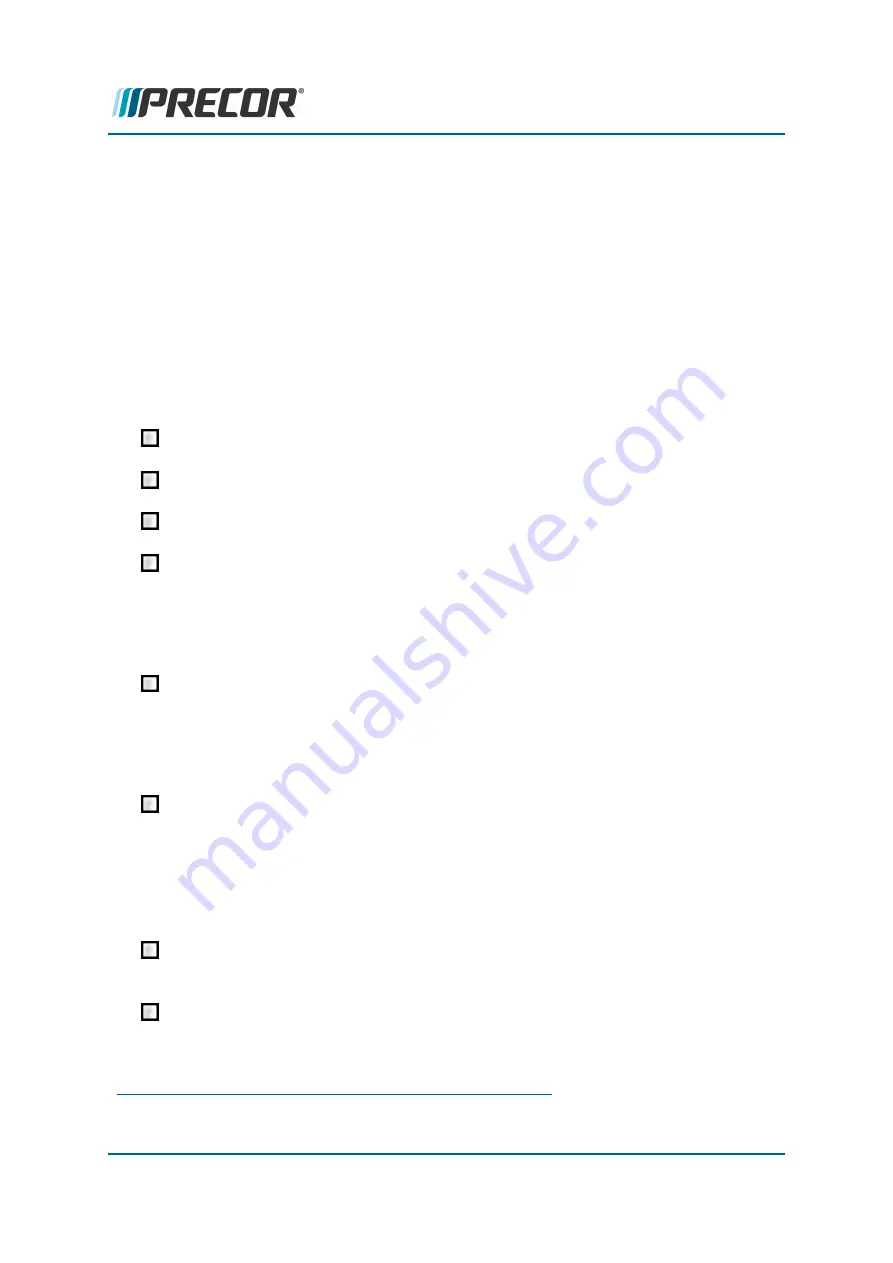
Operation Verification
About
Use the Operation Verification Checklist to verify the bike operation. Verify the bike oper-
ation at the completion of any maintenance procedure and when it is necessary to ensure
that the bike is operating properly.
Operation Verification Checklist
Do an overall visual inspection of the bike looking for any loose hardware and/or miss-
ing parts. .Repair and replace as needed.
Verify that the bike sets level and is stable on the floor, see
Verify that the seat position is level and does not rotate or tilt. Tighten and adjust as
needed.
Verify that the seat height and forward/back adjustment work correctly.
l
Make sure that the seat post up/down movement is smooth and that the pop-
pins lock at different positions. .
l
Make sure the forward/back slider movement is smooth and the adjustment
knob locks the seat in position.
Verify that the handlebar height and forward/back adjustment work correctly.
l
Make sure the handlebar post up/down movement is smooth and that the pop-
pins lock at different positions.
l
Make sure the forward/back slider movement is smooth and the adjustment
knob locks the handlebar in position.
Set the resistance to minimum and pedal the bike at a moderate pace (55 rpm or
greater), increase the resistance to maximum and return to zero resistance.
l
Verify that the resistance knob functions normally from min to max resistance.
l
Verify that there were no unusual noises from the brake pads or flywheel during
operation.
l
Verify that at maximum resistance, the bike was very hard to pedal.
Pedal the bike at a moderate pace (55 rpm or greater), stop pedaling and press down
on the resistance knob. Verify that the flywheel immediately begins to slow and
quickly stops.
Power (Watts) measurement AutoCal verification:
(Spinner
®
Chrono
1
™ Power only).
l
Set the resistance to minimum and pedal the bike at 55 rpm or greater.
1
Spinner® Chrono™ Power bike.
Contact Precor Customer Support at [email protected] or 800.786.8404 with
any questions.
Page 14
3 Operation Verification
About