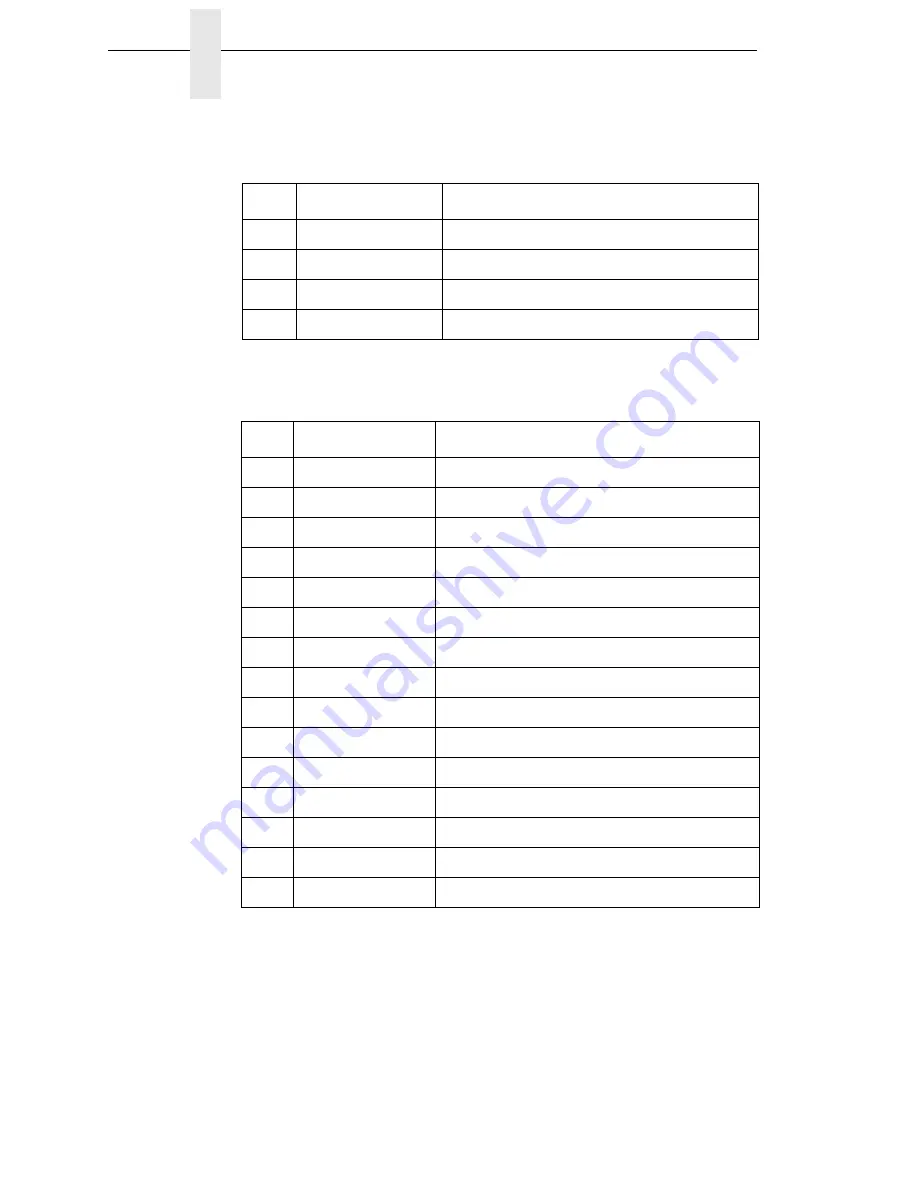
II–210
Appendix A
Input / Output Signals
Connector CN16 (not used)
Table II–36. Connector CN14
Pin
Abbreviation
Signal Name
1
LTSH
Lamp Thermistor
2
LTSHG
Lamp Thermistor (Ground)
3
LTF
Lamp Temperature Fuse
4
SG
Signal Ground
Table II–37. Connector CN15
Pin
Abbreviation
Signal Name
1
S24
+24V (Power)
2
DSPSA
Drum Surface Potential Sensor A (Output)
3
DSPSB
Drum Surface Potential Sensor B (Sealed)
4
SG
Signal Ground
5
P24
+24V (Power)
6
HCF
Head Cooling Fan
7
P24
+24V (Power)
8
HBF
Head Blower Fan
9
P24
+24V (Power)
10
SPS
Separator Pick Solenoid
11
P24
+24V (Power)
12
FCF
Fuser Cooling Fan
13
PEL
Erase Lamp
14
PG
Power Ground
15
NC
No Connection
Summary of Contents for L5535
Page 1: ...Maintenance Manual Volume II of II L5535 Multifunction Printer...
