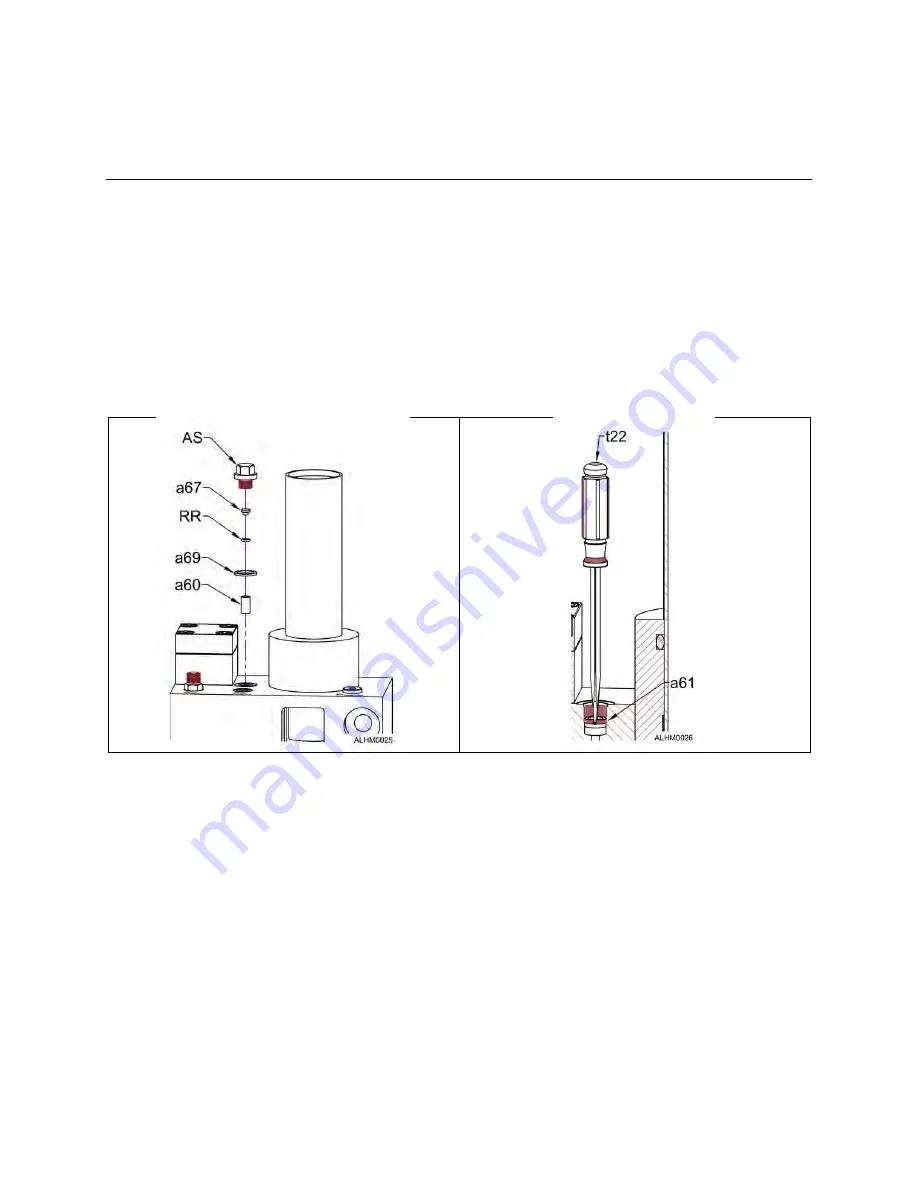
- 47 -
REPLACEMENT OF THE FILTER AND
DIAPHRAGM
For replacement of the filter and diaphragm, you must first remove the plug (AS). Then
you can remove the filter thrust piece (a67), oring (RR), sealing ring (a69) and strainer
(a60). Use a slotted screwdriver (t22) to remove the diaphragm (a61).
NOTE: Upon re-installation, make sure that the sealing edge of the diaphragm is
not damaged.
After re-installing the diaphragm, you can insert the strainer, the oring, and the thrust
piece. Keep them in place using the plug and sealing ring.