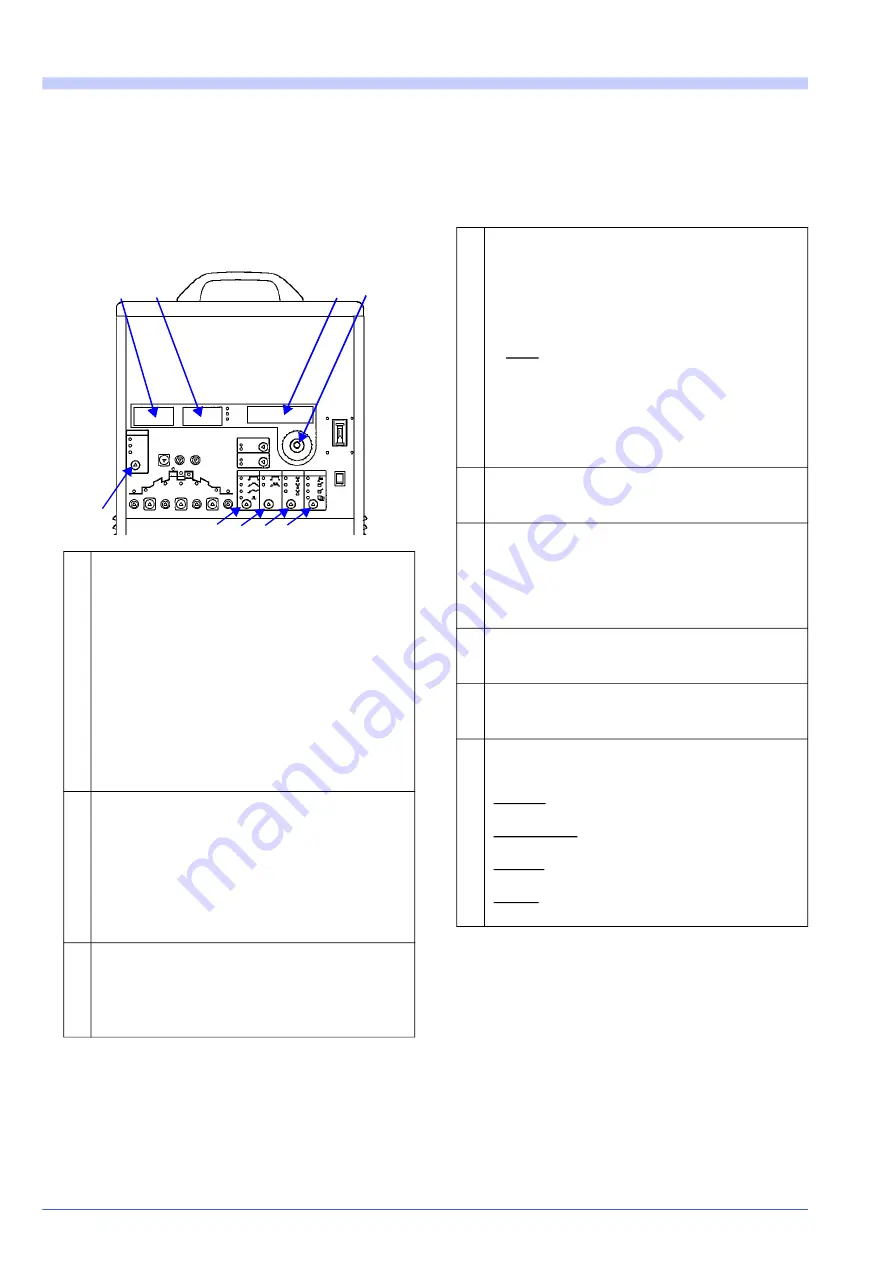
Names and Functions
OMCTT5639E09
18
4. Names and Functions
4.1 Front panel
4.1.1 Data display/setting section and welding conditions selecting section
For details of functions, see “Welding conditions” in this
chapter.”
*1
: In the case of a welding voltage, indicates the welding
voltage (between output terminals of this product) during
the welding operation rather than the set value.
*2
: See section “Operation” for how to display welding volt
-
age.
1
Digital ammeter
• Indicates welding current values during the weld
-
ing. (Displays an average current value mea
-
sured during the period of 0.4 second in
amperes.)
Due to a rounding error, a resulting value may
vary within the range of plus or minus 1A.
As this ammeter is designed to display an aver
-
age current value measured during the period of
0.4 second, it may not be able to follow the varia
-
tion of current quickly enough when the current
changes frequently during the pulse welding, etc.
• Indicates an “Err” (error) mark in case of a trou
-
ble.
2
Set-value display
• Indicates the set values
*
1
of current (A), time (S),
frequency (Hz), pulse width (%), AC balance (%),
DC ratio (%), welding voltage (V)
*
2
, etc.
• The unit display lamp changes according to the
type of indicated set values.
• Indicates an “Err” (error) number in case of a
trouble.
3
LCD display
• This is the information display area.
• Indicates condition-setting items in letters.
• Indicates error contents in letters in case of a
trouble.
1
2
3
4
5
7 8 9
6
4
Jog dial
• This is a dial to carry out the function of a potenti
-
ometer (setup of current and time).
For example, to set welding current to 125A, turn
the dial to the right (increase) or to the left
(decrease) until such a value is indicated (on the
set-value display).
Note: Turning the jog dial without discretion may
result in the change of a set value for the item
currently indicated on the LCD display.
• Use the press button function of the jog dial in the
following situation.
In the reproduction, storage or details mode (See
item 9 in the right column.)
5
“Weld conditions” selection button
Selects a required welding method (DC TIG, AC
TIG or MIX TIG).
6
“Crater control” selection button
Regarding the selected welding method, selects
the “absence, presence or repeat” of the crater
control, as well as the “spot” (arc spot welding).
The arc spot welding can be done only in the case
of “DC TIG” and “AC TIG” welding.
7
“Pulse” selection button
Regarding the selected welding method, selects
the absence or presence” of pulses.
8
“AC waveform” selection button
In case the AC welding method is selected, selects
an AC waveform (standard, hard or soft).
9
“Mote” selection button
Selects an operation “mode” of this product (weld
-
ing, reproduction, storage, or details).
Welding: Can be used to set welding conditions
and conduct a welding operation.
Reproduction: Can be used to reproduce stored
welding conditions.
Storage: Can be used to store the present welding
condition.
Details: Can be used to change the factory-set
mode of this product.
Summary of Contents for YC-300BP2YAF
Page 10: ...Rated Specifications OMCTT5639E09 10 2 2 1 Dimensions ...
Page 16: ...Installation OMCTT5639E09 16 Example of extension cable connection ...
Page 49: ...Parts list OMCTT5639E09 49 9 Parts list ...
Page 52: ...OMCTT5639E09 52 ...
Page 53: ...Circuit diagram OMCTT5639E09 53 10 Circuit diagram NF9 NF8 ...
Page 54: ...Circuit diagram OMCTT5639E09 54 10 1 Enlarged left half NF8 MCB ...
Page 55: ...Circuit diagram OMCTT5639E09 55 10 2 Enlarged right half NF9 ...
Page 62: ...OMCTT5639E09 62 ...
Page 63: ...OMCTT5639E09 63 ...