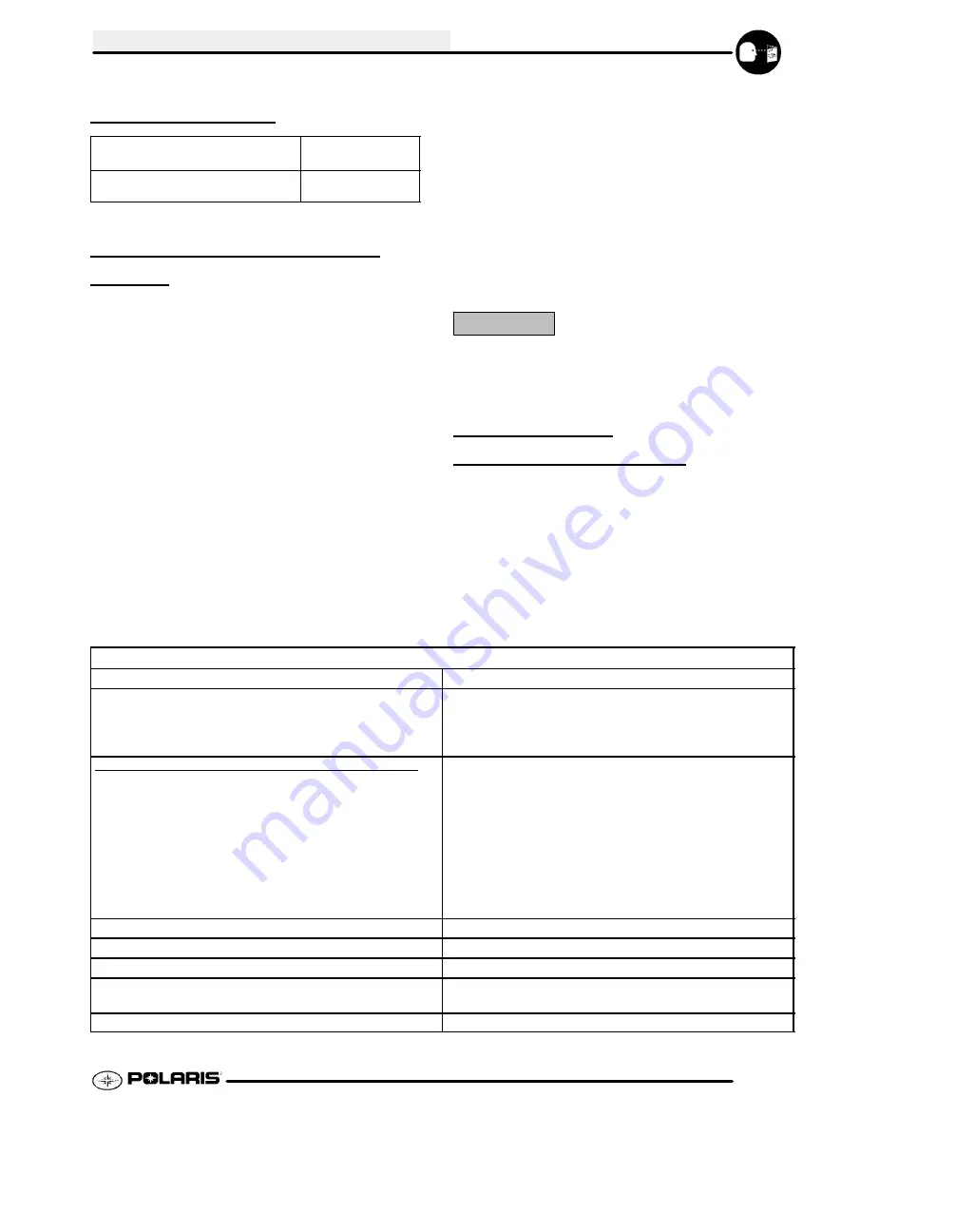
GENERAL INFORMATION
9.3
SPECIAL TOOLS
PART NUMBER
TOOL
DESCRIPTION
2870975
Mity Vac
t
Pressure Test Tool
BRAKE SYSTEM SERVICE
NOTES
Disc brake systems are light weight, low
maintenance, and perform well in the conditions ATVs
routinely encounter.
