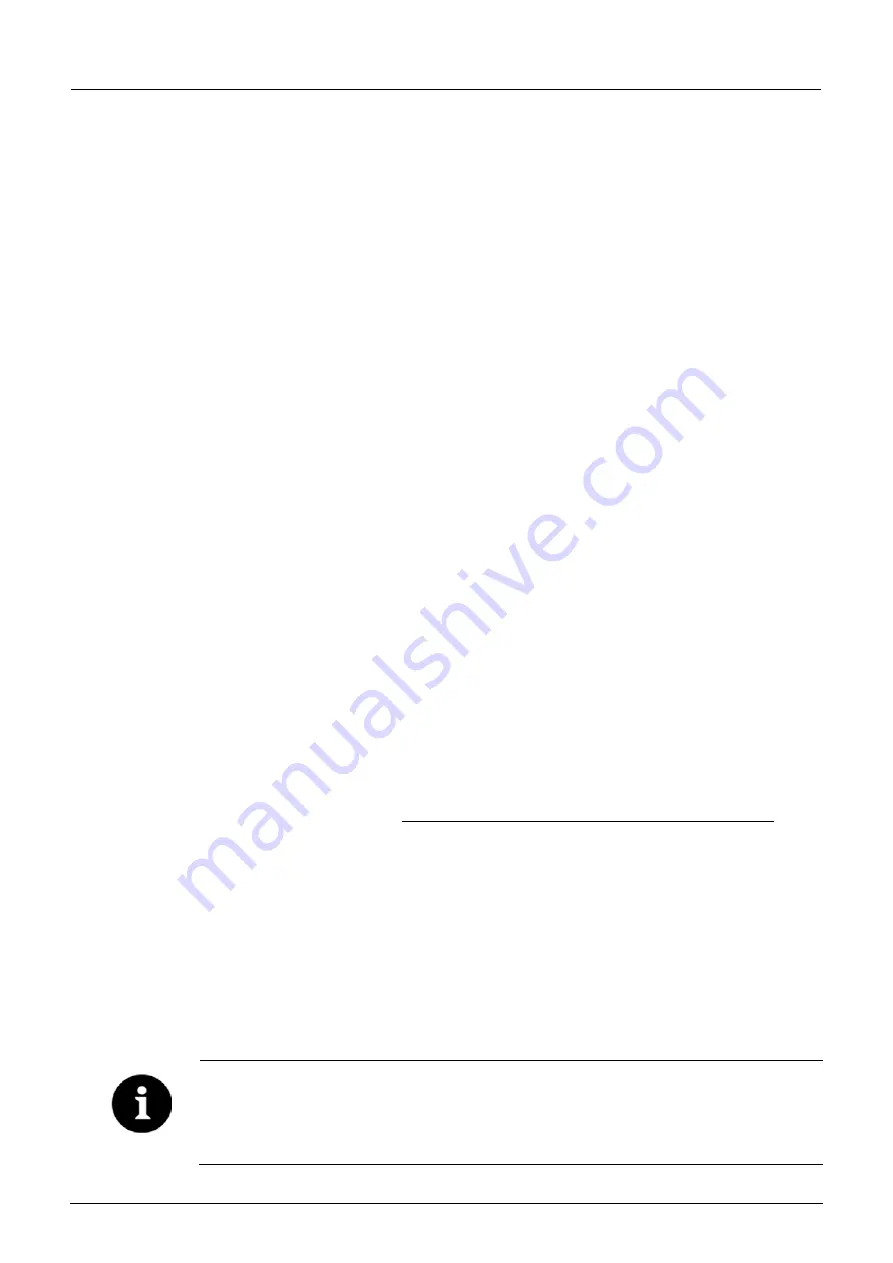
Parameter Setting
OCM F - rev. 05 / 06.04.2018
page 65
>Not active<
The function is disabled.
>Internal set
point<
The set point is determined in the OCM F.
>Max. flow rate<
Enter the max. possible flow rate of the
measurement place here in l/s. This value is
required for improved system control.
>Int. set point<
This parameter is to determine the internal
flow set point in l/s.
>Min. variation<
This parameter defines the permissible set
point deviation of the control system without a
regulating event is allowed to be executed.
The setting reduces the oscillation tendency
of the system. If there is no set point devia-
tion tolerance defined, the system will con-
stantly attempt to exactly adjust the actual
value according to the set point. Due to this
reason the regulating unit might be driven
permanently which may result in mechanical
defects or higher wear and tear. Normally the
deviation should be approx. 10 % of the set
point value.
>Cycle<
The processing interval of the controller.
Short intervals will accelerate the control be-
haviour, but are going to result in oscillation
of the control circuit as from a certain point. A
long interval is going to reduce the oscillation
tendency of the controller but will however
increase inertia of the regulating system.
Interval =
Average flow velocity
• 1,3
Distance between regulating unit and measurement
>Slidevalve
runtime<
Use this parameter to monitor spindle breaks,
slide valve gate breaks, gear defects, power
failures on the regulating unit or other malfunc-
tion sources which may reveal because the
regulating unit does not move although control
signals are being generated.
Slide run time
to be set
=
time between open and closed condition
of slide valve during permanent operation
• 1,2…2,0
Information concerning slide run time
An error message is going to be generated if the controller unit does not reach the end
switch CLOSED after the slide run time has expired (see chapter “21 Operation Mode
(RUN)” sub item “Error messages”).
Summary of Contents for OCM F
Page 105: ...Approvals and Certificates OCM F rev 05 06 04 2018 page 105 Approvals and Certificates...
Page 106: ...Instruction Manual OCM F page 106 OCM F rev 05 06 04 2018...
Page 107: ...Approvals and Certificates OCM F rev 05 06 04 2018 page 107...
Page 108: ...Instruction Manual OCM F page 108 OCM F rev 05 06 04 2018...
Page 109: ...Approvals and Certificates OCM F rev 05 06 04 2018 page 109...
Page 110: ...Instruction Manual OCM F page 110 OCM F rev 05 06 04 2018...