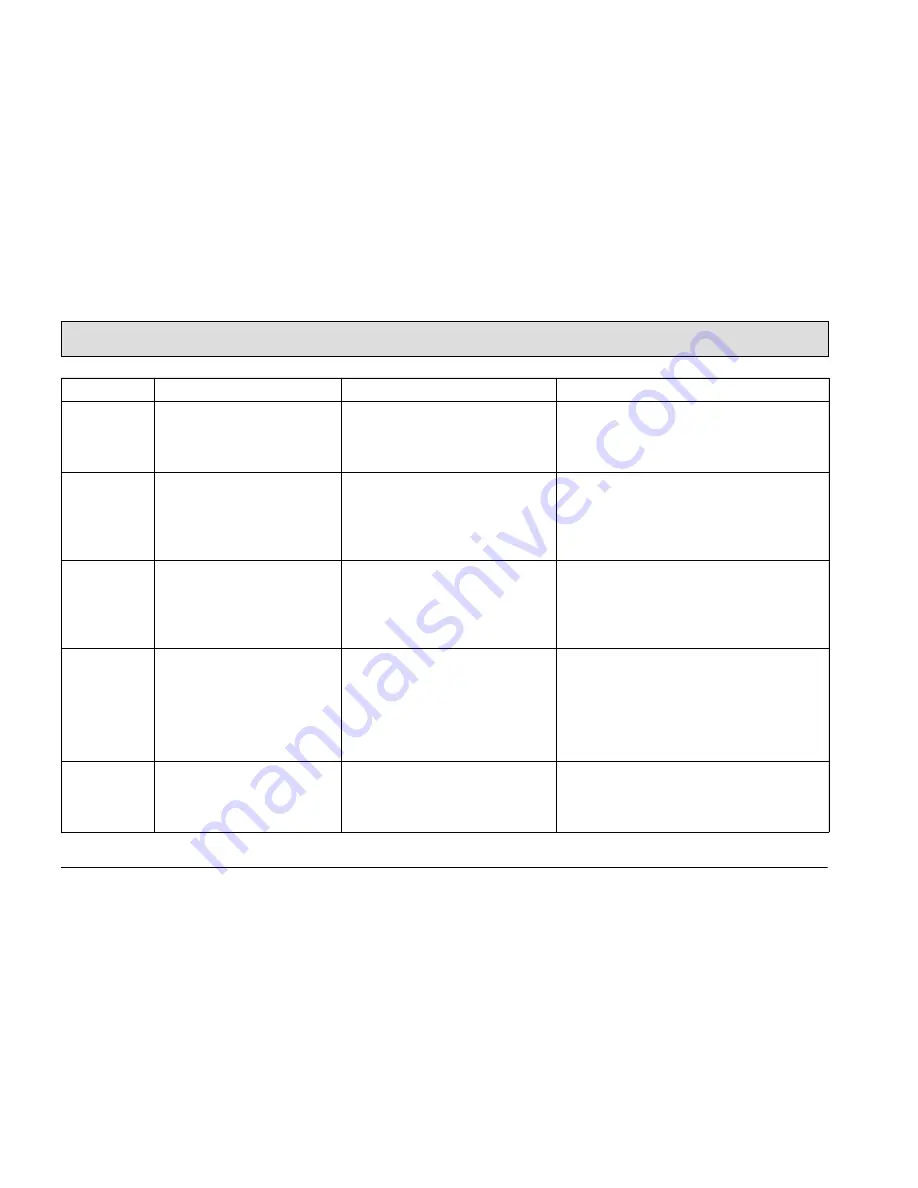
64
Operation
Error code
Fault
Cause
Solution
1.2.6.2.
Brushes remain stopped
because the anti-blocking
system of the third, middle
brush has been tripped.
Foreign bodies (e.g. tape or
such) block the brushes
• Check the brush for foreign bodies,
remove them as necessary.
1.2.6.3.
The brush attachment and
brush motors have been
switched off because the
anti-blocking system has
been tripped.
Foreign bodies between the
brush head and vehicle.
• Check the brush head for foreign bodies
and remove them, as necessary.
1.4.6.1.
Squeegee holding
attachment has been
switched off because the
anti-blocking system has
been tripped
• Foreign bodies between the
squeegee and vehicle.
• Squeegee is jammed
• Check the squeegee attachment for
foreign bodies and remove them, as
necessary
• Free the squeegee.
2.2.5.1
Cylindrical brush remains
stopped because the
thermostatic switch has
been tripped.
The motor has overheated.
Foreign bodies (e.g. tape or
such) possibly block the
cylindrical brush.
• Check the cylindrical brush for foreign
bodies and remove them, as necessary.
• Allow the motor to cool down.
• If the problem reoccurs, determine the
cause of overheating; contact an
authorized PowerBoss service center, if
necessary.
2.2.6.1
Cylindrical brush remains
stopped because the anti-
blocking system has been
tripped.
Foreign bodies (e.g. tape or
such) block the cylindrical brush.
Check the cylindrical brush for foreign
bodies and remove them, as necessary.
Summary of Contents for Admiral 48D
Page 1: ...Instruction Manual Admiral 48D 7580 45...
Page 54: ...54 Operation 13Seat console 14Electrical compartments 15Side door Fig 24 13 14 15...
Page 116: ......
Page 117: ......
Page 118: ......
Page 119: ......