There are a few things to
remember when replacing disc brake pads or
performing brake system service to ensure proper
system function and maximum pad service life.
S
Optional pads are available to suit
conditions in your area. Select a pad to fit
riding style and environment.
S
Do not over-fill the master cylinder fluid
reservoirs.
S
Make sure the brake levers return freely
and completely.
S
Adjust stop pin on front caliper after pad
service.
S
Check and adjust master cylinder
reservoir fluid levels after pad service.
S
Make sure atmospheric vent on reservoirs
are unobstructed.
S
Test for brake drag after any brake system
service and investigate cause if brake
drag is evident.
S
Make sure caliper moves freely on guide
pins.
S
Inspect caliper piston seals for foreign
material that could prevent caliper pistons
from returning freely.
S
Perform a brake burnishing procedure
after installing new pads to maximize
service life.
CAUTION:
Use only DOT 3 brake fluid as an
assembly aid for all procedures described in this chapter to
prevent brake system contamination. DO NOT USE
LUBRICANTS OF ANY KIND FOR ASSEMBLY.
BRAKE NOISE
TROUBLESHOOTING
Dirt or dust buildup on the brake pads and disc is the
most common cause of brake noise (squeal caused by
vibration). If cleaning does not reduce the occurrence
of brake noise, Permatex
t
Disc Brake Quiet (
PN
2872113
) can be applied to the back of the pads. Follow
directions on the package.
This will keep pads in
contact with caliper piston(s) to reduce the chance of
squeaks caused by dirt or dust. See table below.
Brake Noise Troubleshooting
Possible Cause
Remedy
Dirt, dust, or imbedded material on pads or disc
Spray disc and pads with CRC Brakeleen
t
or an
equivalent non-flammable aerosol brake cleaner. Re-
move pads and/or disc hub to clean imbedded material
from disc or pads.
Pad(s) dragging on disc (noise or premature pad wear)
Improper adjustment
Insufficient lever or pedal clearance
Master cylinder reservoir overfilled
Master cylinder compensating port restricted
Master cylinder piston not returning completely
Caliper piston(s) not returning
Operator error (riding the brake / park brake
applied)
Adjust pad stop (front calipers)
Check position of controls & switches.
Set to proper level
Clean compensating port
Inspect. Repair as necessary
Clean piston(s) seal
Educate operator
Loose wheel hub or bearings
Check wheel and hub for abnormal movement.
Brake disc warped or excessively worn
Replace disc
Brake disc misaligned or loose
Inspect and repair as necessary
Noise is from other source (chain, axle, hub, disc or
wheel)
If noise does not change when brake is applied check
other sources. Inspect and repair as necessary
Wrong pad for conditions
Change to a softer or harder pad
Summary of Contents for 2004-2005 Sportsman 6x6
Page 1: ...SPORTSMAN 6X6 6 59 0 18 31 504 SPORTSMAN 6X6 6 59 0 18 31 504...
Page 58: ...MAINTENANCE 2 38 NOTES...
Page 78: ...GENERAL INFORMATION 3 20 CYLINDER HEAD EXPLODED VIEW EH50PL EH50PL...
Page 126: ...GENERAL INFORMATION 4 14 NOTES...
Page 142: ...GENERAL INFORMATION 5 16 NOTES...
Page 198: ...GENERAL INFORMATION 7 30 NOTES...
Page 276: ...ELECTRICAL 10 48 NOTES...
Page 277: ...ELECTRICAL WIRING DIAGRAM 2004 SPORTSMAN 6X6...
Page 278: ...ELECTRICAL WIRING DIAGRAM 2004 SPORTSMAN 6X6 NOTES...
Page 279: ...ELECTRICAL WIRING DIAGRAM 2005 SPORTSMAN 6X6 BUILT BEFORE JULY 12 2004...
Page 280: ...ELECTRICAL WIRING DIAGRAM 2005 SPORTSMAN 6X6 BUILT BEFORE JULY 12 2004 NOTES...
Page 281: ...ELECTRICAL WIRING DIAGRAM 2005 SPORTSMAN 6X6 BUILT AFTER JULY 12 2004...
Page 282: ...ELECTRICAL WIRING DIAGRAM 2005 SPORTSMAN 6X6 BUILT AFTER JULY 12 2004 NOTES...
Page 289: ...31 504 3ULQWHG LQ 86...