Page 2: ......
Page 3: ...Maintenance Manual L5535 Multifunction Printer Volume II of II...
Page 6: ......
Page 18: ...Table of Contents...
Page 21: ...II 21 Parts lists begin on the next page...
Page 26: ...II 26 Chapter 7 Illustrated Parts Breakdown Figure II 16 Developing Unit A 5 10 15 15 Ref A...
Page 28: ...II 28 Chapter 7 Illustrated Parts Breakdown Figure II 17 Miscellaneous Details 5 10 15...
Page 36: ...II 36 Chapter 7 Illustrated Parts Breakdown Figure II 20 Fuser Unit Sheet 1 of 4 5 A...
Page 37: ...II 37 Figure II 20 Fuser Unit Sheet 2 of 4 A C 10 15 B D 16 17 40 45...
Page 38: ...II 38 Chapter 7 Illustrated Parts Breakdown Figure II 20 Fuser Unit Sheet 3 of 4 C B 20 25...
Page 39: ...II 39 Figure II 20 Fuser Unit Sheet 4 of 4 D 30 35 This view is rotated 180...
Page 40: ...II 40 Chapter 7 Illustrated Parts Breakdown Parts lists continue on the next page...
Page 52: ...II 52 Chapter 7 Illustrated Parts Breakdown Figure II 25 LED Print Head LED Array 5 10 15 20...
Page 55: ...II 55 Figure II 26 Cut Sheet Feeder Assembly Sheet 2 of 4 B 64 62 62 61 5 65 60...
Page 57: ...II 57 Figure II 26 Cut Sheet Feeder Assembly Sheet 4 of 4 D E Ref 10 11 Ref 15...
Page 58: ...II 58 Chapter 7 Illustrated Parts Breakdown Parts lists continue on the next page...
Page 61: ...II 61 Figure II 27 Front View Left Side Sheet 2 of 3 C 30 25 35 42 42 40 40 37 38 39...
Page 64: ...II 64 Chapter 7 Illustrated Parts Breakdown Figure II 28 MC PCBA 5...
Page 69: ...II 69 Figure II 30 Controller Module Sheet 2 of 3 45 A A...
Page 72: ...II 72 Chapter 7 Illustrated Parts Breakdown Figure II 31 Head Blower Fan Assembly 5 10...
Page 76: ...II 76 Chapter 7 Illustrated Parts Breakdown Figure II 33 General Details Sheet 1 of 2 5 10...
Page 77: ...II 77 Figure II 33 General Details Sheet 2 of 2 15 15 20 25...
Page 78: ...II 78 Chapter 7 Illustrated Parts Breakdown Parts lists continue on the next page...
Page 80: ...II 80 Chapter 7 Illustrated Parts Breakdown Figure II 34 Smoke Filter Box 5 10...
Page 84: ...II 84 Chapter 7 Illustrated Parts Breakdown Figure II 36 Flash Power Supply A 10 A...
Page 86: ...II 86 Chapter 7 Illustrated Parts Breakdown Figure II 37 Miscellaneous Details 5 10...
Page 88: ...II 88 Chapter 7 Illustrated Parts Breakdown Figure II 38 DC Main Power Supply 10 15 20...
Page 91: ...II 91 Figure II 39 Back View Left Side Sheet 2 of 5 A 45 40 20 25 30 30 35 B 21...
Page 93: ...II 93 Figure II 39 Back View Left Side Sheet 4 of 5 C 60 65 70 80 75 85 90 95 90 95 100 D...
Page 98: ...II 98 Chapter 7 Illustrated Parts Breakdown Figure II 41 Flash Duct Assembly 5...
Page 103: ...II 103 Figure II 43 Back of Printer Left Side Sheet 2 of 6 A 5 10 15 15...
Page 105: ...II 105 Figure II 43 Back of Printer Left Side Sheet 4 of 6 E F 31 35...
Page 108: ...II 108 Chapter 7 Illustrated Parts Breakdown Parts lists continue on the next page...
Page 110: ...II 110 Chapter 7 Illustrated Parts Breakdown...
Page 170: ...II 170 Chapter 8 Operational Sequences...
Page 173: ...II 173 Print Engine Interconnection Diagram Diagram continues on the next page...
Page 262: ...262 Appendix B Cut Sheet Output Unit...
Page 267: ...Setup II 267 Power Stacker Hook Printer Stud Printer Stud...
Page 277: ...Swinger II 277 Swinger The swinger is driven by the swinger motor Swinger Motor Swinger...
Page 299: ...Inside The Right Frame II 299 Inside The Right Frame Belt E S3M825...
Page 344: ...II 344 Appendix D Memory Operation Menu...
Page 357: ......