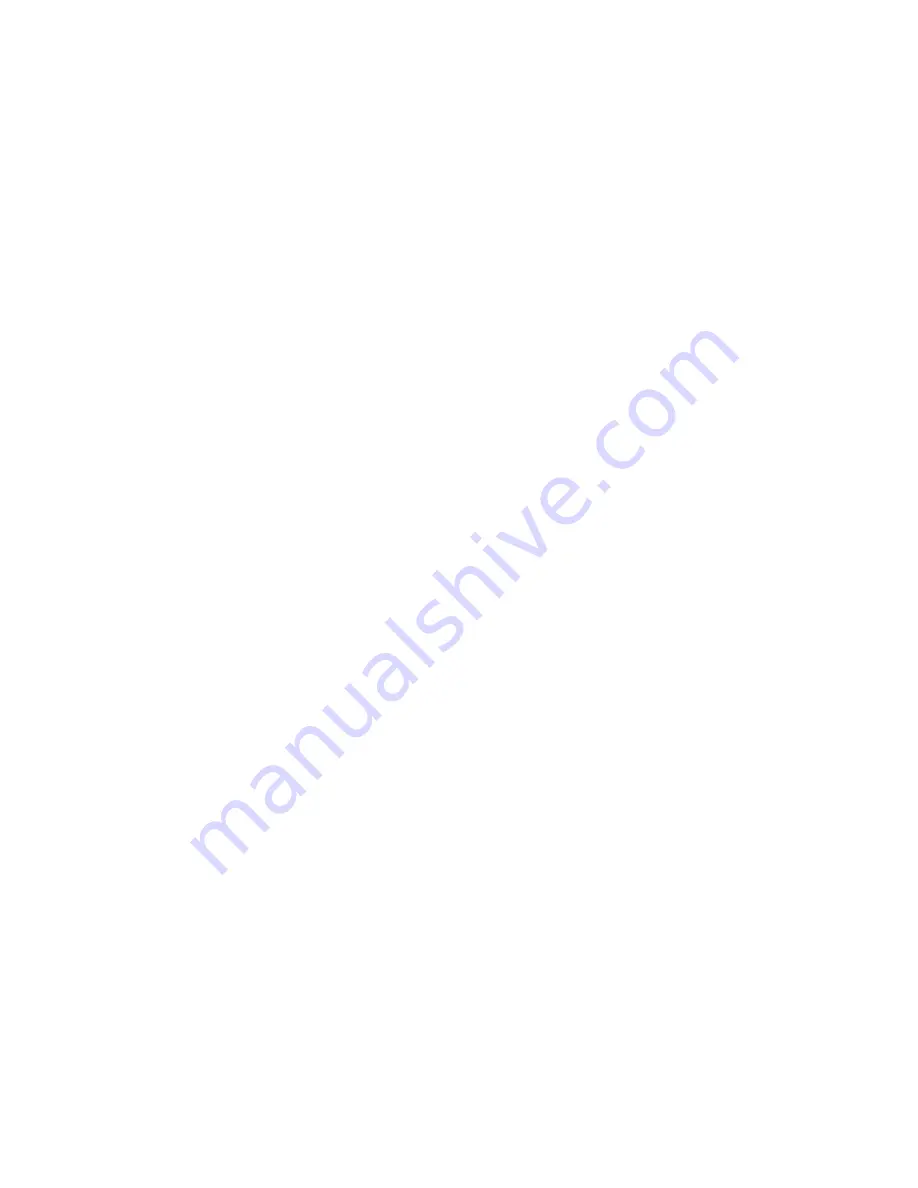
Parker
Hannifin
Command Language Reference (Online Help System in the ACR-
View software).
The feedback device is counting backwards. Use either:
AcroBASIC remedy: Change the MULT command setting to either
+4 or –4 to reverse feedback polarity (not applicable for SSI
feedback devices).
Hardware remedy: Depending on the feedback device used, do
one of the following:
If your application can change how the feedback device is
mounted, you may be able to affect the count direction with
it.
For Quadrature feedback, switch Encoder CHB+ and Encoder
CHB
−
between the controller and the feedback device.
For Step and Direction feedback, switch Encoder CHB+ and
Encoder CHB
−
between the controller and the feedback
device.
For CW and CCW feedback, switch both the CW and CCW
signal pairs between the controller and the feedback
device.
For SSI feedback, switch the Drive AOUT+ and Drive AOUT
−
connection between the controller and the drive. (If the
drive does not support differential outputs, switching the
connections will not work.)
Note:
Some SSI encoders may
have a polarity input that can be set to change the count
direction.
3. If the drive holds torque when you disable the axis, and loses torque
when you enable the axis, check the value of the Drive Enable Output
Shuts Down Drive flag. Some drives implement reverse functionality of
the disable and enable settings.
Stepper Axes
For problems with the stepper axes, check the conditions listed below and
follow the recommended steps.
1. If the direction of motion is reversed, take one of the following actions.
AcroBASIC remedy: Change both the
STEPPER GAIN
and
MULT
settings (
MULT
is not applicable for SSI feedback devices, nor
required if no feedback device is used). This reverses both the
polarity of the commanded direction and the feedback direction.
Hardware remedy:
For Step and Direction mode, switch the Drive Di and Drive
Direction
−
connection between the controller and the drive.
For CW and CCW mode, switch the CW and CCW signal pairs
between the controller and the drive.
Swap the A+ and A
−
connections between the drive and the motor.
2. If the stepper is unstable, follow these steps.
Verify that you have attached the axis as a stepper and not as a servo.
For more information, see the
ATTACH
command in the ACR
Chapter 4 Troubleshooting 107
www.comoso.com
Summary of Contents for ACR9000
Page 1: ...www comoso com ...