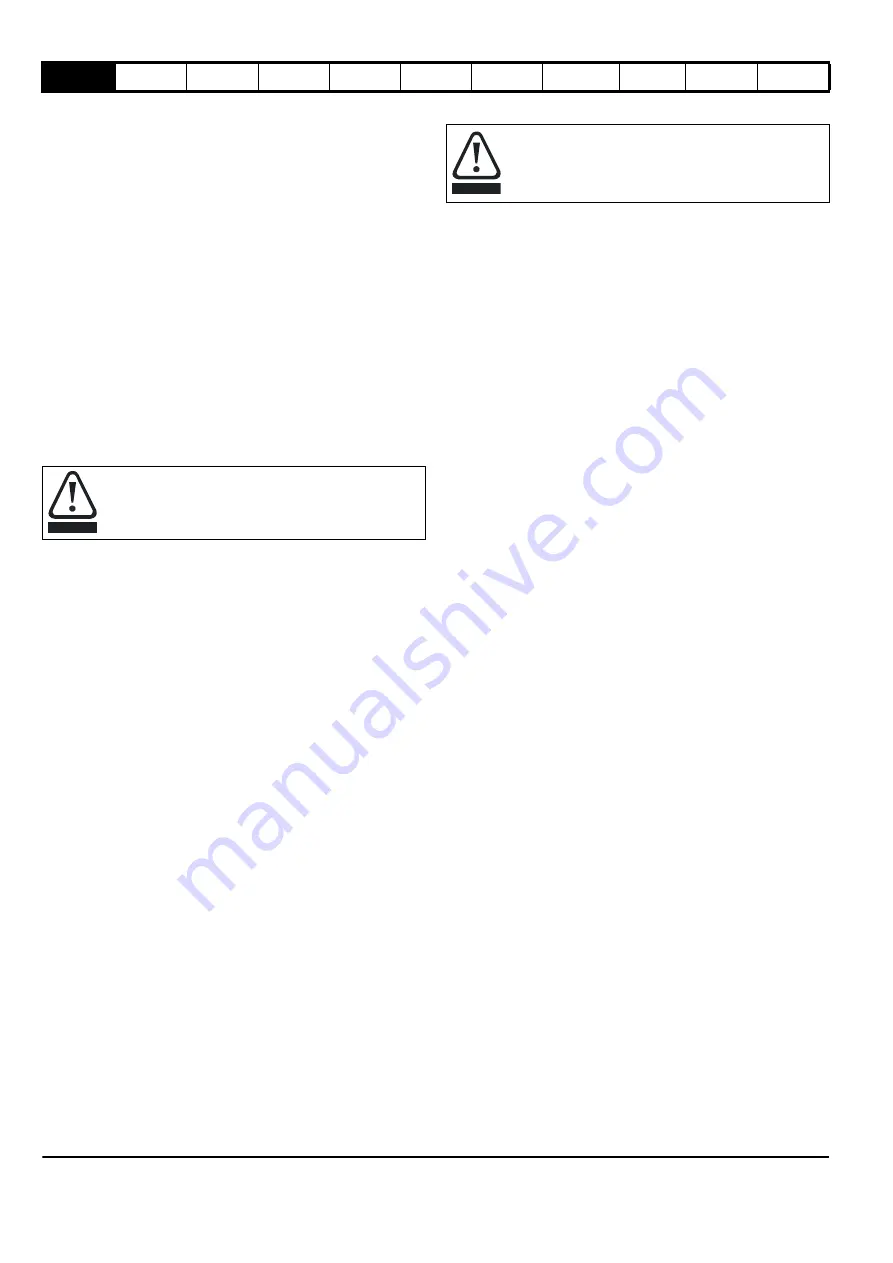
6
Commander S100 User Guide
1.7 Adjusting parameters
Some parameters have a profound effect on the operation of the drive
e.g. enable auto restart. They must not be altered without careful
consideration of the impact on the controlled system and should be
conducted by qualified personnel. Measures must be taken to prevent
unwanted changes due to error or tampering e.g. set
Security PIN
(P4.02) or use a locked enclosure.
1.8 Electromagnetic compatibility (EMC)
Installation instructions for a range of EMC environments are provided in
this User Guide. If the installation is poorly designed or other equipment
does not comply with suitable standards for EMC, the product might
cause or suffer from disturbance due to electromagnetic interaction with
other equipment. It is the responsibility of the installer to ensure that the
equipment or system into which the product is incorporated complies
with the relevant EMC legislation in the place of use.
