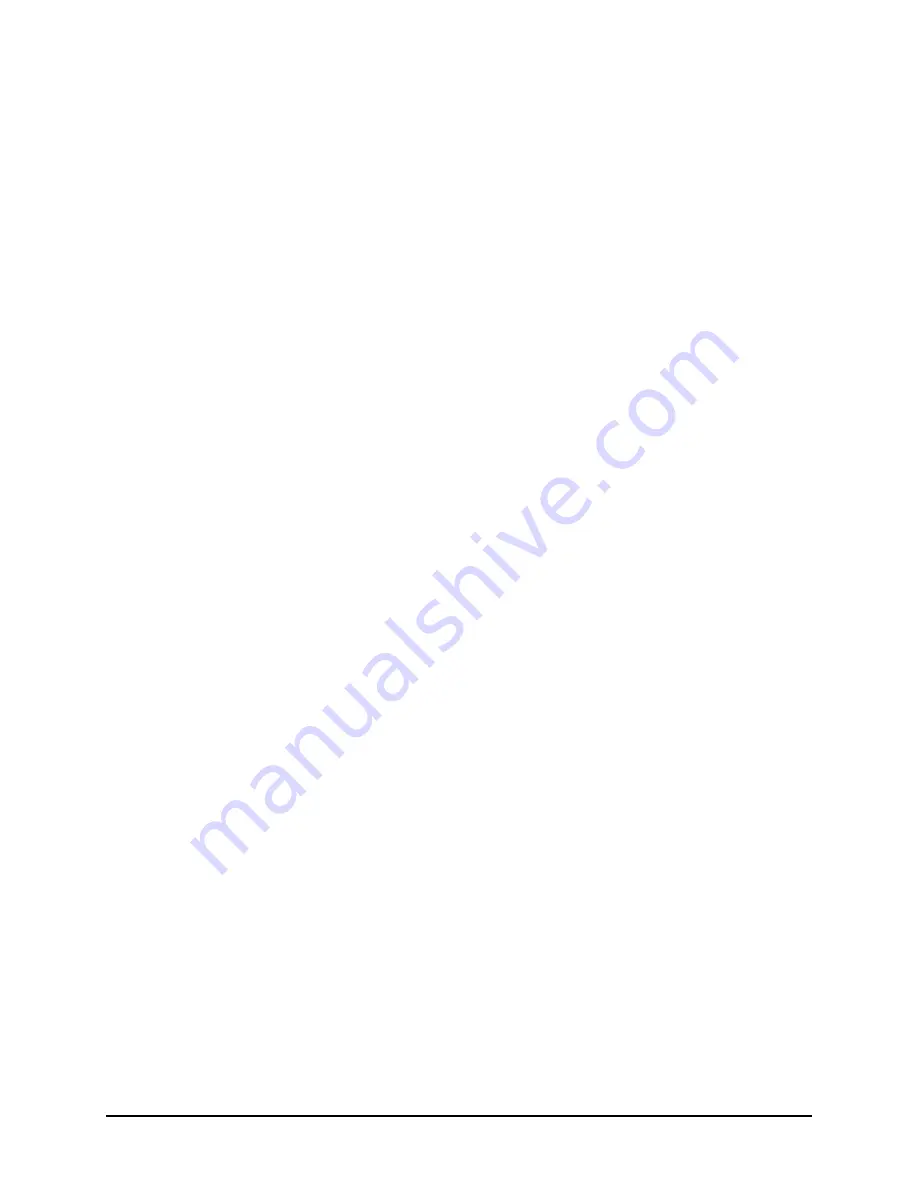
1-8
Introduction
1.10.12.2 Controlled Process Heat
Nordson ASYMTEK’s Controlled Process Heat (CpH) software increases functional control that
eliminates operator interaction altogether. Software-managed heat levels are provided (e.g., warm up,
process ramp, cool down, etc.) with programmable shut-off timers and “step-down” or “no-heat”
capability when a part is not present. CpH control improves yield and “thermal footprint” efficiency by
requiring less power. See
1.10.12.3 Needle/Nozzle Heat
The Needle Heater is an RTD-controlled heating element that provides needle heat on the DV-7000 and
DV-8000C dispensing valves and nozzle heat for the DispenseJet valves. The Needle Heater heats the
dispensing fluid to control the fluid temperature at the needle tip, protecting the rest of the fluid from
chemical reactions or property changes that can occur if the entire reservoir is heated. The DispenseJet
has dual-ended control allows the machine to ensure the correct fluid temperature regardless of ambient
machine temperature. Nozzle heating is integrated into the NexJet and IntelliJet assemblies and is
programmed in the Fluidmove software.
