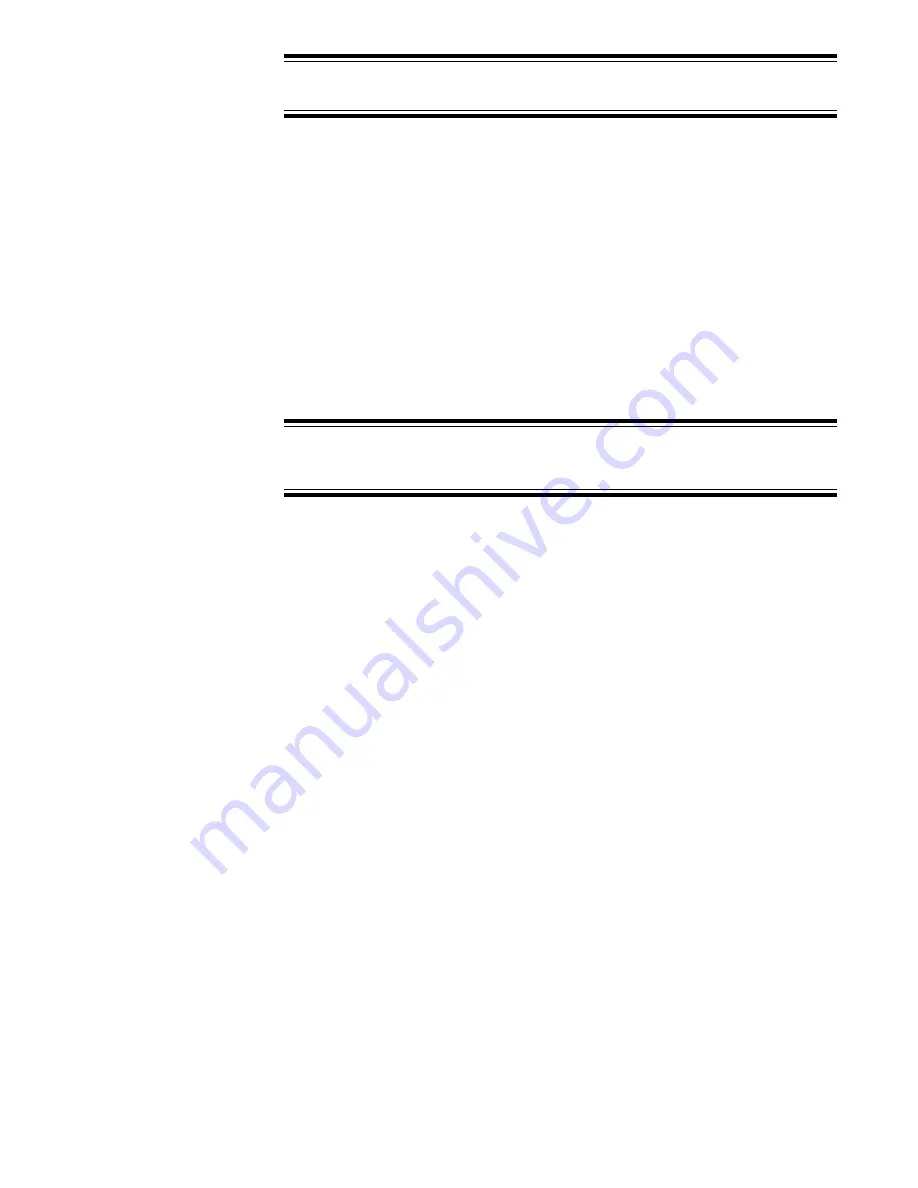
➁
Installation
33
WARNING
The motor case and drive are grounded through the AC power connector ground pin. You
must provide a proper AC power ground for safety purposes.
Peak Power Ratings
The amount of power the TQ10 draws from your AC power source depends upon the motor
you use and upon your specific application. For high power applications, we suggest you
use a dedicated 20 amp service for the TQ10. Even applications that use low
average
power
may require 20 amp service if the
peak
power is high. Inadequate AC power can cause
various problems that are difficult to diagnose.
8. Test Your System
Except for connecting the motor to the load, system installation should be complete at this
point. Perform the test procedure below to verify that your system is functioning properly.
In the test procedure, you will command single revolution moves in the clockwise and
counterclockwise direction. If your mechanics do not permit such moves, choose a move
that allows you to easily verify correct system response.
CAUTION
If you have an SM or NeoMetric Motor, use the drive’s DIP switches to set the peak current
at twice the motor’s continuous current rating, or less. Motor damage due to excessive
heating may result from the combination of high peak current and improper tuning values.
Test Procedure
➀
Apply 120VAC power. The bicolor LED labeled
GRN = POWER ON
should be illuminated
green.
➁
Command a slow move of one revolution in the clockwise direction. Verify that the motor
turns as commanded.
➂
Command a slow move of one revolution in the counterclockwise direction. Verify that the
motor turns as commanded.
➃
Test any of the optional inputs and outputs that you have connected.
You may need to tune your system before you can obtain motion from the motor. We give
tuning instructions later in this chapter.
Successful completion of this procedure will verify that your controller and motor are
correctly connected to the TQ10, and that the drive is functioning properly.
If the test was unsuccessful, observe the LEDs on the front panel of the TQ10 while you try
the test procedure—they may indicate the cause of the problem. (
Chapter 4, Troubleshoot-
ing
has a complete description of LED functions.) Review earlier sections of this user
guide, verify that you have completed each step, and try this test procedure again.
If the test is still unsuccessful, proceed to
Chapter 4, Troubleshooting
for problem identifi-
cation and solution procedures.
9. Connect the Motor to the Load—Couplers
Your mechanical system should be as stiff as possible. Because of the high torques and
accelerations of servo systems, the ideal coupling between a motor and load would be
completely rigid. Rigid couplings require perfect alignment, however, which can be
difficult or impossible to achieve. In real systems, some misalignment is inevitable.
Therefore, a certain amount of flexibility may be required in the system. Too much
flexibility can cause resonance problems, however.
These conflicting requirements are summarized below.
•
Maximum Stiffness (in the mechanical system)
•
Flexibility (to accommodate misalignments)
•
Minimum Resonance (to avoid oscillations)
The best design may be a compromise between these requirements.
Artisan Technology Group - Quality Instrumentation ... Guaranteed | (888) 88-SOURCE | www.artisantg.com