1.9 Grounding
The drive must be grounded by a conductor(s) sufficient to carry the
prospective fault current in the event of a fault and in a zone of
equipotential bonding. The ground loop impedance must conform to the
requirements of local safety regulations.
If the EMC filter disconnect screw is fitted (as delivered)
The protective earth shall be two conductors of the same cross-sectional
area and material as the supply phases or the minimum size of the
protective earthing conductor to comply with the local safety regulations
for high protective earthing conductor current equipment.
Each protective earth conductor including the protective earth conductor
to the motor must use a separate means of connection. Four tapped
holes are provided (2 x M3 and 2 x M4). If the cable management
bracket is used, then any additional protective earth conductors can be
connected to the cable management bracket.
If aluminium cables are used, then the copper cross-sectional areas
should be increased by 60 %.
If the EMC filter disconnect screw is removed
If the protective earth conductor is part of the supply cable, the cross
section of the protective earth must have minimum area equivalent to
the supply phases. If individual cores are used the protective earth
should have a minimum cross section area of 2.5 mm² (if copper) with
strain relief or 4 mm² (if copper) without strain relief or have a minimum
area equivalent to the supply phase conductors whichever is the
greatest.
1.10 Fuses and circuit breakers
The A.C. supply to the drive must be installed with suitable protection
against overload to provide branch circuit protection in accordance with
local safety regulations, e.g. the National Electrical Code (NEC), the
Canadian Electrical Code. Failure to observe this requirement will cause
a risk of fire.
The integral solid-state short circuit protection of the drive does not
provide branch circuit protection. Branch circuit protection must be
provided in accordance with the National Electrical Code and any
additional local codes.
Opening or failure of the branch circuit protective device may be an
indication that a fault has occurred and to reduce the risk of fire or
electric shock, the equipment and the branch circuit protective device
should be examined and tested and replaced if damaged.
1.11 RCD
1.12 Safety of the control circuits
The drive is protective class I where user protection from electric shock
is achieved through a combination of insulation and a protective ground.
The control terminals and 485 Communications port are isolated from
the power circuits in the drive by double/reinforced insulation which
meets the requirements for PELV. The installer must ensure that the
external circuits do not compromise this insulation barrier. If the control
circuits are to be connected to circuits classified as Safety Extra Low
Voltage (SELV) - for example, to a personal computer - an additional
basic barrier must be included in order to maintain the SELV
classification.
1.13 Terminal connections and torque
settings
Loose power connections are a fire risk. Always ensure that terminals
are tightened to the specified torques. Refer to the tables in section 4
1.14 Environmental limits
Instructions in this guide regarding transport, storage, installation and
use of the equipment must be complied with, including the specified
environmental limits. This includes temperature, humidity,
contamination, shock and vibration. Drives must not be subjected to
excessive physical force.
1.15 Enclosure
The Basic Drive Module (BDM) must be mounted in an enclosure which
prevents access except by trained and authorized personnel. The BDM
is not a fire enclosure. The BDM is designed for use in an environment
classified as pollution degree 2 by IEC 60664-1. This means that the
environment within the enclosure must be dry, non-conducting
contamination only. Any contamination must not obstruct air flow
1.16 Hazardous environments
The equipment must not be installed in a hazardous environment (e.g. a
potentially explosive environment) unless it is installed in an approved
enclosure and the installation is certified.
1.17 Access to equipment
Access must be restricted to authorized personnel only owing to the risk
of electric shock and the risk of unintended changes to the system
behaviour.
1.18 Routine maintenance
Regular inspections and maintenance should be carried out to ensure
the reliability if the drive is maximized. See detailed information in
section 3.5
.
1.19 Repairs
Users must not attempt to repair a drive if it has failed, nor carry out fault
diagnosis other than through the use of the diagnostic features
described in this User Guide. It must be returned to an authorized
Control Techniques distributor. Users must not make any attempt at
removing drive plastics to inspect the internal parts of the drive.
1.20 Hazardous materials
RoHS, REACH WEEE etc. details are available at www.drive-setup.com/
environment
Touch current in the protective earthing conductor exceeds
3.5 mA.
CAUTION
This product can cause a D.C. current in the protective
earthing conductor. Where a residual current-operated
protective (RCD) or monitoring (RCM) device is used for
protection in case of direct or indirect contact, only an RCD or
RCM of Type B is allowed on the supply side of this product.
CAUTION
Summary of Contents for COMMANDER S100
Page 118: ...0478 0650 02...