1.10.13 Height Sensor
The CCD non-contact Laser Height Sensor (LHS) is standard on all S2-900 systems. The LHS provides
high-speed dispense height measurement for components that may be compromised by tactile sensing.
Specialized circuitry automatically controls the duration of laser emission, preventing measurement errors
due to surface color and texture variations. Three LHS models are available. Contact Nordson
ASYMTEK to determine the best fit for your application requirements. An optional Mechanical/Tactile
Height Sensor is also available.
1.10.14 Interlock
The Interlock is a built-in safety feature that automatically removes dispensing system servo and
conveyor motor power, stopping all dispensing activity, when the hatch is opened. This prevents
personnel from being injured by movement of the dispensing head and conveyor.
1.10.15 Light Beacon
A highly visible light beacon indicates system status and can warn the operator when fault conditions
exist. The beacon has an audible alarm and four different color lights which can be constantly on (solid)
or flashing.
Software and hardware share control of the beacon lights. Sometimes hardware-driven displays override
those caused by software conditions, and vice versa. Safety critical conditions always have priority.
Flashing light software conditions have priority over solid light conditions. See
for
additional information.
1.10.16 Low Fluid Sensor
1.10.16.1 Fluidmove Software Low Fluid Tracking
Fluidmove keeps track of material usage during the dispense operation if the initial syringe fluid weight
(mass) is entered in the recipe. Both low and critically low values can be monitored. When a low fluid
condition is detected, the light beacon is activated to warn the operator. Additionally, the Fluidmove
software displays user warnings for low fluid conditions in the Run Window.
Summary of Contents for Spectrum II S2-900 C Series
Page 2: ......
Page 36: ...1 22 Introduction 1 11 8 Rear View Open Figure 1 9A S2 900 Rear View Open 1 2 3 4...
Page 40: ......
Page 124: ......
Page 157: ...Calibration and Adjustment 5 33 Figure 5 38 Dispense Lift Table Controls...
Page 159: ...Calibration and Adjustment 5 35 Figure 5 40 Beacon Configuration Window...
Page 186: ......
Page 197: ...Troubleshooting 7 11 Figure 7 1 Scale Setup Menu Figure 7 2 Scale Error Message...
Page 200: ......
Page 215: ...Parts Replacement 8 15 Figure 8 11 Replacing a Panel Mounted Fuse...
Page 218: ......
Page 223: ...Specifications 9 5 Top View mm Back View mm Figure 9 2 S2 900 System Dimensions 2 of 2...
Page 225: ...Specifications 9 7 Top View mm Back View mm Figure 9 4 S2 9XXC System Dimensions 2 of 2...
Page 228: ...A 2 Appendix A Material Safety Information A 2 1 Multemps PS NO 2...
Page 229: ...Appendix A Material Safety Information A 3...
Page 230: ...A 4 Appendix A Material Safety Information...
Page 231: ...Appendix A Material Safety Information A 5...
Page 232: ...A 6 Appendix A Material Safety Information...
Page 233: ...Appendix A Material Safety Information A 7...
Page 235: ...Appendix A Material Safety Information A 9...
Page 236: ...A 10 Appendix A Material Safety Information...
Page 237: ...Appendix A Material Safety Information A 11...
Page 238: ...A 12 Appendix A Material Safety Information...
Page 239: ...Appendix A Material Safety Information A 13...
Page 240: ...A 14 Appendix A Material Safety Information...
Page 246: ......
Page 252: ......
Page 258: ......