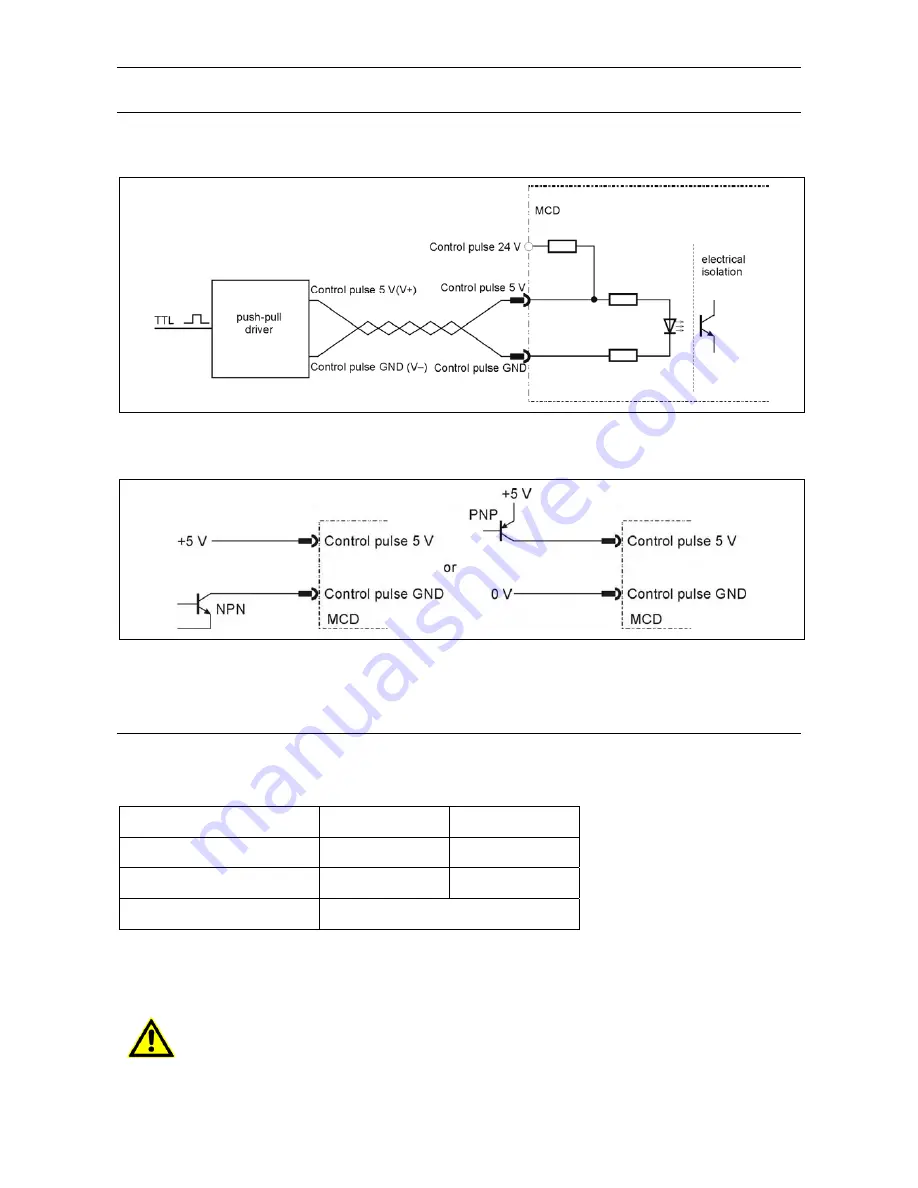
phytron
7.1.1 Push-Pull- or OC-Controlling
We recommend to control the MCD inputs by push-pull drivers. This confers optimum
suppression of disturbances.
Fig. 23:
Push-pull controlling
Alternatively a controlling via open-collector is possible.
Fig. 24:
Open Collector Controlling
7.1.2 Logic Level 24 V or 5 V
MCD power stages can be driven by input level 5 V or 24 V.
The different values depend on the input level:
Signal level
5 V
24 V
High
2.5 – 5.5 V
20 – 30 V
Low
< 0.4 V
< 3 V
Necessary driver current
10 mA minimum
Attention:
Please check the input level applied to the MCD: 5 V or 24 V
and connect the signals to the equivalent pins (see fig. 25)!
Do not connect a 5 V input to 24 V voltage! Danger of damages!
27
MA 2102-A005 GB