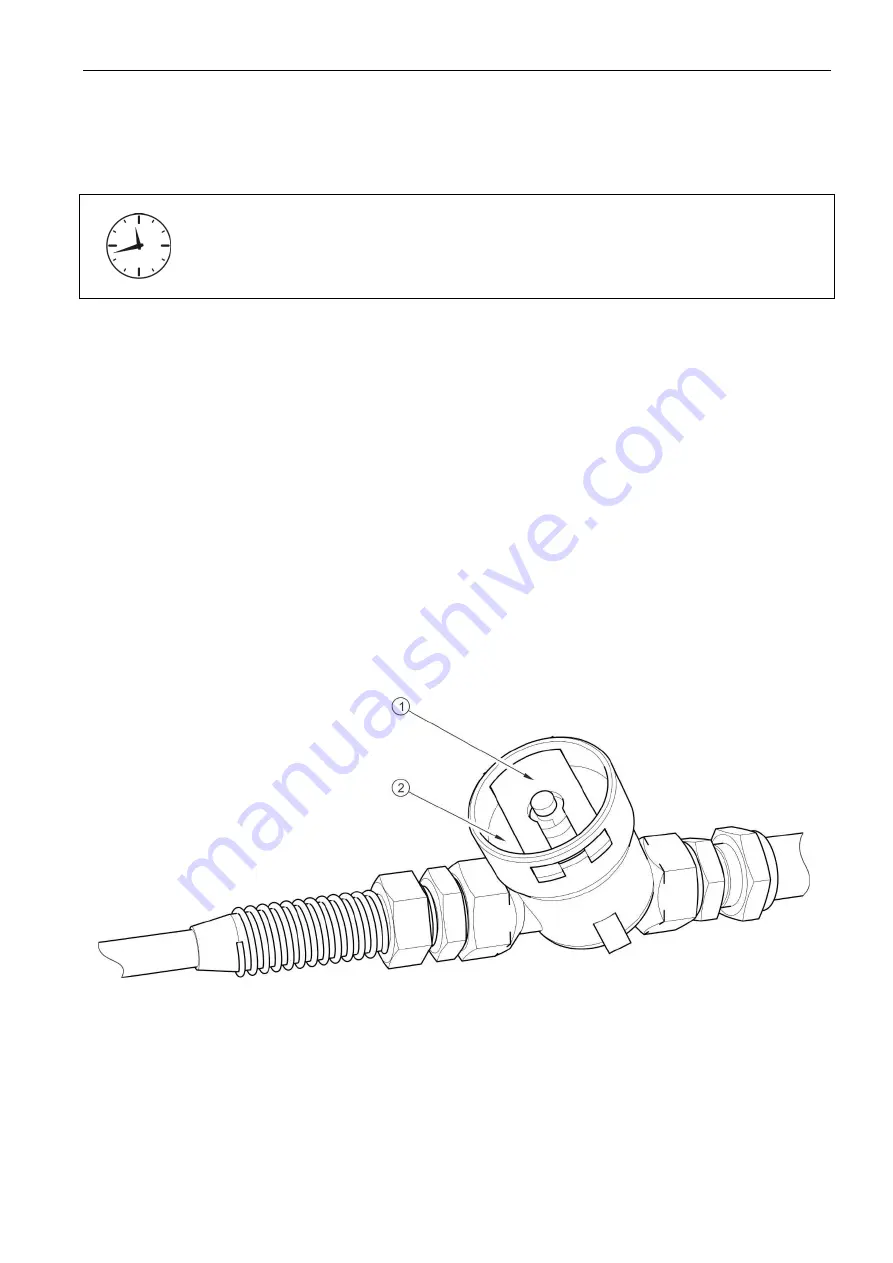
SECTION 5
PRONAR T679/5
5.21
5.3.3 INSPECTION OF THE SYSTEM
INSPECTION
•
Each time during tightness inspection.
During tightness inspection attention should additionally be given to technical condition and
degree of cleanness of the system components. Contact of pneumatic conduit seals etc. with
oil, grease, petrol etc. may cause damage and accelerate the ageing process. Bent,
permanently deformed, cut or worn conduits should be replaced.
5.4 CLEANING THE AIR FILTERS
Depending on trailer working conditions, but not less than once in three months, take out and
clean air filter elements, which are located in pneumatic system connection conduits. Inserts
are used many times and are not subject to changing unless they are mechanically
damaged.
FIGURE 5.12 Air filter
(1) securing slide lock, (2) air filter cover
Required maintenance activities
Reduce pressure in supply conduit.
Summary of Contents for T679/5
Page 2: ......
Page 6: ......
Page 11: ...SECTION 1 BASIC INFORMATION ...
Page 26: ...PRONAR T679 5 SECTION 1 1 16 ...
Page 27: ...SECTION 2 SAFETY ADVICE ...
Page 37: ...SECTION 2 PRONAR T679 5 2 11 FIGURE 2 2 Locations of information and warning decals ...
Page 38: ...PRONAR T679 5 SECTION 2 2 12 ...
Page 39: ...SECTION 3 DESIGN AND OPERATION ...
Page 53: ...SECTION 4 CORRECT USE ...
Page 72: ...PRONAR T679 5 SECTION 4 4 20 ...
Page 73: ...SECTION 5 MAINTENANCE ...
Page 101: ...SECTION 5 PRONAR T679 5 5 29 FIGURE 5 14 Trailer s lubrication points ...
Page 114: ...PRONAR T679 5 SECTION 5 5 42 ...
Page 115: ...NOTES ...
Page 116: ... ...