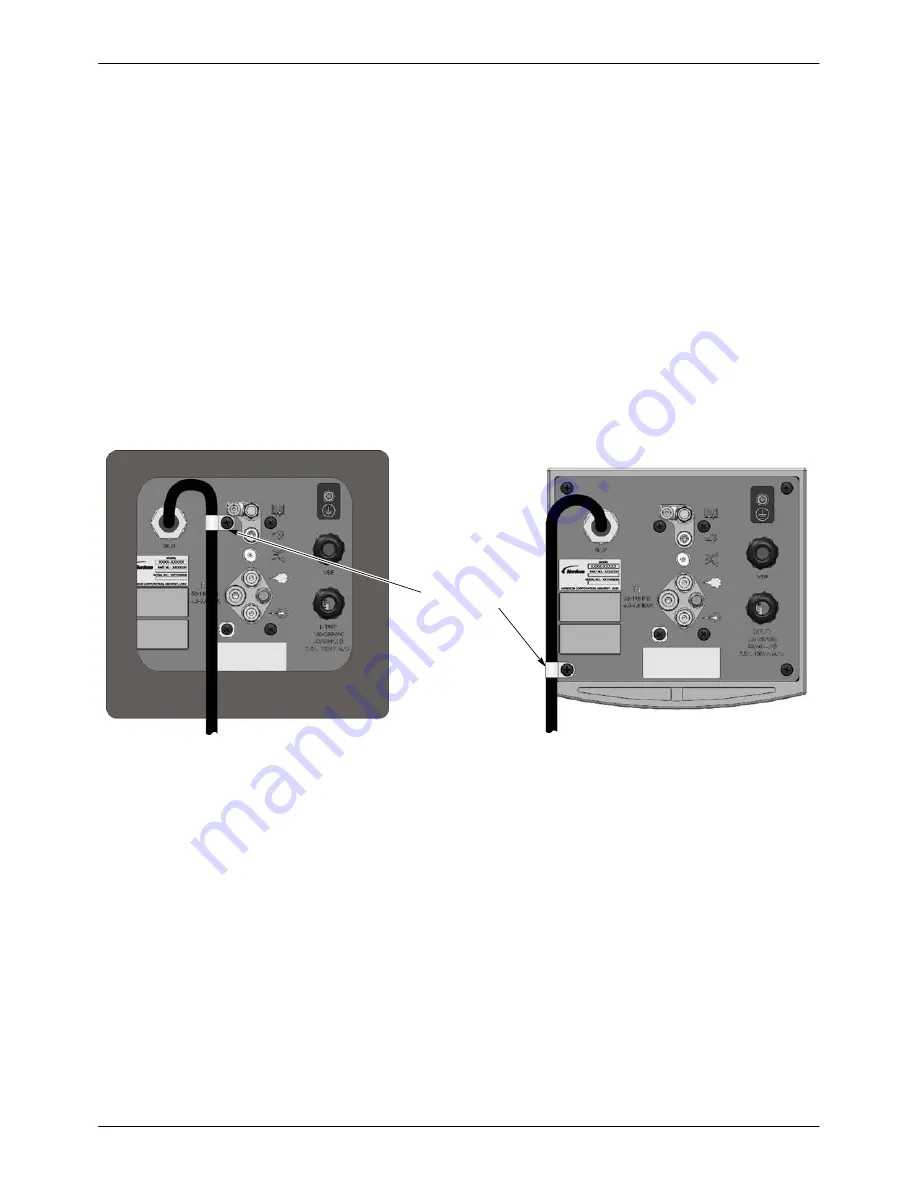
System Setup
3-11
Part 1604857-04
E
2014 Nordson Corporation
Spray Gun Connections
Unpack the spray gun. Uncoil the cable, the 4-mm clear and 6-mm black air
tubing, and the 11-mm powder hose. Make the following connections:
Gun Cable
1. Connect the gun cable to the GUN receptacle on the rear panel of the
controller. The cable plug and receptacle are keyed.
2. Thread the cable nut onto the receptacle and tighten the nut securely.
3. Secure the cable strain relief to the rear panel with one of the existing
panel screws.
Mobile System
Rail/Wall Mount System
Strain Relief
Figure 3-11 Gun Cable Connection and Strain Relief Mounting
Summary of Contents for Encore LT
Page 4: ...Change Record ii Part 1604857 04 E 2014 Nordson Corporation ...
Page 12: ...Safety 1 4 Part 1604857 04 E 2014 Nordson Corporation ...
Page 34: ...System Setup 3 18 Part 1604857 04 E 2014 Nordson Corporation ...
Page 56: ...Troubleshooting 5 8 Part 1604857 04 E 2014 Nordson Corporation ...
Page 68: ...Repair 6 12 Part 1604857 04 E 2014 Nordson Corporation ...
Page 86: ...Parts 7 18 Part 1604857 04 E 2014 Nordson Corporation ...
Page 87: ...Wiring Diagram 8 1 Part 1604857 04 E 2014 Nordson Corporation Section 8 Wiring Diagram ...
Page 88: ...Wiring Diagram 8 2 Part 1604857 04 E 2014 Nordson Corporation ...
Page 92: ...ZONE REV DESCRIPTION BY CHK RELEASE NO DATE SEE SHEET 1 FOR REVISION HISTORY ...