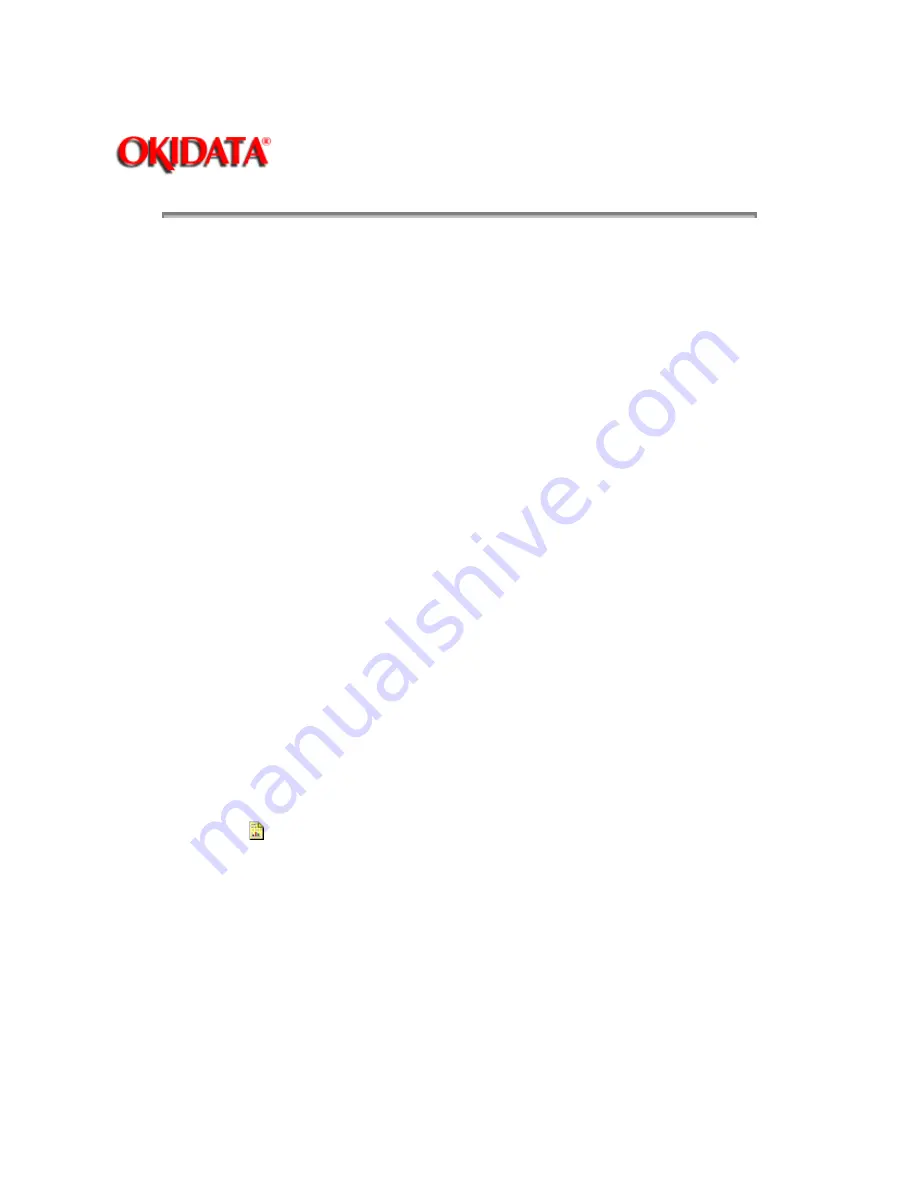
Page: 33
Service Guide ML320/ML321
Chapter 2 Principles of Operation
Head Gap Adjusting Mechanism
The head gap adjusting mechanism adjusts the gap between the platen and printhead by changing
the tilt angle of the carriage frame. This is accomplished by using the adjusting lever.
Moving the adjusting lever rotates the adjusting screw. The adjusting screw is interlocked with the
lever via a gear. Rotating the adjusting screw changes the angle of tilt for the carriage frame. The
printhead is mounted vertically on the carriage frame. Changing the angle of tilt for the carriage
frame moves the printhead closer to, or farther away from, the platen.
The adjusting cam is used to compensate for differences in the printhead gap when measured at
the left and right sides of the platen. Rotating the adjusting cam changes the height of the guide
rail. The height of the guide rail helps determine the distance between the printhead and platen,
when measured at the right end of the platen.
Turning the adjusting cam to the RIGHT will lower the right side of the guide rail.
This causes the printhead gap (on the right side of the platen) to increase.
Turning the adjusting cam to the LEFT will raise the right side of the guide rail. This
causes the printhead gap (on the right side of the platen) to decrease.
The adjusting lever determines the head gap setting.
Setting 1 is for one or two part forms.
Setting 2 is for three or four part forms.
Setting 3 is for envelopes and extra-thick paper.
When the adjusting lever is set to position 3, the distance between the printhead and platen
increases. The electrical contact (attached to the carriage cover) touches a contact pad on the
spacing motor circuit board. This reduces printing speed. Slower speeds ensure adequate
printing pressure.
Refer to Section 3.3 (
) for further details on the Printhead Gap Adjustment.