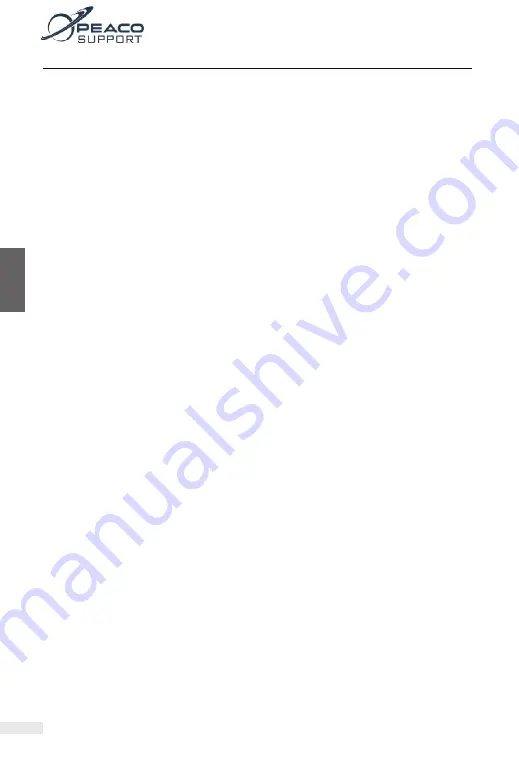
Chapter 3 Installation
Ø
Separated ground connection for peripheral equipments can help to elimi
-
nate the interference from ground wires’leakage current of AC drive while
common
grounding.
3.7.3 Leakage current and treatment
The factors of influencing leakage current over the ground and solutions:
Leakage current has two categories when inverter is in service: One is leaka-
ge current over the ground: and the other is leakage current between lines.
Distributed capacitances exist between wire and ground. The larger
distribu
-
ted capacitances are, the larger the leakage current will be: Effectively decr-
easing the distance between AC drive and motor can reduce distributed cap-
acitances. The larger carrier frequency is, the larger the leakage current will
be. Reducing carrier frequency can decrease leakage current effectively. But
reducing carrier frequency will result in the increase of motor noise, so pleas-
e note this. Installing electric reactor also is an effective method to solve lea-
kage current.
Leakage current will increase with enlargement of loop current,so when the
power of motor is large, the relevant leakage current also will be large.
The factors of influencing electric current between lines and solutions:
Distributed capacitances exit between output wires of AC drive. If the electric
current passing the circuit contains higher harmonic, it may give rise to reso-
nance and leakage current. If you use thermal relay, it may cause false ope-
ration at this time.
The solution is to decrease carrier frequency or install output reactor. We
advise not to install thermal relay before you use the motor of AC drive, but
apply the electronic overcurrent protection function of AC drive.
-34-
C
h
a
p
te
r
3
Peaco Support FC280 Series VFD User Manual
www.peacosupport.com [email protected] Free Shipping Worldwide Reliable Supplier
PEACO SUPPORT