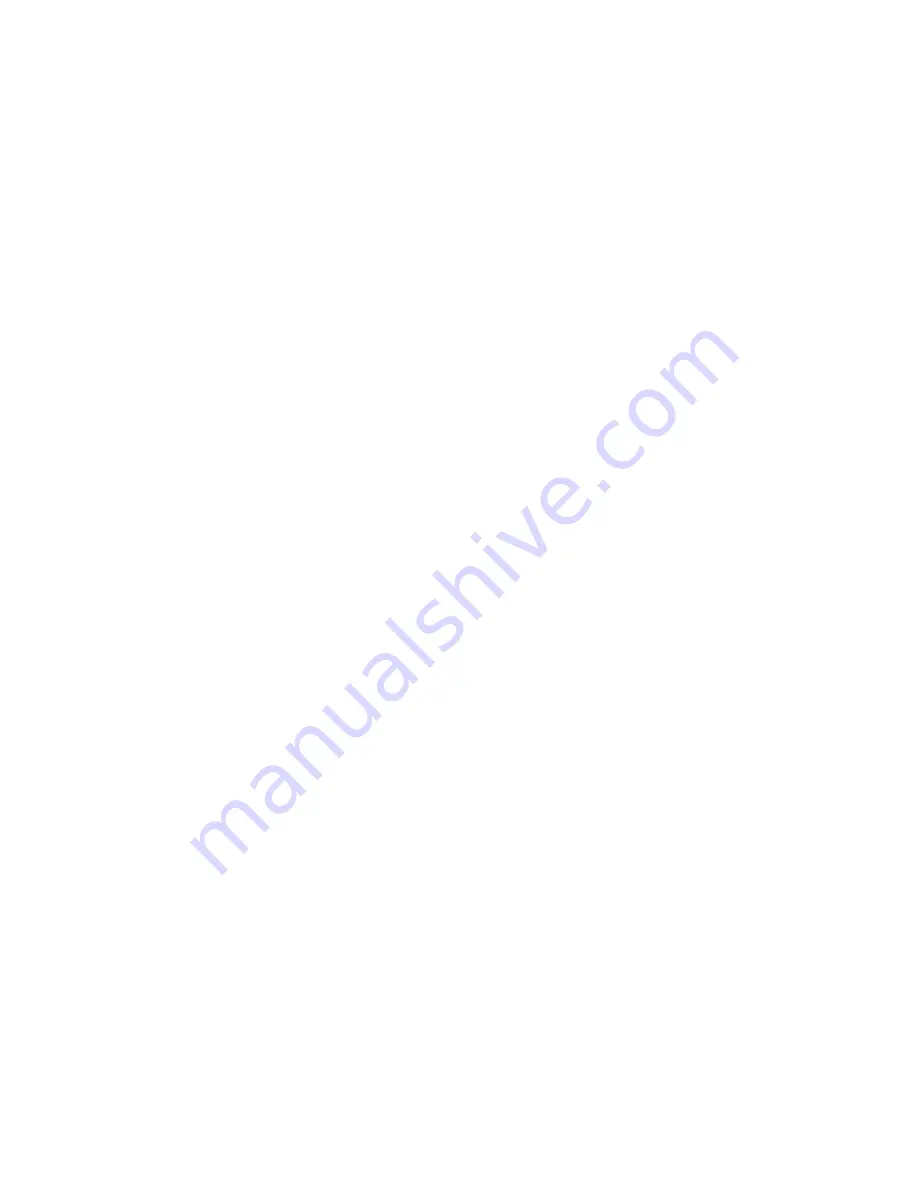
➃
Troubleshooting
5 7
Overvoltage
The TQ10 Drive monitors the voltage on the motor output terminals. If the voltage rises
above a threshold level, the drive will shut down power output to the motor, and will
illuminate
red
the bicolor LED labeled
RED = OVERVOLTAGE
. Excessive regeneration is
the primary cause of an overvoltage fault.
This is a latched fault. To resume operations, cycle power; or, with the TQ10 Torque
drive, you can use the reset input.
Undervoltage
The TQ10 Drive monitors the voltage on its AC power input terminals. If the voltage falls
below 80VAC, the drive will shut down and activate its fault output. When you apply
power to the drive, the power-up event is indistinguishable from an undervoltage;
therefore, the undervoltage fault is not latched. Furthermore, an undervoltage fault will
unlatch any other faults that may be present at the time of the undervoltage.
There is no LED indicator for an undervoltage fault.
Foldback
A mechanical jam in a servo system can cause the motor to overheat. In contrast to a
stepper motor, which does not run hotter when jammed, a servo will apply full current (for
full torque) while it attempts to move as commanded. Usually, this current will be
much
higher than the motor can withstand continuously. If it persists indefinitely, it may damage
the motor’s windings.
To help protect the motor from overheating, the TQ10 has a
current foldback
circuit. If
high motor current persists for too long, the circuit can cause a fault, or reduce the current
to a lower level that decreases the rate of motor heating.
Three of the DIP switches on top of the drive allow you to set the maximum current the
drive will produce (“
PEAK CURRENT LIMIT
”). These switches should be set to a value
no greater than three times the continuous current rating (Ics) of the motor used. This
setting is used by the foldback circuitry to help protect the motor.
Six of the DIP switches configure the foldback circuitry. Three of them set the time that
“high” current will be permitted before the foldback circuitry takes action. Settings range
from 1 to 10 seconds. One switch defines what constitutes “high” current. This is set
according to Ics. One switch will cause a latched fault to be generated when the selected
time at high current is exceeded, otherwise current is reduced (“folded back”) to 40% of
the peak current limit setting. One switch allows foldback to be disabled entirely. See
Chapter 2—Installation
and
Chapter 4—Tuning
(Tuning Procedure) for instructions on
setting the dip switches.
How Foldback Works
When actual current produced by the drive exceeds the threshold (relative to the peak
current limit) set with SW2-2, the foldback circuit illuminates the
PEAK CURRENT
LED
green, and starts a timer. If the current remains above this threshold for longer than the
time set with the time-at-peak dipswitches, the foldback circuit activates, and the IN
FOLDBACK
LED illuminates red. The circuit can generate: A) A latched fault, if so
configured, or B) reduce current to 40% of the peak current limit setting.
In case A (with
SW2-1 ON
), the fault will remain until power is cycled, or the
RESET
input is asserted. This fault condition will be indicated by a red
MOTOR FAULT
LED, and
an active
FAULT OUT
signal. The
IN FOLDBACK
LED may go out when the
MOTOR
FAULT
comes on, depending on the load. When faulted, the motor current will be reduced
to zero.
In case B (with
SW2-1 OFF
), the current reduction will persist until the command input
goes below the actual current, when the circuit will once again allow the full current
permitted by the peak current limit setting. While foldback is limiting the current, the
IN
FOLDBACK
LED will be red. When the command is reduced, the LED will go out. The
FAULT OUT
will not go active, since current foldback is not considered a fault.
Artisan Technology Group - Quality Instrumentation ... Guaranteed | (888) 88-SOURCE | www.artisantg.com