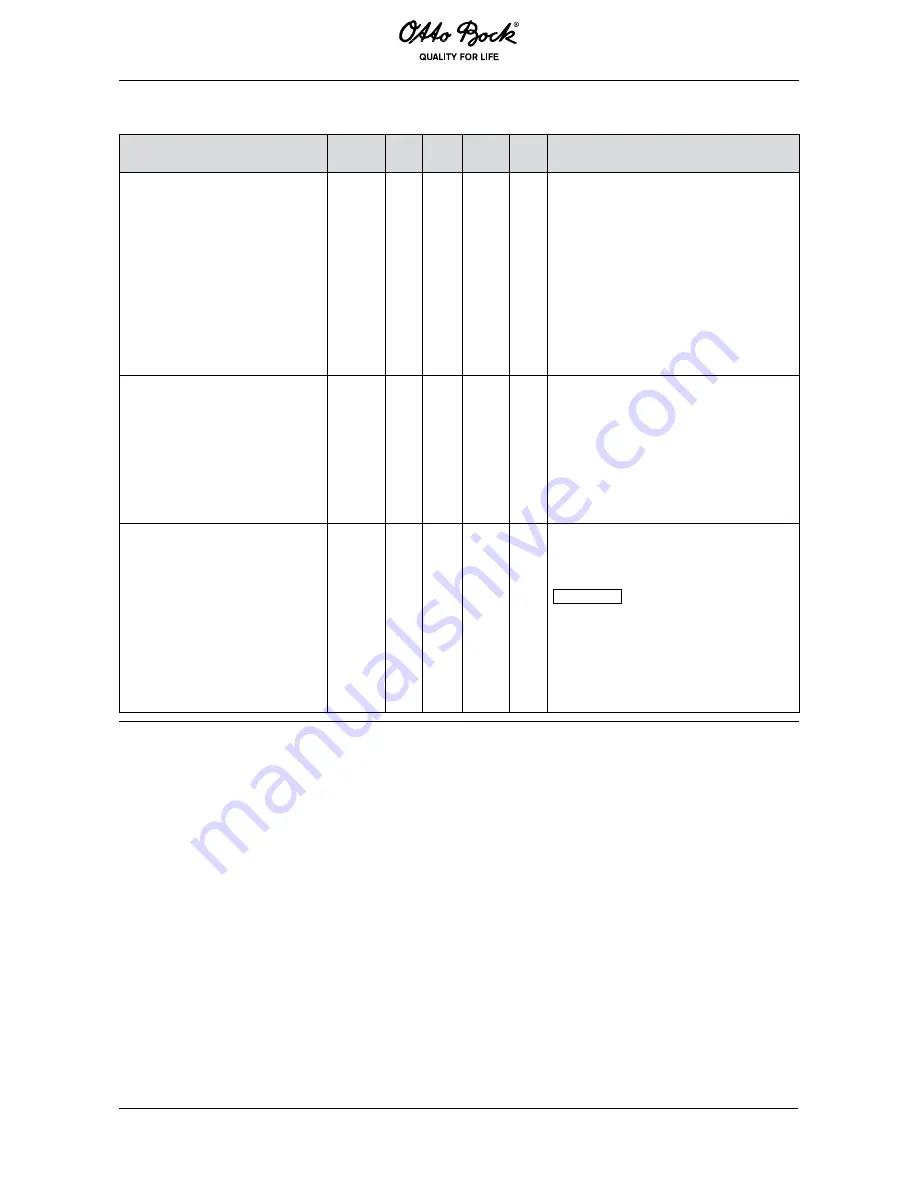
120
8.5.3 “Joystick” parameter settings
Menu tree
Access Min Max
De-
fault
Unit
Help Text
Input devices
> Hand control device settings
> Joystick
> Dead band operation
Service 10
50
20
% Centre dead band
Centre dead band defines the joystick
travel before the system recognises the
command. The value corresponds to a
circle around the joystick zero point.
No movements or commands are
executed unless the joystick is moved
beyond this circle.
Increasing this value is useful if the
operator has a pronounced hand
tremor.
Input devices
> Hand control device settings
> Joystick
> Switch operation
Service Off On
Off
On/
Off
Switch function
The joystick can be used like a switch.
If the switch function is ON, the propor-
tional function is replaced by a switch
function.
Moving the joystick from the centre by
more than 50% generates a 100%
command in the desired direction.
Input devices
> Hand control device settings
> Joystick
> Tremor suppression
Service
0
100
0
% Suppresses a tremor on the joystick.
0% -> Tremor suppression deactivated
100% -> Maximum tremor suppression
INfORMATION
If a brief command is used
for system operation (e.g. if “3 direction
profile” is selected), tremor suppression
should not exceed 90%.
If tremor suppression exceeds 90%
in such a case, the brief command is
ignored.
Table 8 “Joystick” parameter settings
Summary of Contents for C1000 DS
Page 1: ...C1000 DS Service Instructions ...
Page 2: ......