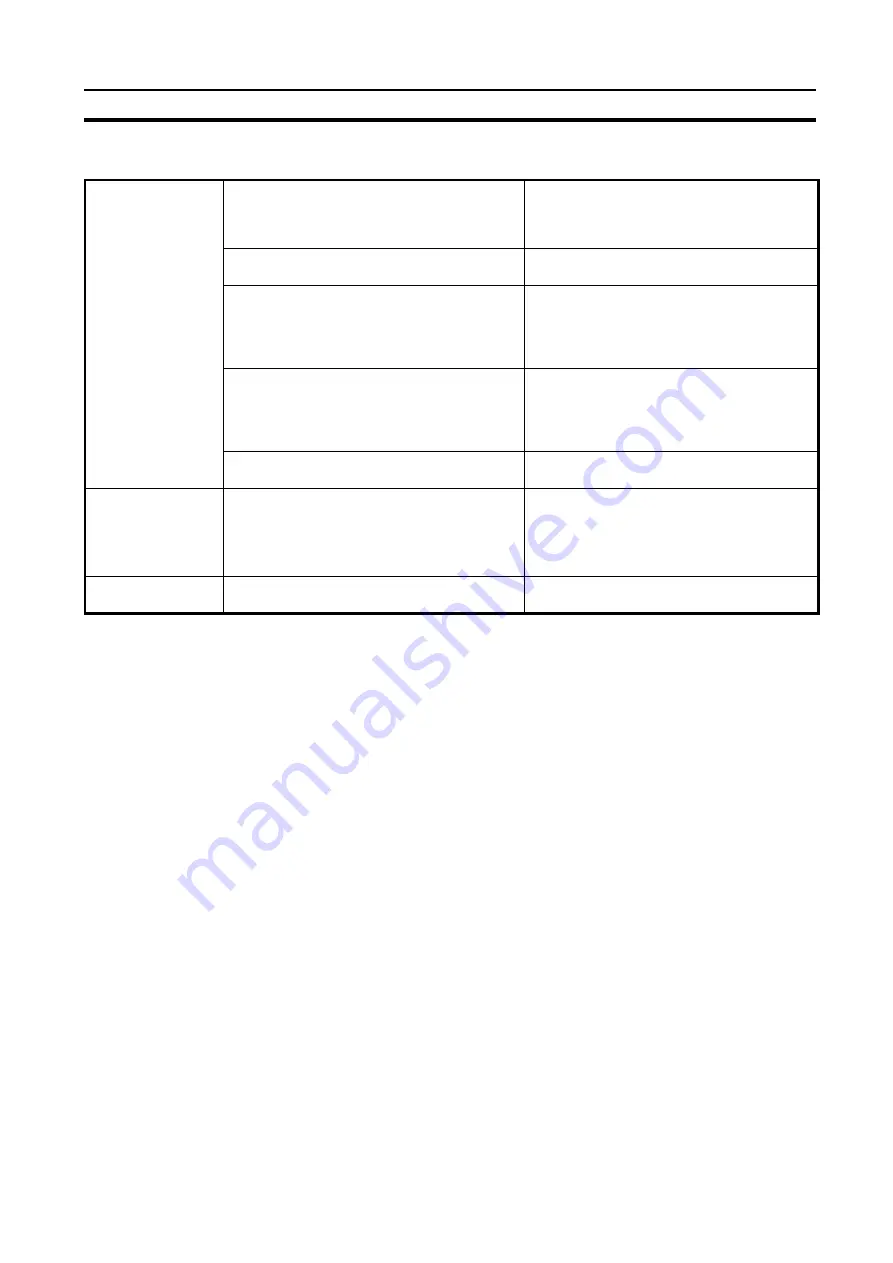
Troubleshooting
Section 7-2
103
Message communication problems
(continued)
No user defined
CAN messages are
received.
The identifier filter was not set or was incorrect.
Check the values of the identifier filter (word n
~ word n+2 of the IOWR message structure)
and execute an IOWR instruction that sets the
identifier filter.
An incorrect PLC start address in the IOWR
message structure was indicated.
Check the PLC start address (word n+3 in the
IOWR message structure).
The network cabling is not correct.
Check if the correct pins of the bus connector
are connected (see section 3-1-5), if there are
no short circuits, if the stub-lines are not too
long, and if the network is terminated at the
appropriate places (see section 3-3-1).
The transmitting node has a 'low-speed' (fault-
tolerant') CAN interface.
'Low-speed' CAN devices use a different
physical layer from the C200HW-CORT21-
V1's 'high-speed' CAN. Converters between
'high-speed' and 'low-speed' CAN are
commercially available.
The Unit operates on a different baud rate than
the other node on the network.
Configure all the units on the network to the
same baud rate.
Not all user defined
CAN messages are
received
The C200HW-CORT21-V1 can buffer up to 15
messages between PLC I/O refreshes. If the
receive buffer is not transferred to the PLC
memory before the buffer overflows, messages
will be lost.
Reduce the data production rate of the
transmitting node.
Reduce the PLC scan time or change to a
lower baud rate (receive buffer is filled at a
lower rate).
ERR LED is
switched ON.
An application error was detected. IR n+3.14 is
set.
Restart the Unit. If this does not help, replace
the Unit.
Summary of Contents for C200HW-CORT21-V1
Page 2: ...C200HW CORT21 V1 CANopen Slave Unit OPERATION MANUAL OMRON Cat No W904 E2 2 ...
Page 3: ......
Page 4: ......
Page 5: ......
Page 6: ...C200HW CORT21 V1 CANopen Slave Unit Operation Manual Produced June 2001 ...
Page 7: ...iv ...
Page 9: ...vi ...
Page 13: ...x ...
Page 47: ...Performance Section 2 3 30 ...
Page 85: ...Control and Status area Section 4 3 68 ...
Page 113: ...Flow diagrams Section 6 6 96 ...
Page 123: ...Maintenance Section 7 3 106 ...
Page 133: ...116 ...
Page 135: ...118 ...
Page 139: ...122 ...
Page 141: ......