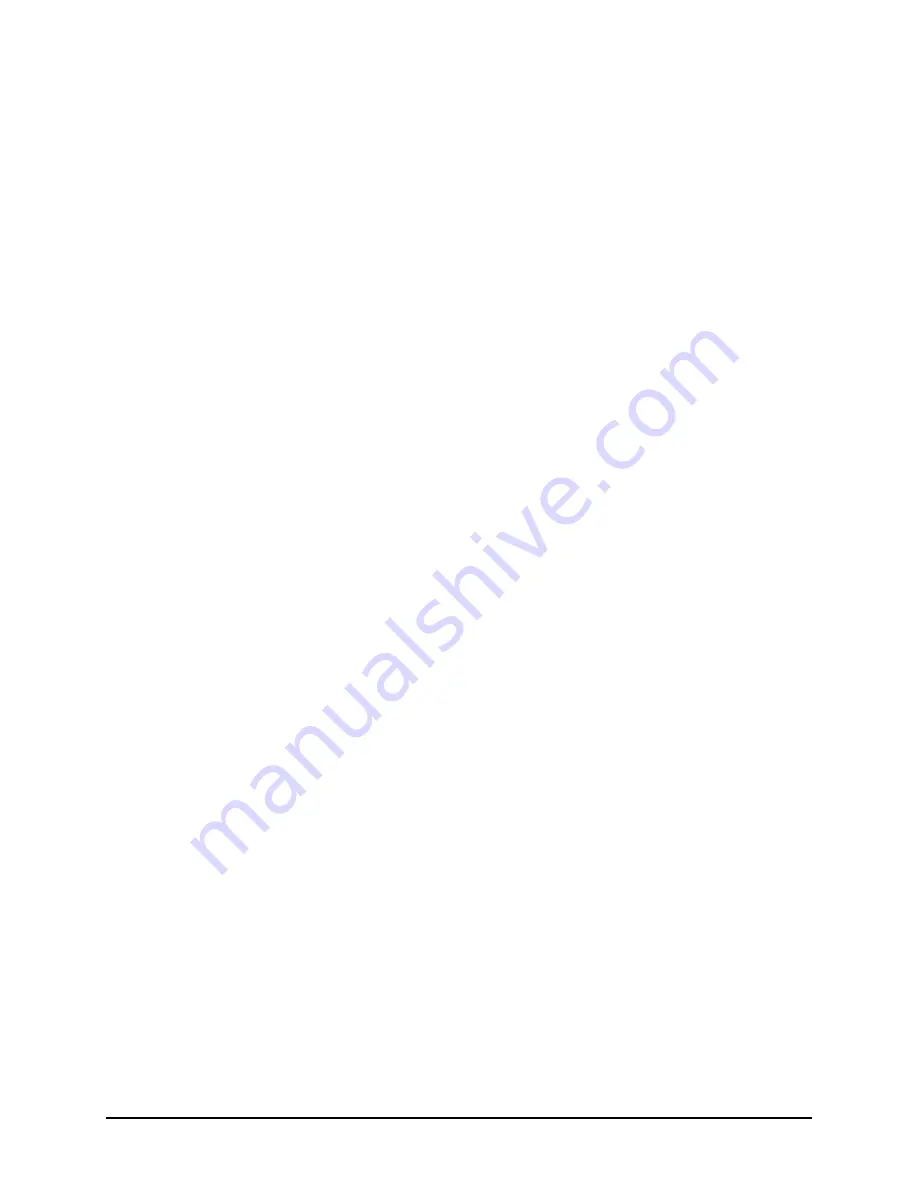
Calibration and Adjustment
5-29
5.16 Adjusting Manual Airflow for Impingement Heaters
NOTES
This procedure applies to S2-900 Series systems equipped with impingement heat.
This procedure does not apply to systems configured with optional Controlled Process
Heat (CpH). See
Airflow to impingement heaters is adjusted by turning the applicable flowmeter adjustment knob located
in the lower front cabinet door. Airflow is read on the gauge on the front of the flowmeter (Figure 5-34).
Factors to be considered when determining the airflow include the following:
•
Maximum airflow is 4.0 SCFM.
•
Size, weight, and securing of the workpiece (high airflow can cause
movement/misalignment).
•
Effect of airflow on the time it takes to heat the workpiece to dispensing temperature.
•
Effect of airflow on how fast the heat tooling reaches/maintains steady-state temperature.
•
Ambient temperature of the dispensing area and its effect on dispensing fluid properties
(pot life, viscosity, cure time).
To adjust the flowmeters:
1.
Locate the impingement air valve and flowmeters in the front cabinet of the dispensing
system (Figure 5-34).
Depending on system configuration, there can be up to six flowmeters (pre-queue,
dispense, and post-queue for Conveyor 1 and Conveyor 2).
The pre- and post-queue flowmeters are located below the pre- and post-queue stations.
2.
Open the impingement air valve by turning the handle counterclockwise so that it is parallel
with the airline. Listen for leaks.
If there is an air leak, identify the source, shut off the air valve, and fix the leak before
proceeding.
3.
While monitoring the readouts on all flowmeters, turn the flowmeter adjustment knobs
counterclockwise until maximum airflow is achieved.
The flow indicators should show an increase in airflow.
4.
While monitoring the readouts on all flowmeters, turn the flowmeter adjustment knobs
clockwise to lessen the flow.
The flow indicators should show a decrease in airflow.
5.
Restore maximum airflow and open the dispensing system hatch. Verify air is coming out
of the holes in impingement heater at each conveyor station.
6.
If air is not flowing out of the heater, check the pneumatic connections.
Summary of Contents for Spectrum II S2-900 C Series
Page 2: ......
Page 36: ...1 22 Introduction 1 11 8 Rear View Open Figure 1 9A S2 900 Rear View Open 1 2 3 4...
Page 40: ......
Page 124: ......
Page 157: ...Calibration and Adjustment 5 33 Figure 5 38 Dispense Lift Table Controls...
Page 159: ...Calibration and Adjustment 5 35 Figure 5 40 Beacon Configuration Window...
Page 186: ......
Page 197: ...Troubleshooting 7 11 Figure 7 1 Scale Setup Menu Figure 7 2 Scale Error Message...
Page 200: ......
Page 215: ...Parts Replacement 8 15 Figure 8 11 Replacing a Panel Mounted Fuse...
Page 218: ......
Page 223: ...Specifications 9 5 Top View mm Back View mm Figure 9 2 S2 900 System Dimensions 2 of 2...
Page 225: ...Specifications 9 7 Top View mm Back View mm Figure 9 4 S2 9XXC System Dimensions 2 of 2...
Page 228: ...A 2 Appendix A Material Safety Information A 2 1 Multemps PS NO 2...
Page 229: ...Appendix A Material Safety Information A 3...
Page 230: ...A 4 Appendix A Material Safety Information...
Page 231: ...Appendix A Material Safety Information A 5...
Page 232: ...A 6 Appendix A Material Safety Information...
Page 233: ...Appendix A Material Safety Information A 7...
Page 235: ...Appendix A Material Safety Information A 9...
Page 236: ...A 10 Appendix A Material Safety Information...
Page 237: ...Appendix A Material Safety Information A 11...
Page 238: ...A 12 Appendix A Material Safety Information...
Page 239: ...Appendix A Material Safety Information A 13...
Page 240: ...A 14 Appendix A Material Safety Information...
Page 246: ......
Page 252: ......
Page 258: ......