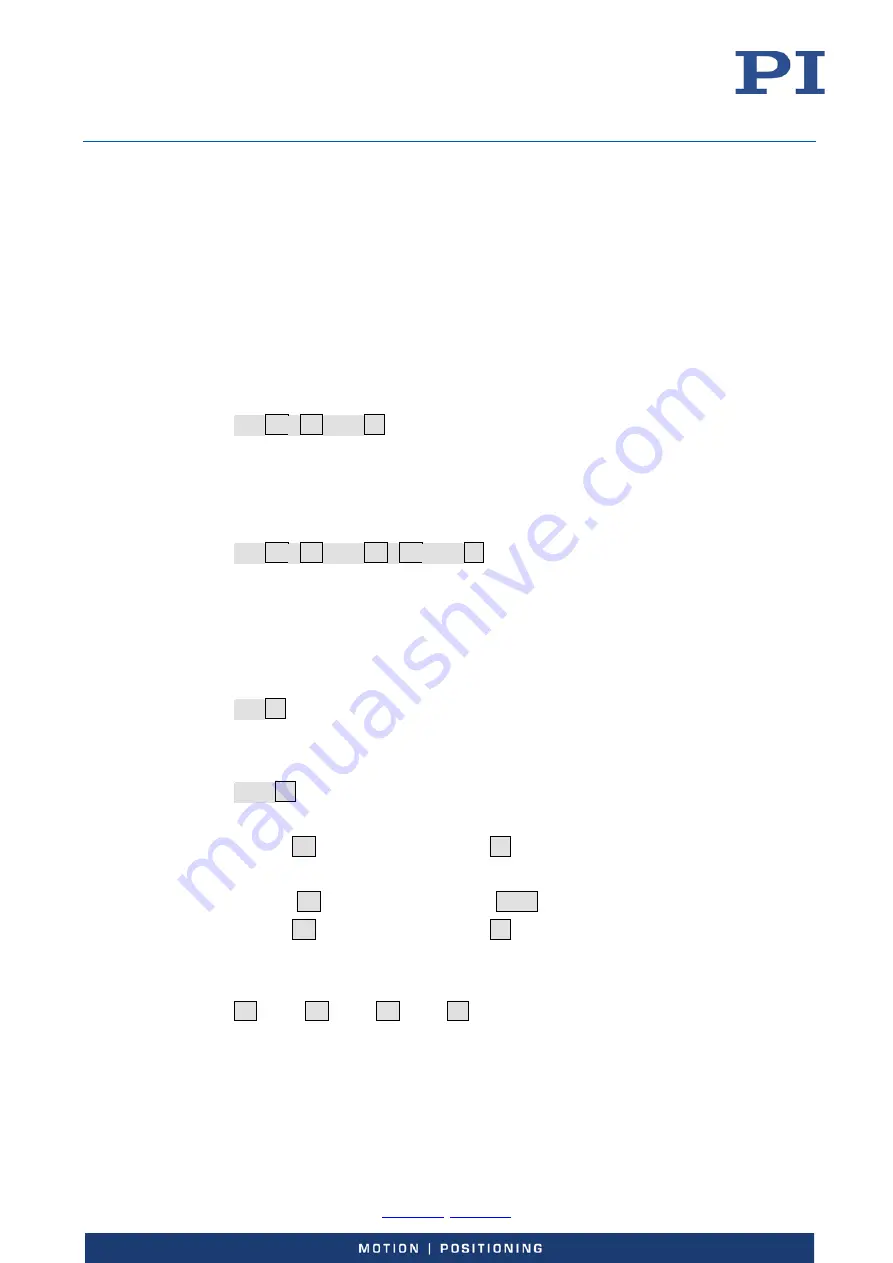
User Manual
E727T0005, valid for E-727
BRO, 2019-06-28
Physik Instrumente (PI) GmbH & Co. KG, Auf der Roemerstrasse 1, 76228 Karlsruhe, Germany
Page 179 / 240
Phone +49 721 4846-0, Fax +49 721 4846-1019, Email
Exception:
Single-character commands are not followed by a termination character. The
response to a single-character commands is followed by a termination character,
however.
The argument <AxisID> is used for the logical axes of the controller. Depending on the controller,
an axis identifier can consist of up to 16 characters. All alphanumeric characters and the
underscore are allowed. See "Axes, Channels, Functional Elements" (p. 22) for the identifiers
supported by the E-727.
Example 1:
Axis 1 is to be moved to position 10.0. The unit depends on the controller (e. g. µm or mm).
Send:
MOV
SP
1
SP
10.0
LF
More than one command mnemonic per line is not allowed. Several groups of arguments following
a command mnemonic are allowed.
Example 2:
Two axes which are connected to the same controller are to be moved:
Send:
MOV
SP
1
SP
17.3
SP
2
SP
2.05
LF
When a part of a command line cannot be executed, the line is not executed at all.
When all arguments are optional and are omitted, the command is executed for all possible
argument values.
Example 3:
All parameters in the volatile memory are to be reset.
Send:
RPA
LF
Example 4:
The position of all axes is to be queried.
Send:
POS?
LF
The response syntax is as follows:
[<Argument>[{
SP
<Argument>}]"="]<Value>
LF
With multi-line replies, the space preceding the termination character is omitted in the last line:
{[<Argument>[{
SP
<Argument>}]"="]<Value>
SPLF
}
[<Argument>[{
SP
<Argument>}]"="]<Value>
LF
for the last line!
In the response, the arguments are listed in the same order as in the query command.
Query command:
CMD?
SP
<Arg3>
SP
<Arg1>
SP
<Arg2>
LF